Unplanned refinery downtime is a significant drain for companies in the oil and gas industry. Unexpected downtime not only costs your business time and money, but it can also have a ripple effect in delaying future schedules, production, equipment maintenance, and more.
Corrosion is a large cause of unplanned refinery downtime and a dangerous enemy to oil and gas companies, as it may gradually attack your carbon steel assets undetected until it’s too late. Once it’s discovered, corrosion may force you to unexpectedly stop production at your refinery, taking a toll on your team’s productivity and your bottom line.
In this post, we’ll discuss how the right corrosion prevention methods can help you reduce unexpected downtime at your company.
The Problems with Unexpected Downtime
Let’s start with a typical industry example of corrosion: piping corrosion.
With some minor exceptions (e.g. flash rush in specific environments), piping corrosion can take months or years to grow into a piping failure problem. Some failures are minor, such as small cracks or pinholes that leak. Yet significant corrosion can lead to pipe bursting or cracking.
Regardless of the extent of damage, downtime is inevitable. For minor or concentrated corrosion, downtime will include the time it takes to apply temporary clamps or replace individual pipes. For extreme or total corrosion damage, pipelines or even entire systems may need to be replaced.
Your company is faced with a variety of costs when addressing a corrosion issue. Aside from the direct costs of replacing steel assets, piping damage means all production is put off, delaying schedules down the supply chain.
Total costs can include:
- The cost of labor to install the new piping
- The cost of the new materials themselves
- The cost to dispose of the damaged piping
- The cost of production (and profit) loss due to downtime
- Added labor costs due to idle time
- Added transportation costs due to rearranging shipment schedules
Taken together, the costs associated with downtime — and corrosion as a whole — are staggering. In fact, corrosion costs in the United States alone rose over $1 trillion by 2013. Amounting to 6.2% of GDP, corrosion was one of the costliest single expenses in the nation’s economy.
Traditional Corrosion Prevention Methods Only Add to Downtime
One of the best ways to reduce unexpected downtime is to prevent corrosion in the first place, protecting your steel assets from costly damage.
Most oil and gas companies run into a common problem: traditional methods for preventing corrosion aren’t effective in the long term, and therefore they don’t adequately reduce refinery downtime. Many paints and coatings fall victim to stresses caused by the drying process for the liquid coating, temperature changes in the environment, and abrasion. When the coatings are weakened by these stresses, the result is yet more refinery downtime, as your company must halt production to repair or replace the traditional anti-corrosive coating.
In many cases, traditional coatings require extensive downtime of assets from the get-go, in order to prep the steel surface and apply the coating.
In the case of corrosion under insulation (CUI), the problems are even more severe. CUI functions as the silent killer of steel in industrial environments. The cost and time associated with the continuous pipeline inspection process for the purpose of identifying CUI before it is too late, along with the cost of replacing the corroded pipe, accounts for about 10 cents of every fixed equipment maintenance dollar in an industrial facility.
The Solution: EonCoat® and the End of Downtime
Unlike traditional anti-corrosion methods, EonCoat® helps oil and gas companies greatly reduce the risk of unplanned refinery downtime — because its formula is designed to last, and it doesn’t need to be reapplied or replaced.
EonCoat® chemically bonds to carbon steel, rather than simply resting on top of it. It provides two layers of protection. The first is an iron phosphate alloy layer. As a second line of defense, a ceramic layer forms over the alloy layer and provides a reservoir of phosphate to continuously maintain the alloy layer. In other words, EonCoat® is self-healing.
The ceramic layer itself also acts as a protective external coating and includes the following benefits:
- Resistance to abrasion
- Resistance to both base and acidic chemicals
- Resistance to fire and temperatures up to 500 degrees Celsius
All of these advantages reduce downtime. The self-healing nature of EonCoat® means the elimination of labor, material costs, and downtime by avoiding coating re-application. By chemically bonding with the steel, EonCoat® prevents corrosion from impacting your assets, eliminating the risk of unplanned downtime due to corrosion damage.
While downtime costs cause a ripple effect throughout your supply chain, the reverse is also true. The right corrosion prevention method saves companies — and the oil and gas industry as a whole — significant time and costs throughout the supply chain.
Traditional coatings have their drawbacks, and the industry has been paying enormous costs for them. New solutions like EonCoat® are changing this. We offer a permanent solution to protect your company’s carbon steel assets.
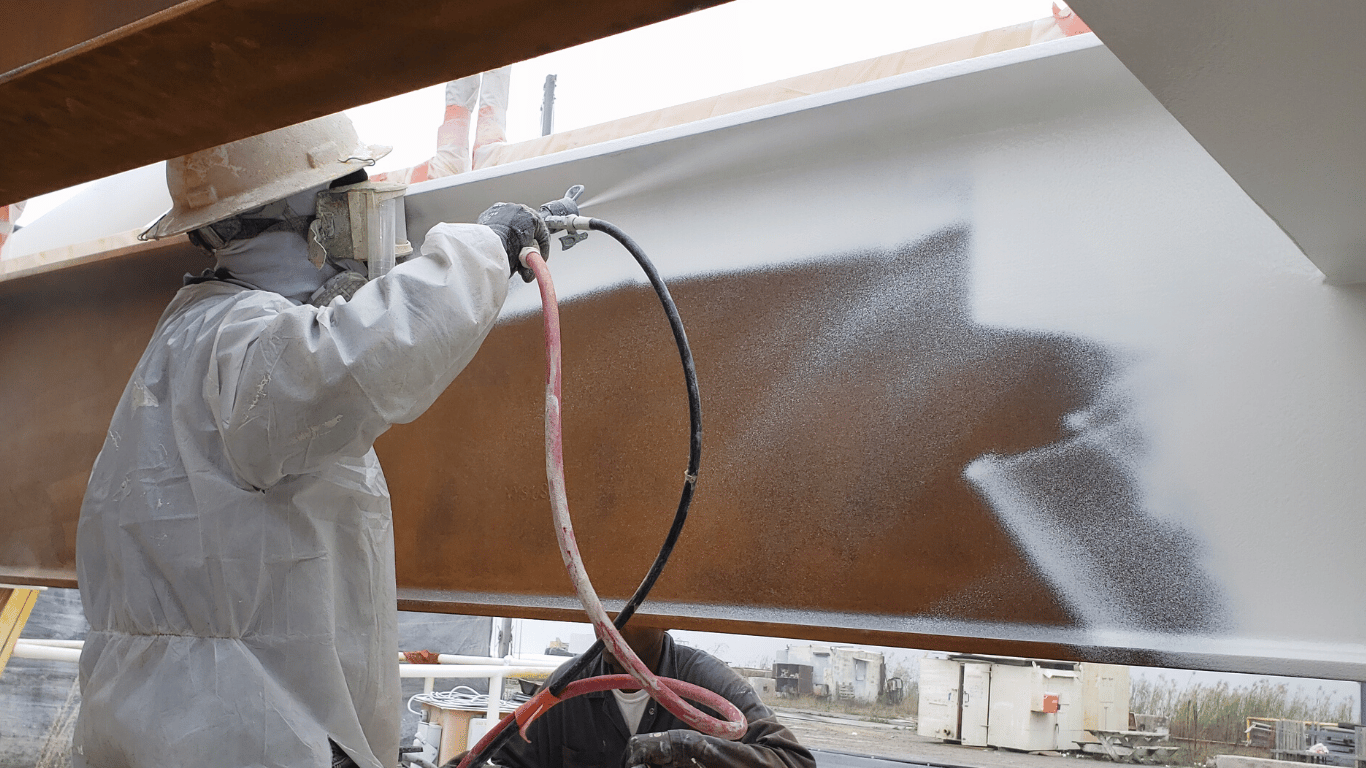
Ready to Learn More About EonCoat?