EonCoat has a process unlike other anti-corrosion agents to protect the pipelines and metal assets that are crucial to businesses around the world. Many leading brands utilize a single layer of protection against corrosion or require the use of a three-part ‘system’ featuring a primer, intermediate coat, and topcoat. Instead, EonCoat’s patented, dual-layer system is not only more effective than other methods, but it’s also safe, convenient, and easy to apply. And with EonCoat as a primer, only a thin layer of topcoat is needed and no intermediate coating is used.
Here’s more about EonCoat’s unique method of action.
What Are the Two Layers?
EonCoat relies upon two distinct layers that work together to provide unparalleled protection to carbon steel: the iron phosphate layer and the ceramic layer.
The Iron Phosphate Layer
The first layer of protection against corrosion is the iron phosphate layer, which is formed when EonCoat is sprayed upon the carbon steel. EonCoat chemically bonds with the steel to form an amorphous layer of magnesium iron phosphate. The resultant chemical bond is visible under an electron microscope; the alloy formed is only two microns thick and protects the steel from corroding by preventing any moisture or oxygen from ever coming into contact with the steel.
The Ceramic Layer
The iron phosphate layer is impressive in its own right, but the ceramic layer helps EonCoat’s protection rise to an unparalleled level. At a thickness of 20 mils, this layer of ceramic is nearly 100% inhibitor and leaches phosphate when necessary to re-alloy the steel. In this reservoir-like manner, the alloy remains intact, and the hard ceramic provides further value by acting as a guard against abrasion, making EonCoat self-healing without the need for reapplication.
Preparation
EonCoat’s highly effective method of protection against corrosion requires minimal surface preparation in the form of a commercial blast (NACE-3 / SSPC – SP 6), and the rapid return to service means assets are up and running again quickly. Notably, EonCoat actually excels when applied directly to flash rust as that assists in the formation of the iron phosphate alloy layer.
Filling the Gaps
Traditional barrier coatings leave gaps between the layer of protection and the steel substrate that can trap moisture that leads to corrosion when compromised. EonCoat is not a barrier coating. Its chemical charge means it is physically pulled into any valleys of the substrate. By alloying the steel, EonCoat ensures that no gap exists. Moisture and corrosion cannot penetrate the stable covalent bond between EonCoat and the steel. The patented formula allows for true long-lasting protection.
Self-Healing Properties
If one were to cut a scribe line through both the ceramic layer and the alloy layer, phosphate will leach from the ceramic layer and re-alloy the steel. No barrier coating in the world can make the same claim to this ‘self-healing’ regenerative quality as EonCoat can.
Additional Protection
Beyond EonCoat’s corrosion protection on carbon steel – backed by the confidence of a 30-year warranty – EonCoat provides abrasion resistance up to 10 times stronger than epoxies and 16 times stronger than most polymer paints. EonCoat also tests very well against extremely alkaline chemicals and all but the most undiluted acidic chemicals; this same chemical structure inherent in EonCoat’s formula also makes microbial growth next to zero, providing an extra level of sanitization. Finally, because EonCoat is fully inorganic (unlike many other coatings), the water-based coating contains no VOCs, no HAPS, no odors and it will not burn.
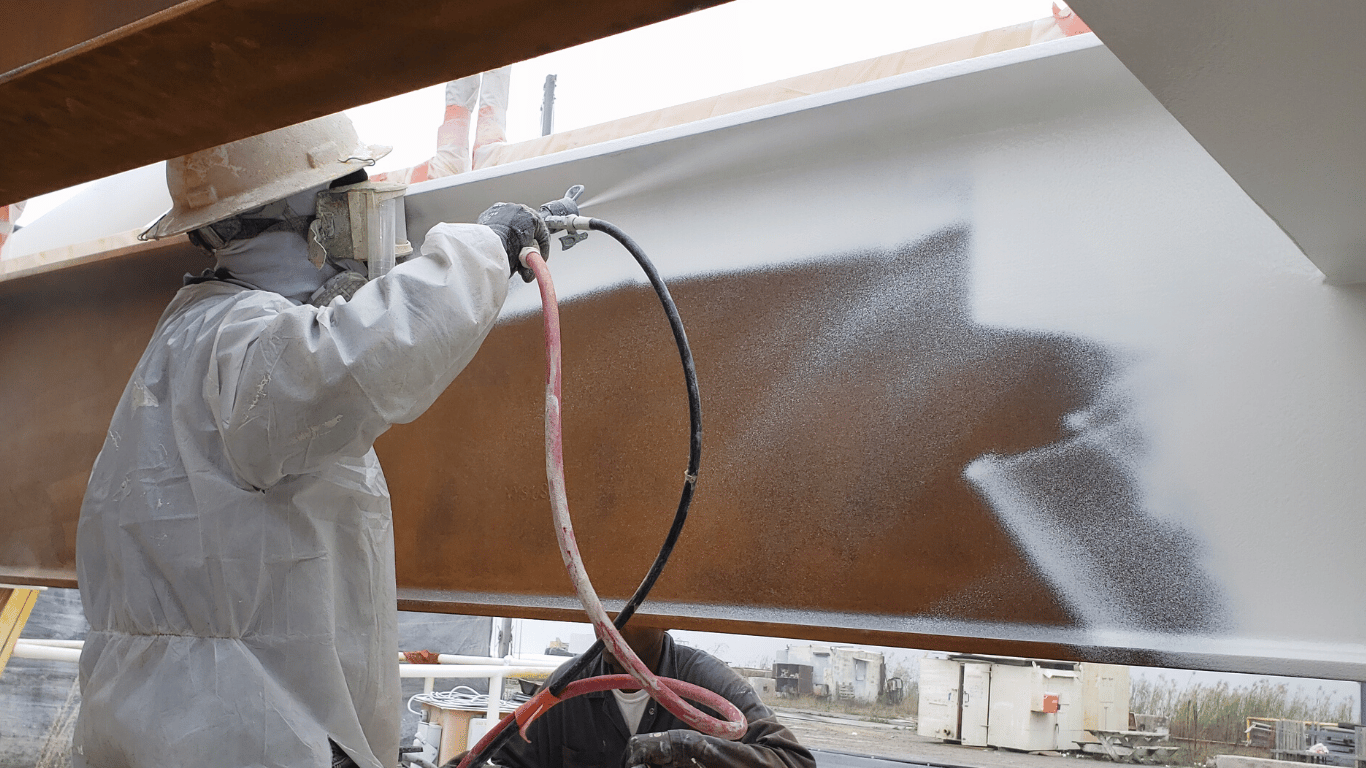
Ready to Learn More About EonCoat?