For a company that relies on steel assets, there’s nothing worse than spending money, labor hours, and crucial equipment downtime to apply a protective coating meant to preserve your equipment — only to find that the coating has failed, and needs to be replaced.
Choosing an effective, reliable coating is crucial to not only increasing efficiency, production, and safety at your facility but also avoiding the risk that the coating may fail. Traditional coatings have their drawbacks, and a lack of preparation and knowledge can lead to costly coating failure.
In this post, we’ll cover the basics of coating failure, including why it occurs and the associated costs. We’ll then discuss how EonCoat’s revolutionary coating addresses the issues of coating failure head-on.
What is Coating Failure and Why Does it Happen?
Coating failure is the loss or reduction of a coating’s bond strength. There are two types of failure: premature and catastrophic. Premature failure occurs when the coating needs to be replaced before its expected lifespan. Catastrophic failure is sudden, severe destruction of the coating.
Coating failure can occur for a variety of reasons, and oftentimes, as Louis D. Vincent explains in The Anatomy of a Coating Failure, for many reasons at once. Among these include:
- The company’s lack of experience with certain environmental or internal conditions, which can impact the effectiveness of the chosen coating. Abrasion is a typical result of the environmental impact on a coating.
- Improper surface preparation, which can prevent the coating from adhering properly. Blistering, or the appearance of bubbles underneath the coating surface, often results from this oversight.
- Improper application, which can lead to peeling or running of the coating. Pin-holing, for example, can result from improper spray atomization.
- Exposure to substances such as calcium hydroxide, potassium, sodium, or any number of acids that react with chemicals in the coating, causing it to deteriorate.
- Improper mixing of the coating formula, which can lead to a comprehensive ineffectiveness of the coating.
What are the Costs of Coating Failure?
The costs of coating failure to your organization come from two ends: post-failure and prevention. Post-failure costs describe all costs that incur following the onset of coating failure, including:
- Repair of the damaged surface
- Potential replacement of the coating or equipment
- Labor costs associated with repair and replacement
- Revenue lost due to equipment downtime during repair or replacement
In the oil and gas industry, where time is precious and loss of productivity for one piece of equipment for even one day has a huge financial impact, coating failure can put a serious dent in your bottom line.
Of course, these are only the monetary costs to your company. You must also consider worker safety, as some coating failures could create dangerous conditions. Depending on the extent of the failure, nearby areas could also be put in harm’s way. Both worker injury and environmental destruction could lead to reputational damage and a loss of faith in the public eye.
The costs of coating failure aren’t limited to just reactionary expenses after it happens. Organizations also incur steep costs to prevent corrosion failure from occurring. This includes labor and monetary costs for repeated applications of traditional coatings, and revenue lost due to equipment downtime required for prevention methods.
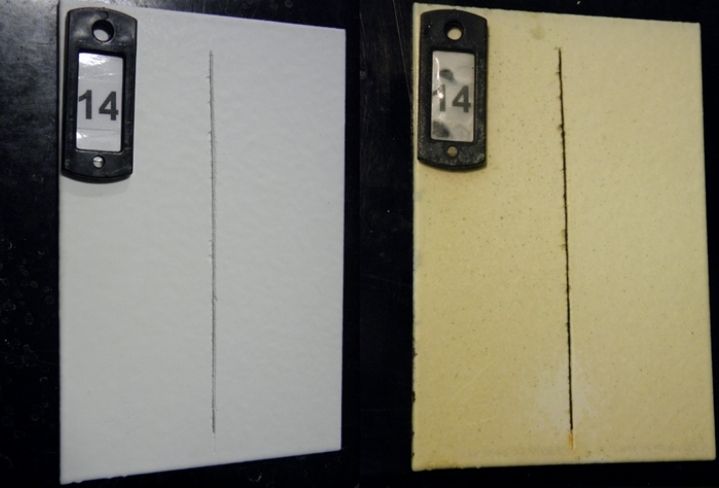
How EonCoat® Reduces Your Risk of Coating Failure
Avoiding the costly damage of coating failure comes down to researching and understanding the properties of the coatings available to you. The best way to avoid coating failure is to choose an anti-corrosion coating that’s well suited to succeed in the environment where you operate.
For the oil and gas industry, EonCoat® is that coating. Not only is it long-lasting, but its patented formula makes it resistant to many factors that cause traditional coatings to fail.
Surface Preparation
With traditional coatings, there’s a lot that can go wrong before the coating is applied. Many coatings need extensive surface preparation, including cleaning and removing flash rust from the surface before application. Errors made during the surface preparation process can render the coating ineffective in a number of ways. The coating may experience blistering, bubbles, or moisture — all of which attack the integrity of the coating itself. At worst, the coating may not adhere to the steel surface properly, leaving the surface vulnerable to corrosion.
EonCoat® requires very little preparation time. All that’s needed is a commercial (NACE-3/SSPC SP-6) blast before EonCoat® can be applied to the steel surface. This can be done in one go, significantly reducing the possibility of errors that could lead to coating failure. EonCoat® can also be applied directly over flash rust, eliminating the need to spend additional time and money cleaning flash rust off the surface of the steel or ‘holding the blast’ once the substrate has been blasted to near white metal. With minimal surface preparation needed, EonCoat® reduces the risk of coating failure and enables a quick return to service for your assets.
Chemical Reactions
Traditional coatings are vulnerable to a number of chemical reactions that may weaken the coating. If exposed to substances like calcium hydroxide or sodium, the hydroxyls of the alkaline substance can break the ester linkage of the coating — a process called saponification. This chemical reaction results in the formation of an organic acid and alcohol, causing the coating to deteriorate and gradually lose strength.
Acidic substances may react with moisture — especially in environments with high humidity, frequent rain, or heavy condensation (dew) on surfaces — to break down chemical bonds in the coating. This can leave the steel surface beneath it unprotected and vulnerable to corrosion.
EonCoat® is far more resistant to chemical attacks than traditional coatings. The acid in EonCoat’s formula enables it to chemically bond with the steel surface, forming an iron phosphate alloy layer. On top of this, a tough ceramic layer forms which not only protects the surface, but also leaches phosphate to re-alloy the steel if necessary. This allows EonCoat® to remain unphased by most chemical attacks. When tested with exposure to alkalis, EonCoat® yielded very little chemical reactivity; in fact, no reactions were seen involving alkalis with a pH of 6 to 12. When tested with exposure to acids, EonCoat® was relatively non-reactive; only acids with a pH of less than 2 yielded reactions.
Environmental Conditions & Abrasion
EonCoat’s outer layer is made of a robust ceramic that is resistant to cracks, punctures, and scratches. With a thickness of 20 mils, the ceramic layer makes EonCoat® up to 10 times stronger against abrasion than epoxies and 16 times stronger than most polymer paints. The chemical makeup of the ceramic layer also doesn’t change during freeze/thaw cycles, making it ideal for use in tougher environments.
The oil and gas industry has for too long endured the struggles of coating failure. EonCoat® offers a solution. Our coating is a comprehensive, effective, and safe corrosion prevention solution that will last longer than any traditional coating. To put it lightly: coating failure has finally met its match.
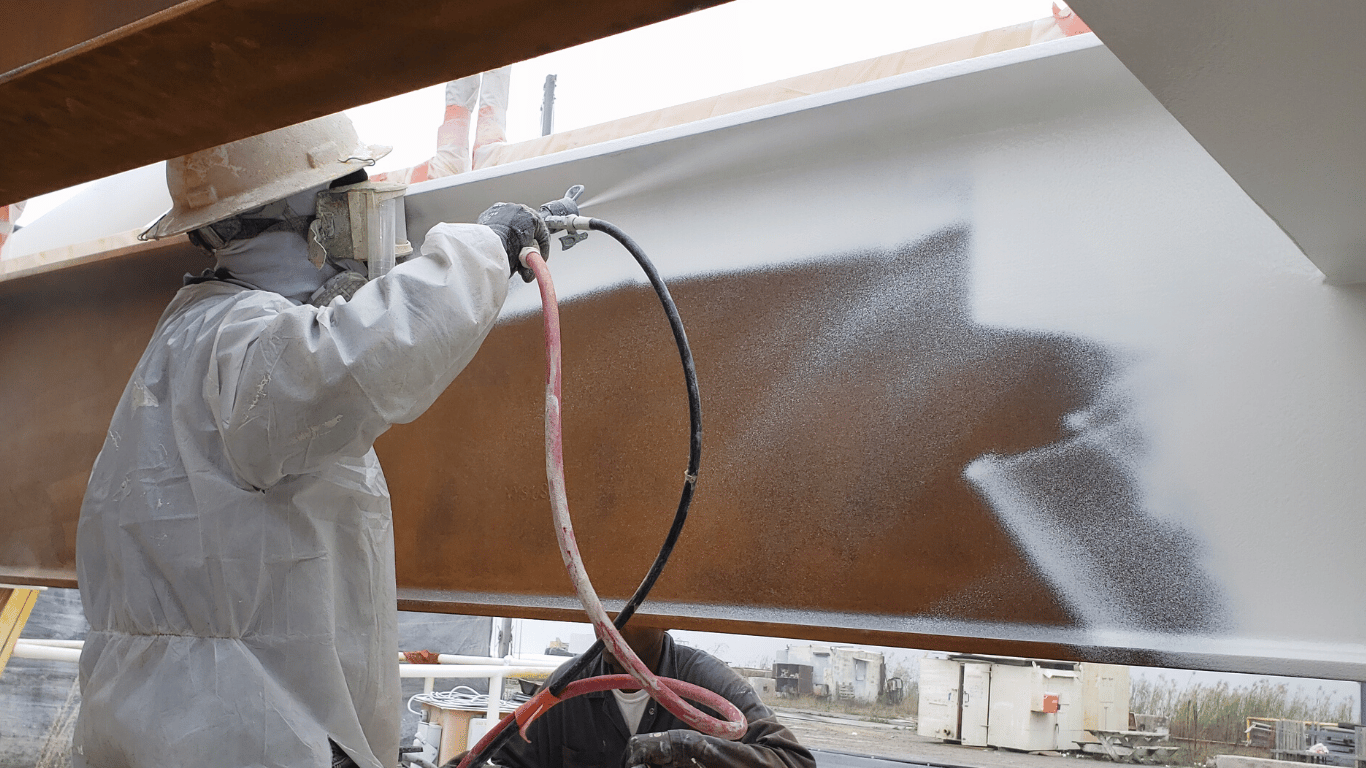
Ready to Learn More About EonCoat?