Cathodic Protection is a major weapon against corrosion but has some costly disadvantages when trying to protect larger steel assets
For corrosion to occur, four elements must be present: a host site from which current flows, a destination site where no current flows, a medium capable of conducting current (such as water, concrete, or soil), and a metal path between the host and destination site.
Electrochemical corrosion of metals is the process by which ions on the surface of metal are transferred to another substance (a depolarizer, or less active substance or metal). Such depolarizers are oxygen, acids, or cations of more passive metals.
What Is Cathodic Protection Used For?
Cathodic protection is often used to mitigate corrosion damage to active metal surfaces. It is used all over the globe to protect pipelines, water treatment plants, above and underwater storage tanks, ship and boat hulls, offshore production platforms, reinforcement bars in concrete structures and piers, and more.
A Cathodic system is often used to protect steel from corrosion. Corrosion is caused when two dissimilar metals are submerged in an electrolytic substance such as water, soil, or concrete. This type of metal conducting path between the two dissimilar metals allows a pathway through which free electrons move from the more active metal (anode) to the less active metal (cathode). If free electrons from the anode do not reach active sites on the cathode before the arrival of oxygen, ions at the active sites can then recombine to produce ferrous hydroxide, i.e. rust.
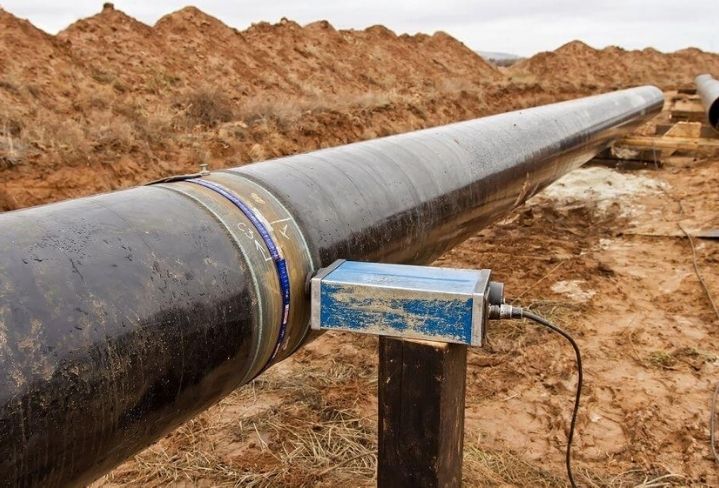
How Does Cathodic Protection Work?
In essence, cathodic protection connects the base metal at risk (steel) to a sacrificial metal that corrodes in lieu of the base metal. The technique of providing cathodic protection to steel preserves the metal by providing a highly active metal that can act as an anode and provide free electrons. By introducing these free electrons, the active metal sacrifices its ions and keeps the less active steel from corroding.
Types of Cathodic Protection.
There are two basic types of cathodic protection:
Galvanic
Galvanic protection consists of applying a protective zinc coating to the steel to prevent rusting. The zinc corrodes in place of the encapsulated steel. These systems have limited life spans. The sacrificial anode protecting the underlying metal will continue to degrade over time. Until the sacrificial anode is no longer capable of supplying protection.
Impressed Current Cathodic Protection
Impressed current cathodic protection systems consist of anodes that are connected to a power source that provides a perpetual source of electrical flow. The sacrificial anode method of protection uses a metal more active than the base metal to “sacrifice” ions. These “sacrificial anodes” (usual alloys such as magnesium, aluminum, or zinc) have a stronger electrochemical potential. This method can often provide much longer protection than a sacrificial anode. The anode is supplied by an unlimited power source.
Drawbacks of Cathodic Protection.
Cathodic protection has been used for years to protect structures that suffer long-term exposure to corrosive environments. But the installation of cathodic protection itself can be costly. The specific details of how structures are constructed can also add to the complexity. So, the cost of cathodic protection. In addition to this cost, the system also requires routine maintenance, including a periodic visual inspection. In the case of impressed current cathodic protection, there is also the ongoing cost of electricity. Sacrificial anodes, in particular, have a limited amount of currently available, are subject to rapid corrosion. Meaning they have a limited lifespan.
This protection doesn’t work well on large metal surfaces that do not have a barrier coating. A key example is the bottom of large, welded tanks. The reason is that it is nearly impossible for even a well-designed cathodic system to maintain the proper voltage across a long metal span that is not insulated. It is because of the natural voltage drop when current is flowing, and current will certainly flow when a surface is exposed to the ground and not insulated. While cathodic protection can work great on pipelines that have an epoxy barrier coat it has serious limitations for uncoated surfaces. Experts think of cathodic protection as secondary to the barrier coating.
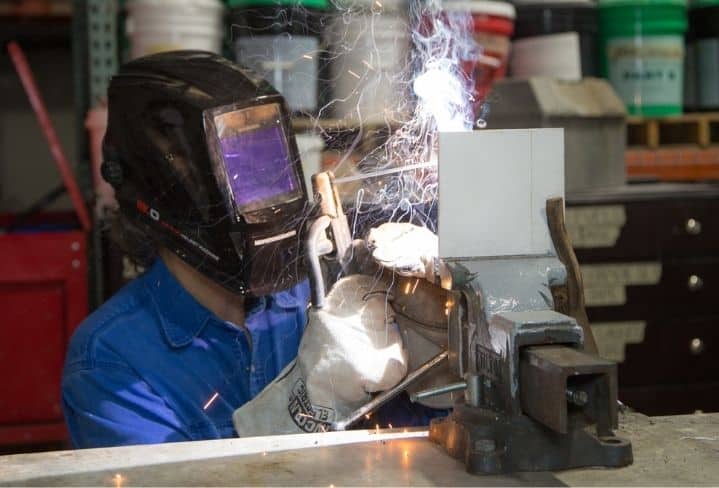
A better solution.
A better solution than cathodic protection is EonCoat. Once you coat the asset there is little to no upkeep & now with our EonCoat Weldable Coating. Tank bottoms now have another option for corrosion protection. Cathodic protection works but has its limitations. Those limitations are surpassed with EonCoat.
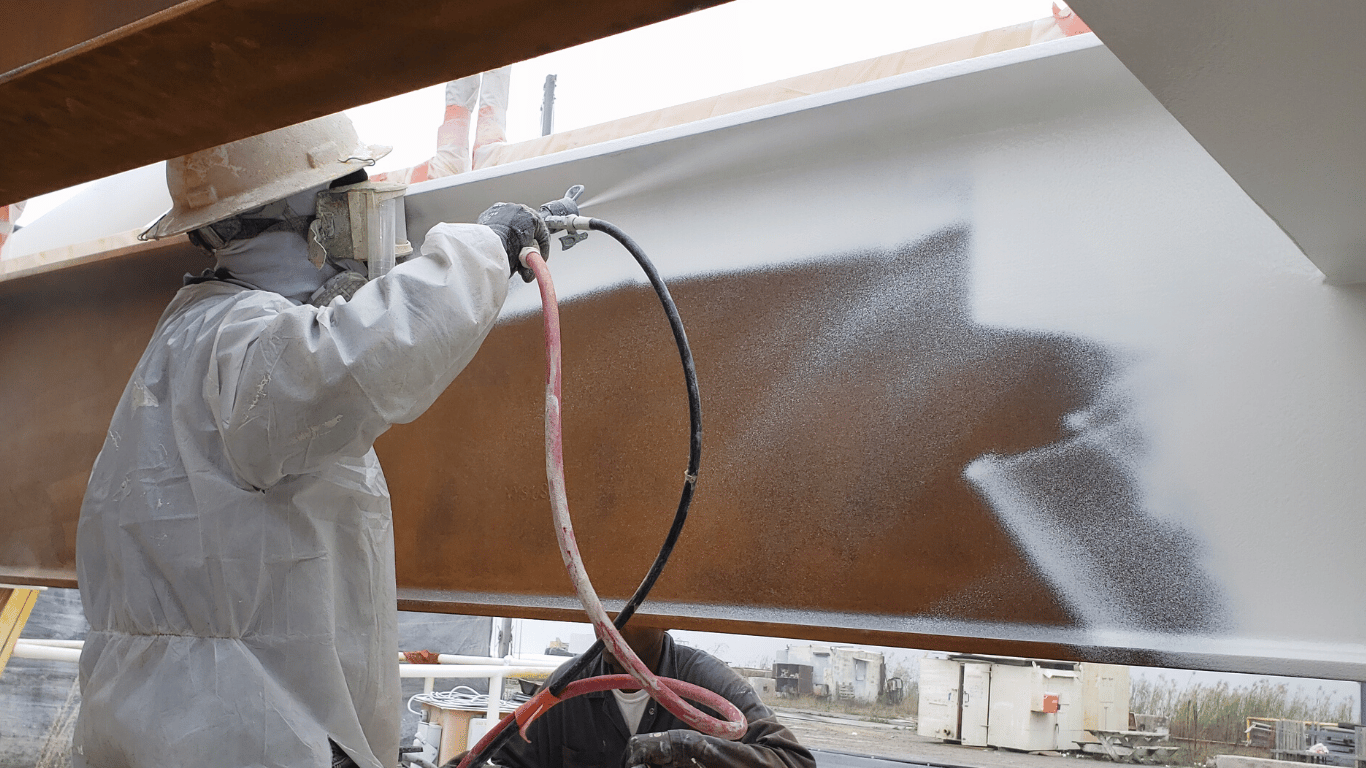
Ready to Learn More About EonCoat?
Comments are closed.