NASA Coating Evaluation Report & Results
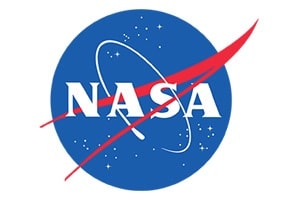
NASA did an experiment whose results shocked the coating industry. The study was conducted in 2013 – 2014 to find a coating that had excellent corrosion protection properties, the lowest impact on the environment, and no zinc, heavy metal, or isocyanate. The results showed the newest competitor on the block to be the clear winner. In 60 years of testing at the Cape the highest score ever on a scale of 1-10 had been a 9.2. In this test EonCoat received the first ever 10. For the Full Report click here.
The experiment takes 18 months of beachside exposure. The National Aeronautics and Space Administration or NASA took some of the coating industry’s best corrosion protection coatings and compared them side by side. The coatings, applied by NASA, were subjected to the vaunted NASA Beachside test, generally agreed to be the toughest real-world test to introduce corrosion. Some of the brands, were EonCoat, PPG, Sherwin Williams & Carboline, to just name a few.
How the Experiment Worked?
Some of the test panels had a steel cup welded onto the test panel. This measures how the coatings protect both welds and areas where saltwater pools. NASA then coated all the test panels with coatings from various manufacturers. NASA tested panels with the primer only and then tested separate panels with a full 3 coat system recommended by the manufacturer. In the case of EonCoat, the testing was just the single coat in both comparisons. In a separate test, the coated panels were given an X scribe to measure scribe creep.
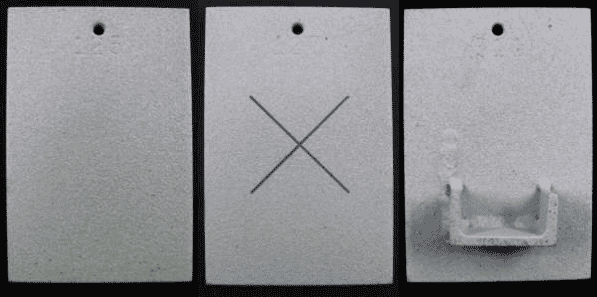
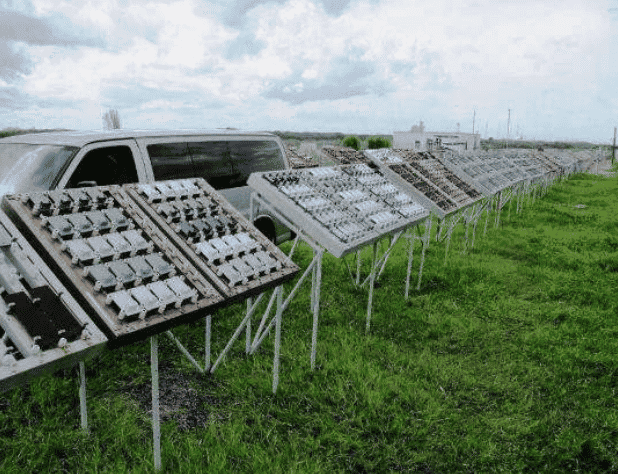
The panels were set on a stand 100 feet from the high tide mark, sitting at a 45-degree angle facing the Atlantic Ocean. Every 4 hours a sprinkler system sprayed seawater directly on the panels. This continued for 18 months.
It is worth noting that EonCoat was the only coating system without VOCs, HAPs, or Toxins. We were also 100% free of zinc, heavy metals, & isocyanates. No other coating met all those standards in these tests. EonCoat was also one of the two single-coat systems. Sherwin Williams, Carboline, & PPG all had multiple coat systems.
To the left are the results for the welded panels. These test panels were welded and left exposed to the elements for 18 months. During the 18 months, they were sprayed with sea water every 4 hours around the clock. NASA uses this test because welds are known to be the weak link of any structure when it comes to corrosion. The results prove this. See that only EonCoat survived this toughest of all tests.
The results speak for themselves. It is worth noting that 2 other coatings performed reasonably well. Both contain zinc, heavy metals, or isocyanates. Only EonCoat was inorganic, VOC-free, and a single coat. To read the full NASA report, please click here.
Ready to learn more about EonCoat? Sign up for our Free E-Book by clicking here (your email address is always safe with us). If you have questions about your unique corrosion prevention needs, click the Contact Us button below. We’d like to know how we can help you.
We appreciate the opportunity to earn your business and look forward to helping you permanently prevent corrosion on your carbon steel assets.
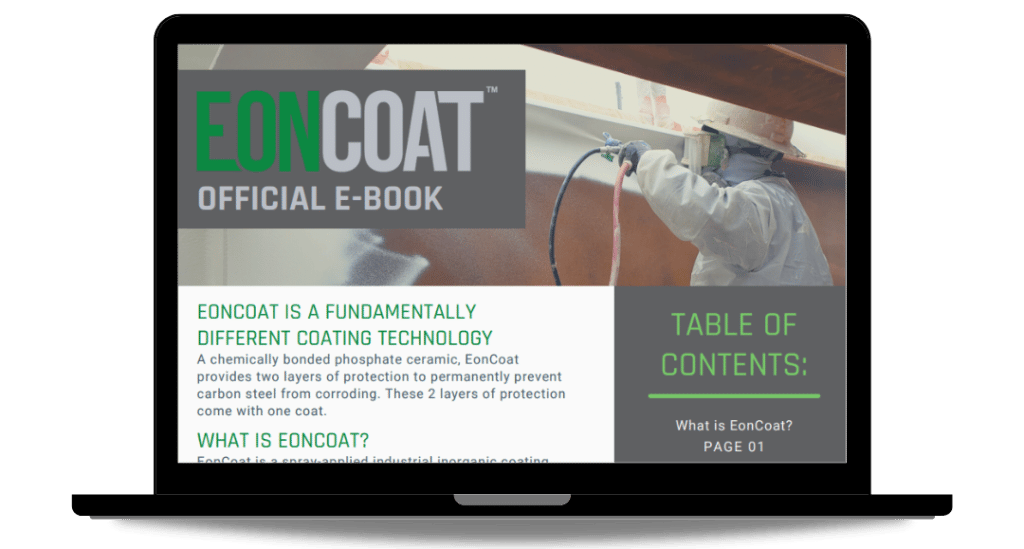
Do you want to become an expert on all things EonCoat? Download our Free E-Book and Crash Course to learn how EonCoat will save you time and money while permanently protecting your carbon steel assets from corrosion. You will receive one email daily over the course of five days, making it easy to learn at your own pace.
In this Free E-Book and Crash Course, you’ll learn:
- How EonCoat works.
- How safe is EonCoat?
- What are the cost benefits of Eoncoat?
- Who is currently using EonCoat?
- How is EonCoat Applied?
Are you ready to speak with a Corrosion Expert?