While the gradual corrosion of steel is a costly problem for the oil & gas industry, flash rust — the sudden onset of corrosion on a potentially massive scale — may be even trickier to resolve. True to its name, flash rust can occur without warning and take over a metal surface in a few hours, or even as little as a few minutes.
Addressing rust and corrosion has been a core focus of the oil & gas industry since an investigation was first ordered by Congress over a century ago. Flash rust has been a particular pain point. It’s difficult to predict and contain due to a variety of factors ranging from surface cleaning method to environment.
In this post, we’ll cover flash rust in detail and explain how EonCoat’s anti-corrosion solution can help companies who face flash rust.
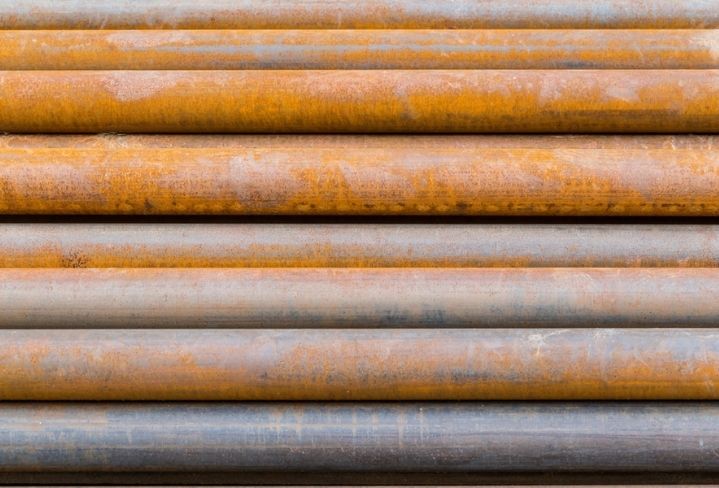
Why is Flash Rust Such a Big Problem?
Flash rust often occurs after using intense wet cleaning methods, such as blast cleaning or water jetting. The window of time between the cleaning and the drying of the surface is when rusting occurs.
Why choose certain cleaning methods if they make surfaces vulnerable to flash rust? Apart from considering the price and cleaning time, some products require a surface profile that can’t be maintained through cleaning methods like chemical stripping or pickling. In some cases, limited access to alternate cleaning methods may leave a company to use blasting methods by default.
Cleaning methods aren’t the only cause of flash rust; it can appear in several forms depending on the surface type and environmental conditions. Rust back, for example, occurs when a steel surface is exposed to contaminants like humidity and moisture. For equipment present in wet areas, this means the risk of flash rust is always present. Even in seemingly dry conditions, any presence of humidity can lead to the development of flash rust.
Flash rust presents an obstacle to applying most forms of corrosion prevention. In order to apply traditional anti-corrosive coatings to carbon steel assets, companies usually have to first remove any flash rust from equipment surfaces. The costs of cleaning materials and extra labor time needed to clean the surface can add up quickly — especially for those companies that operate in moist and humid regions, prone to flash rust.
Let’s not forget the most frustrating fact: traditional coatings don’t guarantee the prevention of flash rust. It’s practically inevitable that flash rust will reappear, forcing companies to repeat this process over again.
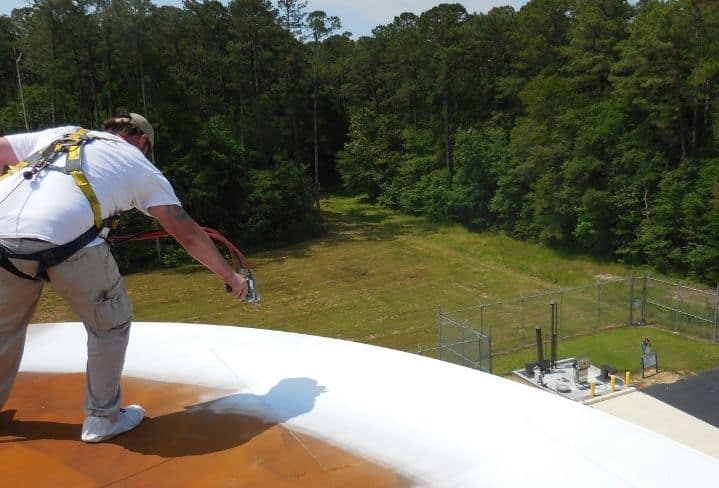
EonCoat® Handles Flash Rust in a Flash
Naturally, investing in long-lasting prevention is the easiest way to combat flash rust. But what about the flash rust already present? Are inefficient and expensive cleaning methods the only way to handle this issue? Thanks to EonCoat’s patented coating, the flash rush is no longer an issue.
EonCoat® is an inorganic steel coating made up of two components, an acid, and a base, which combine to offer two strong layers of defense against corrosion. One of the greatest benefits of EonCoat® is that it can be applied directly on top of flash rust — eliminating much of the labor, cost, and equipment downtime needed to prepare a steel surface before using traditional coatings. With EonCoat® there’s no need to invest in costly cleaning methods to remove existing flash rust from the surface of your steel assets.
Unlike most coatings, which often require a white metal blast or near-white blast, EonCoat® only requires a commercial blast before application. Because EonCoat® can be applied over flash rust, the surface preparation can be done all at once. EonCoat® can then be applied hours, days, or even weeks later. The relatively low cost and time spent on surface preparation make it a revolutionary product for not only the oil & gas industry but many other industries that rely on carbon steel assets.
The simple application process isn’t even the best feature of this anti-corrosion coating. Once applied, EonCoat® provides lifetime protection on the applied surface thanks to its two layers of defense. The first layer is a 2-micron thick iron phosphate alloy layer. The second is a 20 mil thick white ceramic layer, which forms on top of the alloy layer and, if needed, continuously re-phosphates the steel to keep the alloy layer intact. The top ceramic layer, which serves as a phosphate reservoir, makes EonCoat® self-healing so there’s no need to reapply or repair the coating after application.
When it comes to fighting flash rust, the oil & gas industry really can’t ask for anything better. If you’re ready to make worrying about flash rust a thing of the past at your company, contact the team at EonCoat to learn how we can help protect your carbon steel assets.
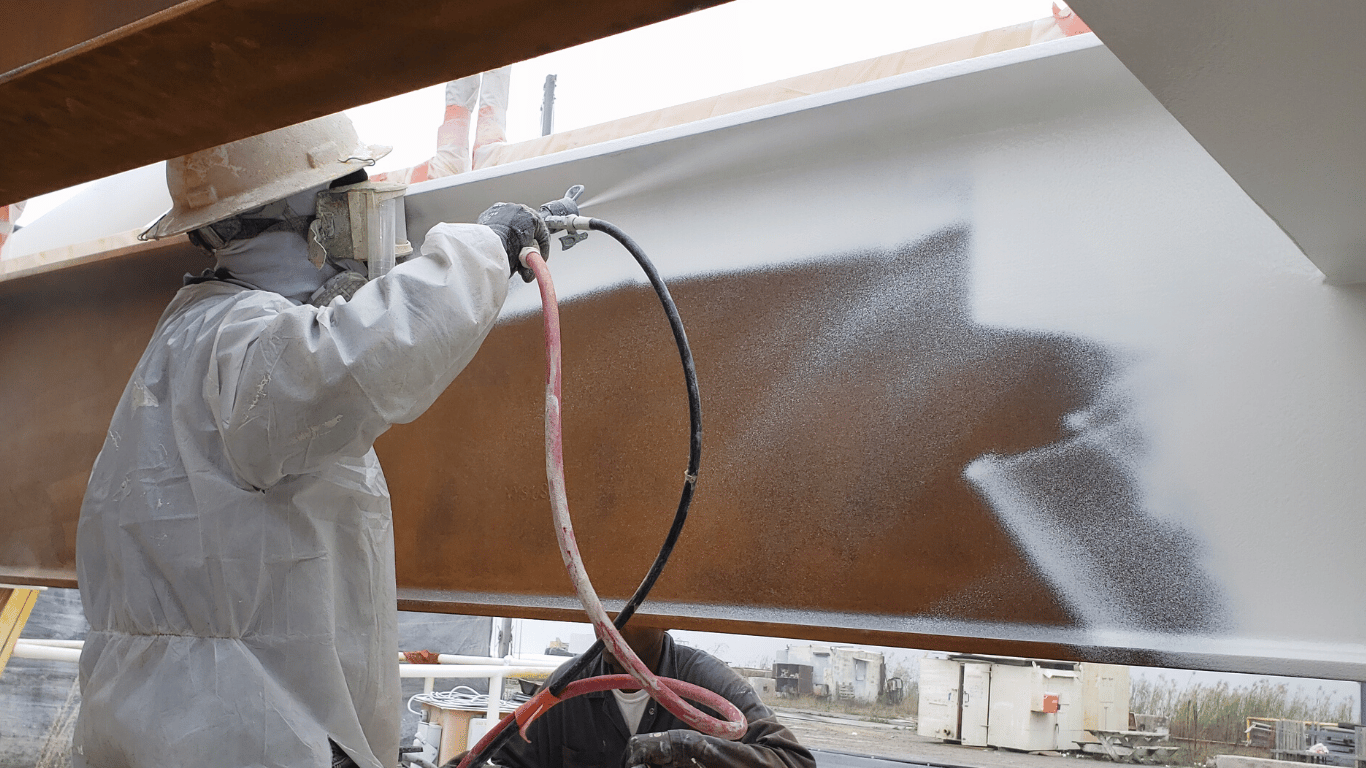
Ready to Learn More About EonCoat?