Oil and gas companies can no longer rely on consistently rising oil and gas prices to make their projects sustainable. That doesn’t mean profitability is impossible, but rather that it will come — at least in part — from increasing efficiency rather than simply increasing productivity.
While prices are starting to rise after years of lagging behind, they have yet to approach historic highs. Low prices led to declining infrastructure investments in recent years, leaving many companies ill-equipped to supply growing demands for energy. Even while demand and prices may now be rising, public enthusiasm is rapidly gathering around alternative energies.
All of these factors combined mean that oil and gas companies must look for ways to improve the efficiency of their assets and operations, in order to reduce costs and remain competitive. In terms of efficiency improvements that have a real impact on the bottom line, no project is more important than asset maintenance.
Carbon steel assets are complicated to maintain, expensive to replace, and disruptive to do without. For instance, corrosion alone costs the industry $1.372 billion annually. And when a large onshore facility unexpectedly goes offline because of maintenance issues, it costs an estimated $7 million a day in lost revenue (daily lost revenue is much more for offshore facilities). Asset maintenance is not just an obligation, but also a significant economic opportunity. When done well, companies can achieve the operational efficiency needed to weather volatile and uncertain oil markets by extending the life of their steel assets.
To maximize efficiency improvements, take a two-pronged approach to asset maintenance at your organization.
Rely on High-Tech Asset Monitoring
Most companies already approach maintenance systematically. But considering the number of assets in play and the scale of maintaining them all, taking an analog approach to maintenance inevitably leads to overlooked issues and ineffective prevention.
New technologies ranging from drones to internet-connected sensors and big data analytics give companies more efficient asset monitoring capabilities. With high-tech monitoring tools, you can spot and address issues earlier, helping to prevent equipment failure and expensive repair or replacement costs.
Technology also enables companies to allocate maintenance staff and resources more effectively, so they’re addressing the most urgent issues first. According to one estimate, automation is expected to save the oil and gas industry $73 billion over the next five years using only currently existing technologies. Savings on asset maintenance are only part of that total, but those savings are significant.
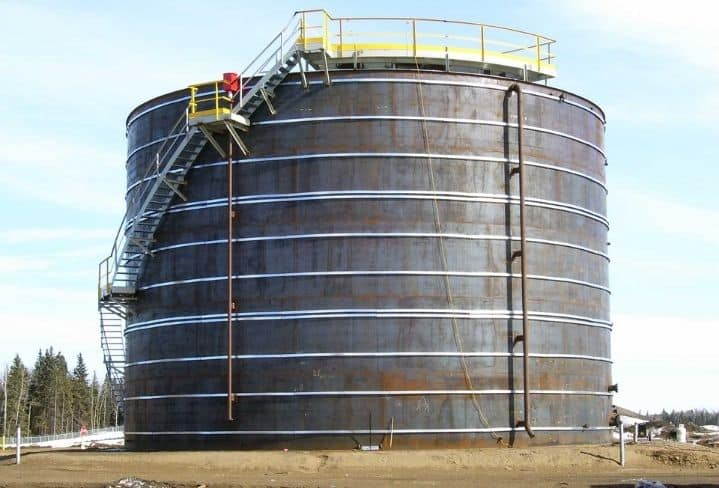
Utilize Advanced Corrosion Prevention
Identifying signs of corrosion early helps reduce the cost and time needed to address it, but this can only do so much to extend the life of your assets. Preventing corrosion from occurring in the first place is far more impactful.
A problem like corrosion under insulation (CUI), for example, is hard to spot (even with modern technology) and even harder to stop. Even with an army of technicians in place, controlling the cost and consequence of CUI and other forms of corrosion is unreliable.
Traditionally, oil and gas companies have invested in protective paints and coatings that temporarily fend off corrosion — but traditional coatings need to be reapplied and repaired at regular intervals often requiring equipment downtime, and always requiring the cost of maintenance, and therefore canceling out the chance of any cost or time savings brought by these coatings.
Thanks to advancements in the coatings industry, corrosion prevention is now possible with EonCoat’s proven-effective coating applied to the exterior of your carbon steel assets. Once in place, EonCoat® prolongs the life of your existing assets while preserving your investment in new assets.
EonCoat® saves companies time and cost from the start, with little time spent on application — it requires minimal surface preparation in the form of a commercial blast (NACE-3 / SSPC – SP 6) and can be applied directly over existing flash rust to minimize application time. The coating can withstand direct mechanical damage and extended weathering without allowing the spread of rust. This kind of all-encompassing protection is only possible because EonCoat’s proprietary formula chemically bonds directly to the substrate while also providing a highly durable outer layer.
Asset maintenance becomes easier and more cost-effective when corrosion is eliminated instead of mitigated. EonCoat is the established leader in corrosion prevention and a crucial component of your asset maintenance strategy. Don’t take our word for it; independent testing proved the performance of our product under exactly the kind of high-stress scenarios that oil and gas equipment encounters.
Find out how EonCoat stood up to multiple tests and proved its effectiveness by downloading our free e-book.
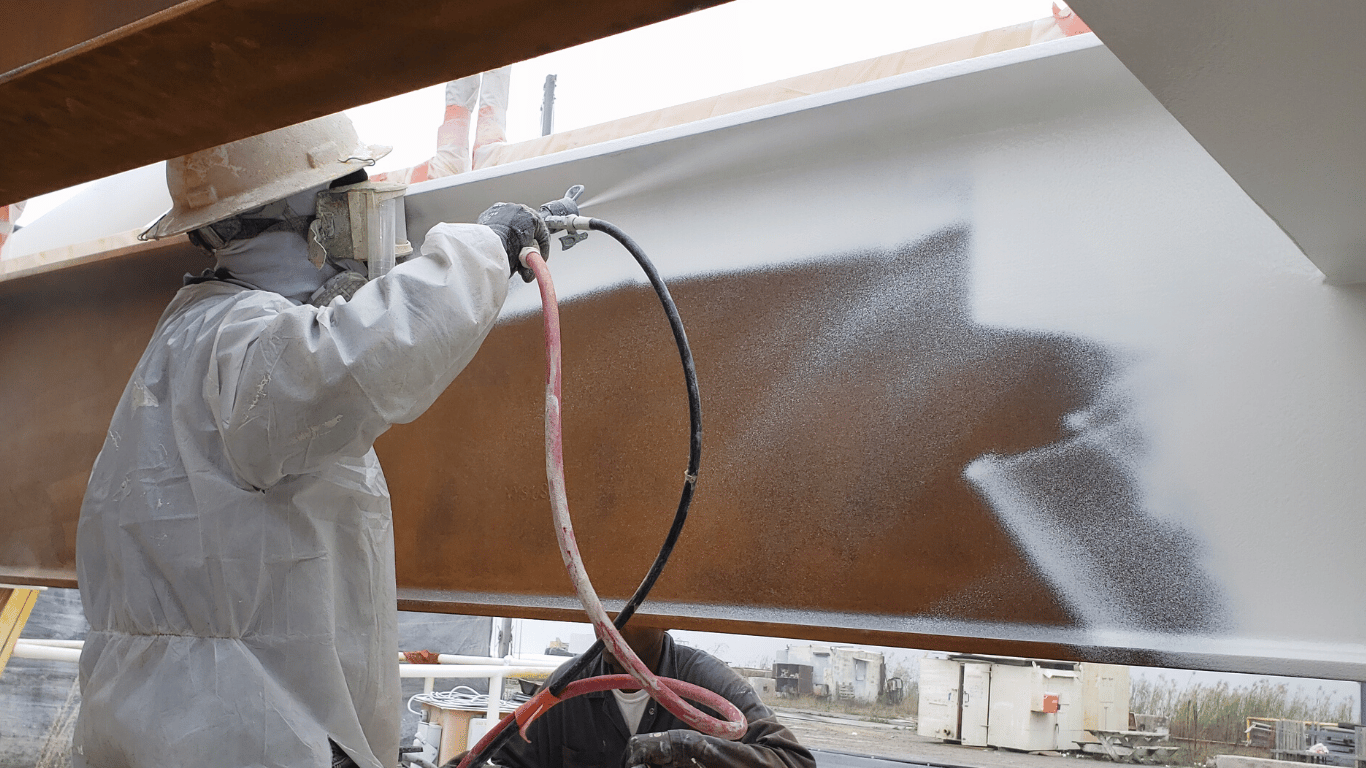
Ready to Learn More About EonCoat?