There are many different types of corrosion, ranging from those that are easily identifiable with the naked eye, to those that take some additional examination to accurately identify.
This naturally occurring condition can cause costly and dangerous damage to systems from personal vehicles to pipelines and architectural infrastructures such as bridges and buildings. Fortunately, there are methods available to help control corrosion and reduce the extent of its damage.
Read on to discover 6 types of corrosion that are more difficult to identify and their causes.
1. Erosion Corrosion
Erosion corrosion occurs when a corrosive fluid runs past a metal surface. Often found on the internal surfaces of pipes and tubing, this type of corrosion leads to increasing erosion that eventually causes a leak. This type of corrosion is also common when the surface of the metal is not smooth, such as from pitting in the metal or compromised workmanship. Erosion corrosion can also be found in offshore well systems or any system where metal comes into contact with liquid-bearing rough particulates, such as sand.
Smoother metal surfaces and lower fluid velocity, along with easily replaceable parts that can bear the brunt of the flow, can help reduce damage. Applying a protective coating is another method utilized to mitigate this type of corrosion.
2. Intergranular Corrosion
Intergranular corrosion occurs at the grain boundaries of metal, often due to impurities that tend to accumulate in those areas. This is primarily caused when chromium carbides consume the chromium in an alloy, making the area anodic, and subject to corrosion by the unaffected grains nearby.
Identification of this type of intergranular corrosion often requires microscopic examination by a professional.
3. Fretting Corrosion
Fretting corrosion is the result of repeated movements of metal under load. It is usually found in machinery and bolted structures or bearings, as well as — and most commonly — contact surfaces subject to continued vibration via transportation. Protective coating on the metal is rubbed off to expose active metal that is then corroded over time by the atmosphere.
4. Cavitation Corrosion
Cavitation happens when the operating pressure of fluid drops below its vapor pressure. This causes gas pockets and bubbles to form and collapse and often occurs within pumps, propellers, regulator and valve discharges, pipe elbows and expansions, hydraulic blades, and such. This type of repeated implosion of gas bubbles eats away at the surface of the metal over time.
5. De-Alloying (Selective Leaching)
De-alloying, or selective leaching, is caused by the corrosion of a select metal within an alloy. This type of corrosion most commonly occurs in unstabilized brass. Zinc is selectively leached from the metal, resulting in a porous and weakened copper, or medium- and high-carbon steel, wherein decarburization occurs.
6. Exfoliation Corrosion
Exfoliation corrosion is intergranular corrosion that is most often associated with strong aluminum alloys. Alloys that are elongated and flattened from heavy work and extrusion have a high risk of this type of corrosion. The production of this corrosion builds around the grain boundaries of the metal and lifts the grains, resulting in a leafing or layering effect. This is most often found near holes, machined edges, and other breaks in the metal, and once initiated can spread to the entirety of the affected metal piece.
Getting Corrosion Checked Out
Repairing corrosion damage can cost your business money that could have been spent elsewhere if the corrosion had been better prevented.
Corrosion prevention comes in the form of correct identification, the use of appropriate alloys, using post-weld heat treatments, and applying a protective coating whenever possible to prevent exposure to corrosion-causing environmental elements. It could make all the difference to your systems and expenses.
If you’re looking to mitigate the effects of corrosion, speak to a member of our team today.
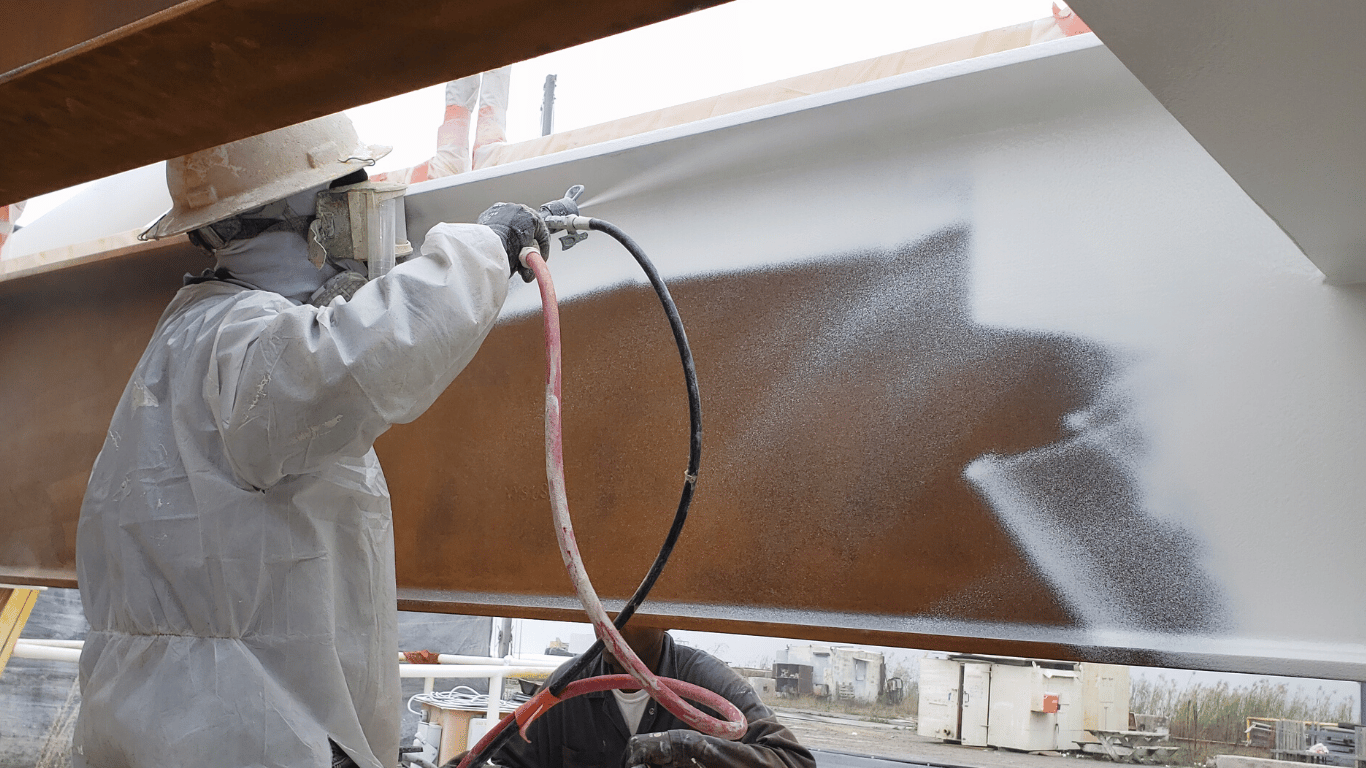
Ready to Learn More About EonCoat?