Facilities in the liquefied natural gas (LNG) sector frequently operate in regions of high humidity, moisture, and rainfall — which makes it challenging for companies to combat the threat of corrosion on their carbon steel assets.
If you work in the LNG sector, you may have already found out firsthand that traditional barrier coatings have significant drawbacks in these environments. It’s difficult to prepare the surface of carbon steel for traditional coating application, and once a coating is in place, the environment presents obstacles that cause traditional anti-corrosion methods to fail.
In this post, we’ll explain what causes these drawbacks, and how EonCoat’s formula holds up in wet and rainy areas to prevent corrosion on carbon steel once and for all.
Moisture Makes Corrosion Worse
Carbon steel, an alloy made of iron and carbon, is susceptible to corrosion of all kinds, particularly atmospheric corrosion from exposure to moisture. These risks are compounded in areas with high humidity and rainfall, which poses a significant problem in the modern LNG sector. China, India, and Pakistan had the greatest growth in LNG trading in 2017, and these regions deal with heavy monsoon seasons.
The risk of corrosion is even higher where marine chlorides are present. Sodium chloride and calcium chloride, which are found in the air and water of marine and coastal environments, accelerate the corrosion process. Heavy and prolonged exposure to moist conditions can also lead to flash rust, which is the appearance and spreading of corrosion within a matter of hours.
These issues put pressure on the LNG sector to find anti-corrosion solutions that are better suited to moist conditions.
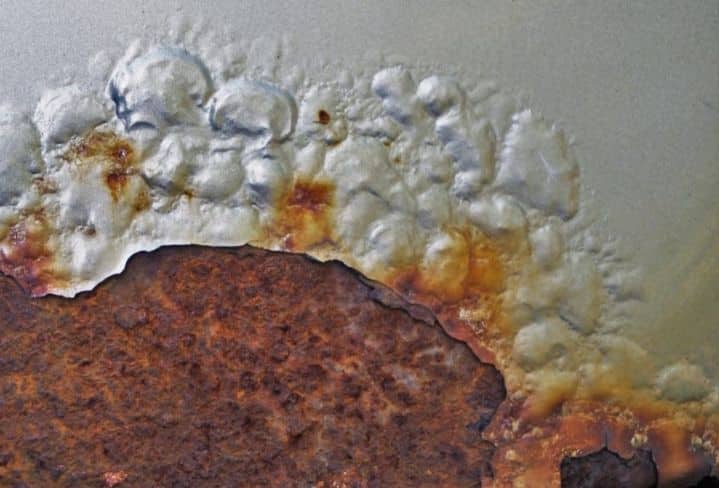
Traditional Coatings Don’t Work for LNG
Traditional coatings simply aren’t cutting it for the LNG industry. These methods need to be reapplied every few years, which is expensive and time-consuming for companies that rely on carbon steel for nearly all of their production. Re-application is also inefficient, as coating companies must send workers out to each LNG company’s facilities which may be located around the globe.
If flash rust has developed, as is common in moisture-rich environments, traditional coatings can’t be applied at all — the flash rust must be fully removed first, adding an expensive and time-consuming process for surface preparation.
There is a solution to helping the LNG sector operate successfully in these wet and humid regions of the world.
How EonCoat® is Helping the LNG Sector
Companies from around the globe are using EonCoat’s chemically-bonded, phosphate ceramic coating as an effective alternative to traditional barrier coatings:
- The Zhoushan LNG Project in China used EonCoat® to protect steel equipment and assets during the construction of an LNG receiving station, LNG terminal, and pipeline connection.
- Florida Power & Light (FPL) used EonCoat® to protect the natural gas pipeline fueling their Martin County Florida power plant, located in the environmentally fragile Barley Barber Swamp.
- The San Diego County Water Authority selected EonCoat® for use on parts of its large aqueduct system, including selected air release valves, blow-offs, and pump wells.
EonCoat’s patented dual-layer system prevents corrosion from ever developing — this has been a game-changer for LNG companies operating in areas with a high risk of corrosion. When applied to the surface of carbon steel, EonCoat® chemically bonds with the steel, forming a 2-micron thick iron phosphate alloy layer. On top of this alloy layer, a 20 mil thick white ceramic layer forms as the second line of defense. The ceramic layer acts as a phosphate reservoir to continuously re-phosphate the steel and keep the alloy layer intact. Since the resulting coating becomes part of the steel, there is no opportunity for corrosion to form.
EonCoat® only needs to be applied once. Because the top ceramic layer serves to continuously re-phosphate the alloy layer if needed, EonCoat® is self-healing. This eliminates the need for companies to invest further time and money into reapplying or repairing the coating after it’s been applied.
Even more importantly for LNG companies who operate in moist environments: EonCoat® can be applied directly on top of flash rust. Surface preparation for EonCoat’s spray-applied coating requires very minimal downtime, and companies don’t need to spend the time or resources to remove flash rust before applying the coating.
The LNG sector doesn’t have to stick to traditional anti-corrosion methods that are costly and inefficient — especially in the high-moisture environments that frequently affect it. EonCoat® not only holds up in moisture-filled environments, but has also been proven to withstand abrasion, chemicals, and high impact. Learn more about your options. Contact EonCoat® to speak to our experts about your corrosion prevention needs.
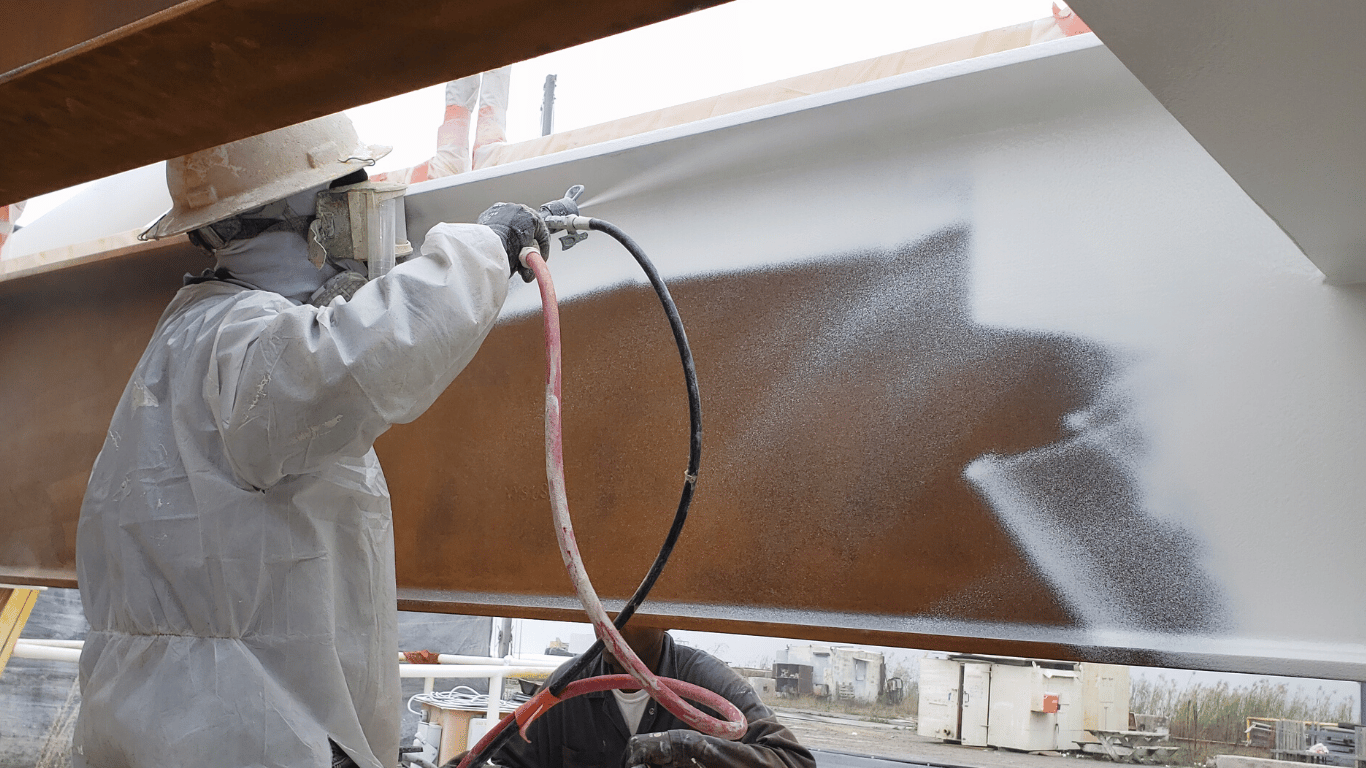
Ready to Learn More About EonCoat?