From the rise of the electric car to extensive data tracking around the globe, green initiatives and rapid change at first seemed threatening to the oil and gas industry — but oil and gas businesses are finding that advanced technology can be their key to cutting costs and staying competitive.
Drilling and completion costs have decreased by 40% since the peak of the oil boom, and that’s not only because oil field services have gone down in price. Oil and gas companies are changing the way they work to embrace technological advancements that subsequently lower their overall costs. Smart machinery, cloud-based solutions, and revolutionary corrosion prevention methods can help boost your production and your bottom line.
Read on to discover the top advancements that can save your oil and gas business significant costs, raising you from behind the times to the forefront of your competition.
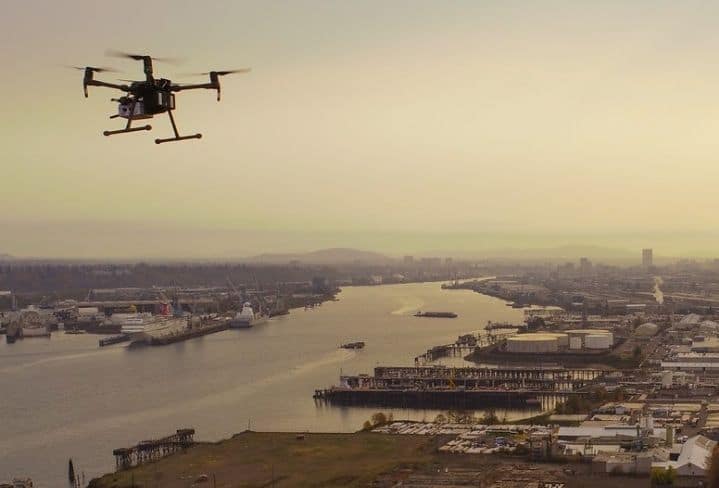
1. Drones
Controlled from afar, drones can conduct inspections of hard-to-reach equipment and expansive areas more easily and effectively than human workers. Not only does this reduce safety risks for workers, but it also eliminates the need for staff to physically travel to every inspection point — cutting down on travel expenses while improving efficiency.
Remote-controlled robots can also be used to perform dangerous or time-consuming tasks quickly. For example, robots can connect drill pipes on oil rigs and carry out inspections within a matter of days that would take rope-access technicians weeks to complete. This saves time and reduces the chance that your company will have to rectify any costly mistakes.
2. Artificial Intelligence
The oil and gas industry is poised to benefit from artificial intelligence (AI) advancements that can be incorporated into traditional equipment. One such example is the intelligent rig, which can leverage weather forecasting, computational capabilities, and other features to increase operational capacity. Using intelligent rigs ensures higher production and reliability, as your business receives advanced warnings of any issues that can lead to equipment downtime or lost wells. The higher production of intelligent rigs can allow companies to use fewer oil rigs in the first place, saving on the costs of equipment and maintenance.
Another example is the use of smart bits to make drilling more efficient. With their multidimensional cutter technology, these smart bits can recognize different rock layers. This allows them to effectively adapt to any job, be it onshore or offshore. As a result, smart bits have a more consistent rate of penetration (ROP) and a longer lifespan, which saves your business replacement costs.
3. Cloud-Based Computing
Cloud-based computing has changed the way companies manage data, by giving users access to the data they need no matter where they’re located. This can be especially helpful in the oil and gas industry, where operations don’t all take place under one roof and can be expensive to track.
With cloud technology, your entire business can store a huge volume of data for analysis, which can be accessed from virtually anywhere. For example, your workers can monitor well production from their mobile devices and then cater to issues on location, with all the information they need to make informed decisions. This accuracy and transparency allow work to be completed in the shortest amount of time and empowers team members to optimize production.
Having more data than ever at the touch of a button — without having to physically visit every site — allows your workforce to streamline inspections, maintenance, and other processes, reducing overall costs to the business.
4. Modern Corrosion Prevention
Recent advancements in oil and gas aren’t limited to just technology; there have also been impressive advancements made in the mission to prevent corrosion, a natural threat to steel that costs oil and gas companies billions each year. Keeping your assets free from corrosion ensures that your equipment will last longer and give you a greater return on investment.
Oil and gas companies have long struggled to combat corrosion. While traditional anti-corrosion solutions — such as paint coatings and cathodes — help to reduce or delay corrosion that affects your assets, they can never truly prevent it. What’s more, these methods need to be repaired and replaced over time, which requires ongoing investment and causes costly downtime.
In addition to embracing advanced technology, oil and gas companies are also saving costs by embracing new anti-corrosion methods, such as EonCoat’s revolutionary spray-applied coating. EonCoat® prevents corrosion from ever developing — and it only needs to be applied once. EonCoat® chemically bonds to the surface of your carbon steel assets, forming a 2-micron thick iron phosphate alloy layer that serves as the first line of defense. On top of this alloy, the layer is a 20 mil thick white ceramic layer. This functions as a phosphate reservoir, to continuously re-phosphate the steel and keep the alloy layer intact. The result is an effective coating that can withstand abrasion, chemicals, and high impact.
EonCoat® has already been used successfully in harsh oil and gas industry environments, from oil storage tanks in the United States and China to offshore platforms in the Gulf of Mexico and the North Sea. With just one quick spray application of EonCoat®, you can reduce equipment downtime, regular upkeep, and costly repairs to your assets. It’s a sure-fire way to reduce your operating costs.
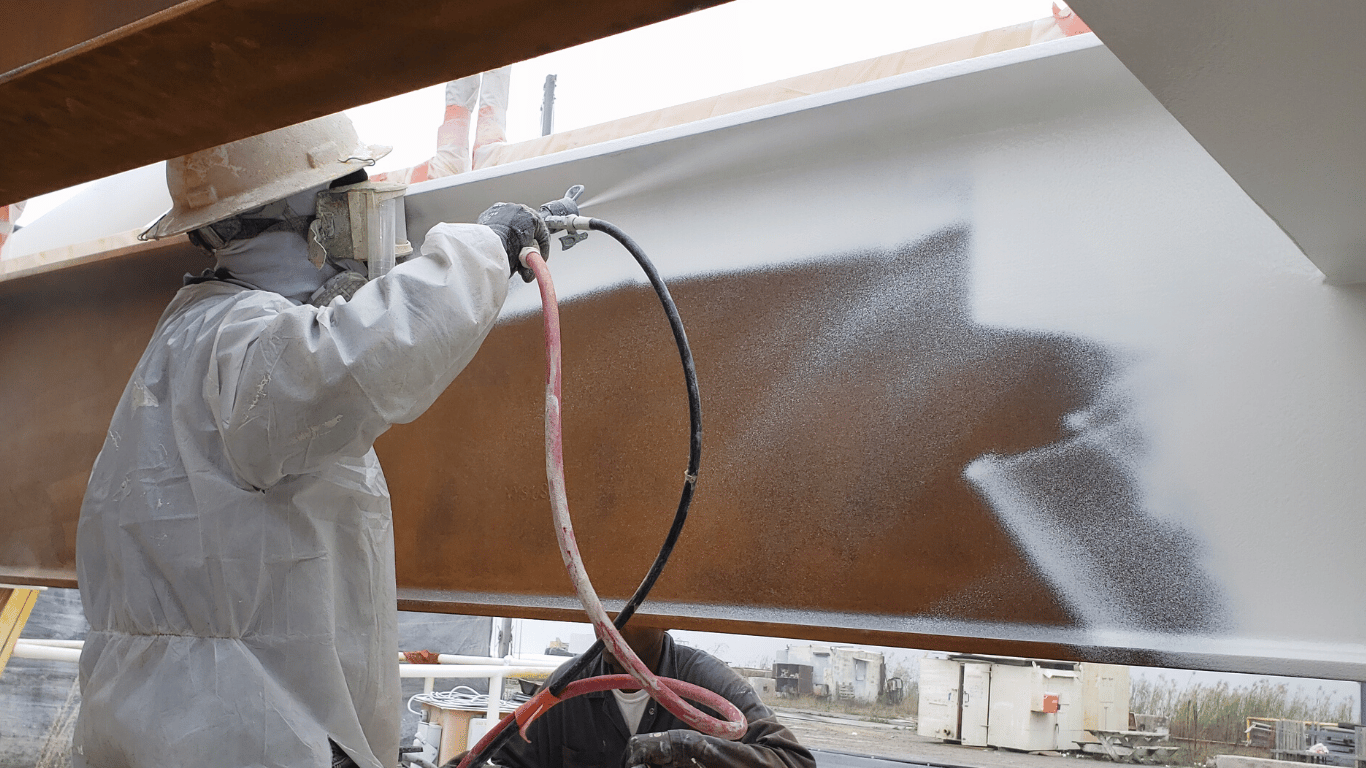
Ready to Learn More About EonCoat?