Anti-corrosion coatings have one job: to protect surfaces from corrosion. Yet when certain chemicals cause coatings to deteriorate, their ability to do that job is compromised. What exactly happens at the chemical level to cause these failures? How does this affect the lifespan of typical coatings? And what can we do to minimize the effect of chemicals on the protective coatings we use?
Understanding the Basics
Permeability is the quality of a material that allows liquids, such as water and oil, to pass through it without being chemically or physically affected. The more permeable a substance, the more susceptible it is to being changed through processes like corrosion. The more permeable a coating, meanwhile, the less effectively it can do its job.
Once a chemical attack breaks through a coating, the entire integrity of the coating is compromised. Corrosion will start at the affected area and lead to deterioration. This, in turn, increases the coating’s permeability to moisture and oxygen and accelerates the deterioration process. The end result is coating failure.
Alkaline Attacks
Common alkaline attacks result from exposure to calcium hydroxide, potassium, and sodium. The most widespread type of attack on anti-corrosion products is on the ester linkage of drying oil in a process called saponification.
Specifically, saponification occurs when the hydroxyls of the alkali break the ester linkage of the coating, which forms an organic acid and alcohol. This reduces the coating’s strength and leads to resin deterioration. The result is a brittle, powdery coating in dry conditions and a sticky, soft coating in wet conditions.
Acid Attacks
On the other end of the pH scale, we have acids (the most common are hydrochloric, nitric, and sulfuric). These chemicals form by reacting with moisture, either through the air (i.e. humidity), precipitation (i.e. rain), or condensation (i.e. dew). Acids attack by breaking down the chemical bonds they come in contact with.
Condensation leads to the strongest acid attacks, which is bad news for outdoor equipment with anti-corrosive coatings. The water components of condensation droplets dry throughout the day, leaving nothing behind except acid that is highly concentrated. Acid rain is less threatening because continuous rainfall dilutes the acids. In some cases, the acids may be washed away before any damage is done.
Chemical Attacks and EonCoat
While the potential damage of alkaline and acidic attacks on traditional coatings is great, there is another option that offers more protection. EonCoat is a spray coating solution consisting of carefully selected compounds, which work together to create a layer that offers superior protection against most chemical attacks.
Here’s how it works: the acid in EonCoat transforms the top steel layer into an iron phosphate alloy layer to prevent corrosion. Next, a ceramic coating forms an outside layer to provide the alloy with a continuous source of phosphate to re-alloy the steel if necessary.
The result is an anti-corrosion solution that protects the steel from a wide range of chemical attacks. In testing, exposure to alkalines yielded very little chemical reactivity (no reactions were seen involving alkalines with a pH of 6 to 12). Similar results were seen with acidic exposure. Only those with a pH less than 2, such as sulfuric acid, yielded reactions.
EonCoat: Your Anti-Corrosive Solution
While alkaline and acid exposure weakens traditional anti-corrosive coatings, they aren’t the only threats. Neutral substances, such as water and salt, can also damage a coating’s effectiveness. Continuous reapplication due to these types of reactions is costly due to purchasing of supplies and revenue lost due to equipment downtime.
That’s what separates EonCoat from the rest. Our product self-heals, as the inner alloy layer is reinforced by the outer ceramic layer, which continuously delivers new phosphate to prevent corrosion. The ceramic outer layer also offers a strong defense against abrasions, breaks, and cracks.
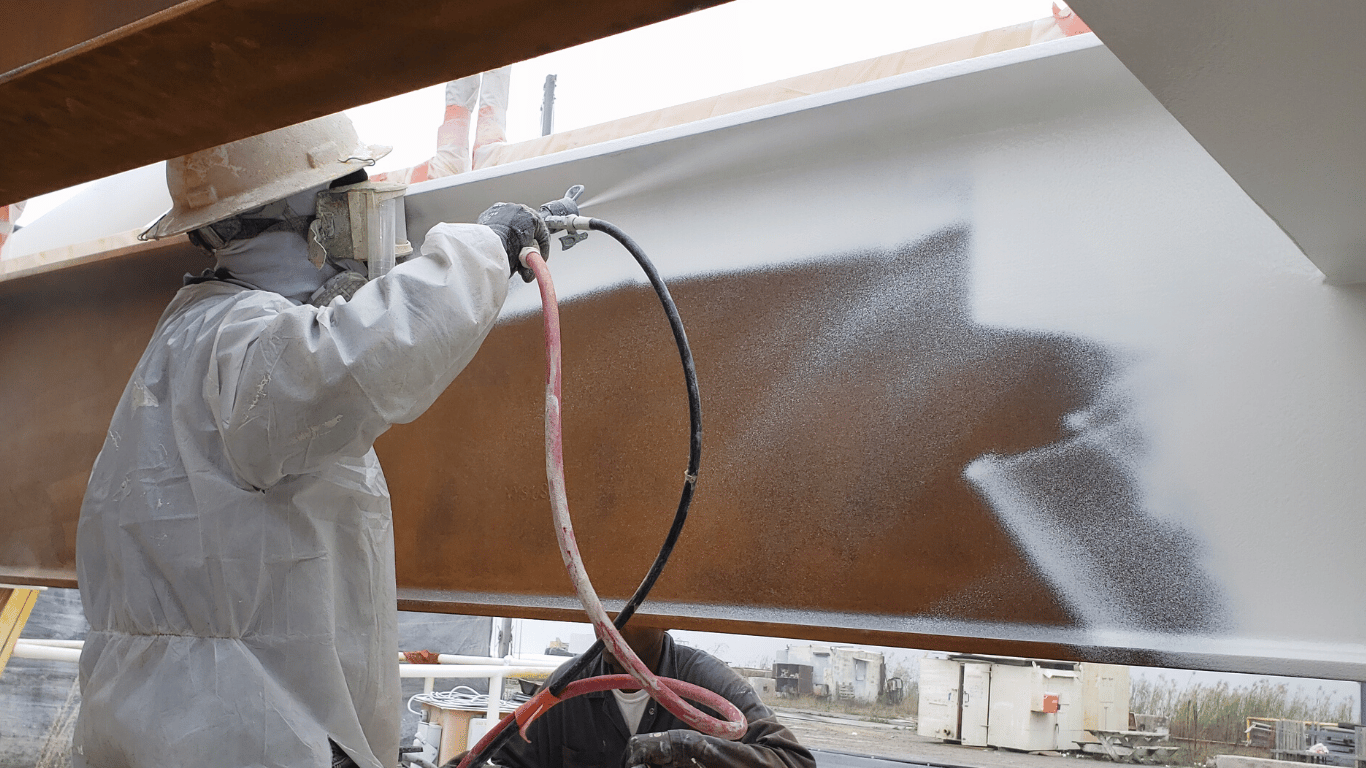
Ready to Learn More About EonCoat?