Corrosion is the top threat to the carbon steel industry, with carbon steel accounting for 85% of annual steel production worldwide.
Corrosion can occur generally or as localized attacks, most commonly through pitting, crevices, and filiform corrosion. High temperatures, chemicals, and other stressors in the environment can also cause corrosion in the form of cracking.
With carbon steel uses ranging from nuclear and fossil fuel power plants to mining, construction, and marine applications, the environments where corrosion takes its toll are diverse. Effective corrosion prevention must be able to hold strong against a multitude of environmental factors. With the sheer number of industries that rely on carbon steel assets, corrosion costs exceed 3.8% of the global gross domestic product.
Read on to learn about the environmental factors that affect carbon steel, as well as how EonCoat® defends your steel assets against these factors, to improve efficiency and protect your bottom line – no matter what industry you operate in.
Atmospheric Corrosion: Humid Environments
Imagine a perfectly dry atmosphere where metallic corrosion occurs at such low rates that it can be easily ignored. Unfortunately, this hypothetical environment does not describe most, if any, of the areas on our planet where carbon steel infrastructure is in use.
Relative humidity, temperature, precipitation, and pollutants all combine to create rural, industrial, and marine atmospheres that attack steel surfaces constantly.
The most aggressive atmospheric agents include chlorides from marine aerosol and sulfur dioxide from the combustion of fossil fuels. This means carbon steel assets in the marine and power industries are especially at risk of atmospheric corrosion.
Soil Corrosion: High-Moisture, & High-Salt
The soil that carbon steel structures sit on or around can corrode steel just as much as the surrounding air. The rate of corrosion depends on the variability of the soil.
There are more than 200 different types of soil in North America alone. Those with high moisture content, electrical conductivity, acidity, and dissolved salts will corrode steel faster.
The permeability of the soil also plays a large role, as the more access oxygen has to the steel structure, the higher the likelihood of corrosion.
High-Temperature Corrosion: Hot Environments
Almost every metal oxidizes above a certain temperature.
Certain industries — such as aerospace, chemical processing, waste incineration, and power — expose their carbon steel assets to high temperatures on a regular basis.
In addition to the effects of oxygen, sulfur-bearing gases, carbon oxides, nitrous oxides, and halogens, solid ash and salt deposits can all contribute to the corrosion of steel in these environments.
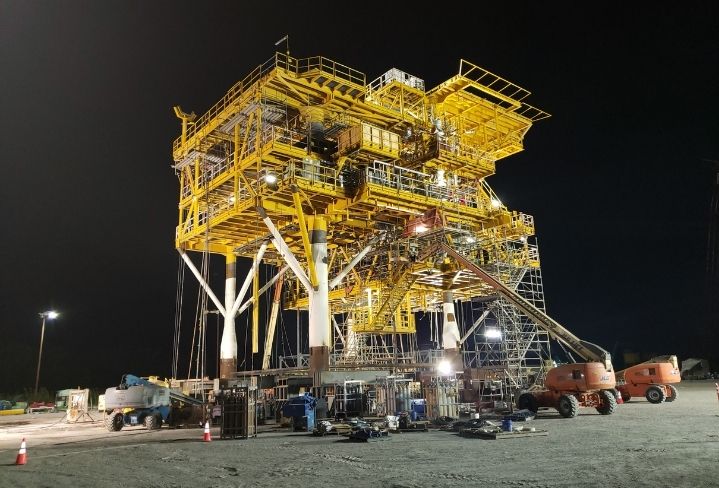
Marine Area Corrosion: Marine-Adjacent Environments
Many industries require carbon steel structures to be built near marine areas. Freshwater, seawater, and potable water each have varying steel corrosion rates determined by the oxygen content, temperatures, pH levels, agitation, and even the tide conditions of the water.
Docks, harbors, naval yards, and offshore oil and gas platforms have an especially great need to protect their steel assets, as the incessant saltwater spray is particularly corrosive.
How EonCoat® Prevents Corrosion in Various Environments
Nature throws a lot of harsh and difficult elements at our steel assets. So, how is EonCoat® able to effectively protect against corrosion in so many environments? The key is that EonCoat’s patented dual-layer system chemically bonds with steel, preventing corrosive elements from penetrating the alloy layer and reaching the steel.
Traditional methods of corrosion protection simply apply a coating that sits on top of the steel, and when that coating is chipped or damaged, the steel is again exposed to the corrosive elements of the environment. Because of this, traditional coatings often need to be reapplied and strengthened in order to continue providing protection.
EonCoat’s approach is fundamentally different from existing coating technology as EonCoat® passivates the steel by chemically bonding with it to form an alloy layer. By comparison, traditional coatings are barrier coatings that simply sit on top of the steel but do not passivate it. EonCoat’s unique formula creates an iron phosphate layer only 2 microns thick, which alloys the steel and provides the first layer of defense. The second line of defense is a white ceramic layer, 20 mils thick, which leaches phosphate when necessary to re-alloy the steel and gives added protection against abrasion, impact, and chemicals.
This eliminates the need for reapplication, as EonCoat’s inorganic primer offers long-lasting protection for your steel assets in various environmental conditions.
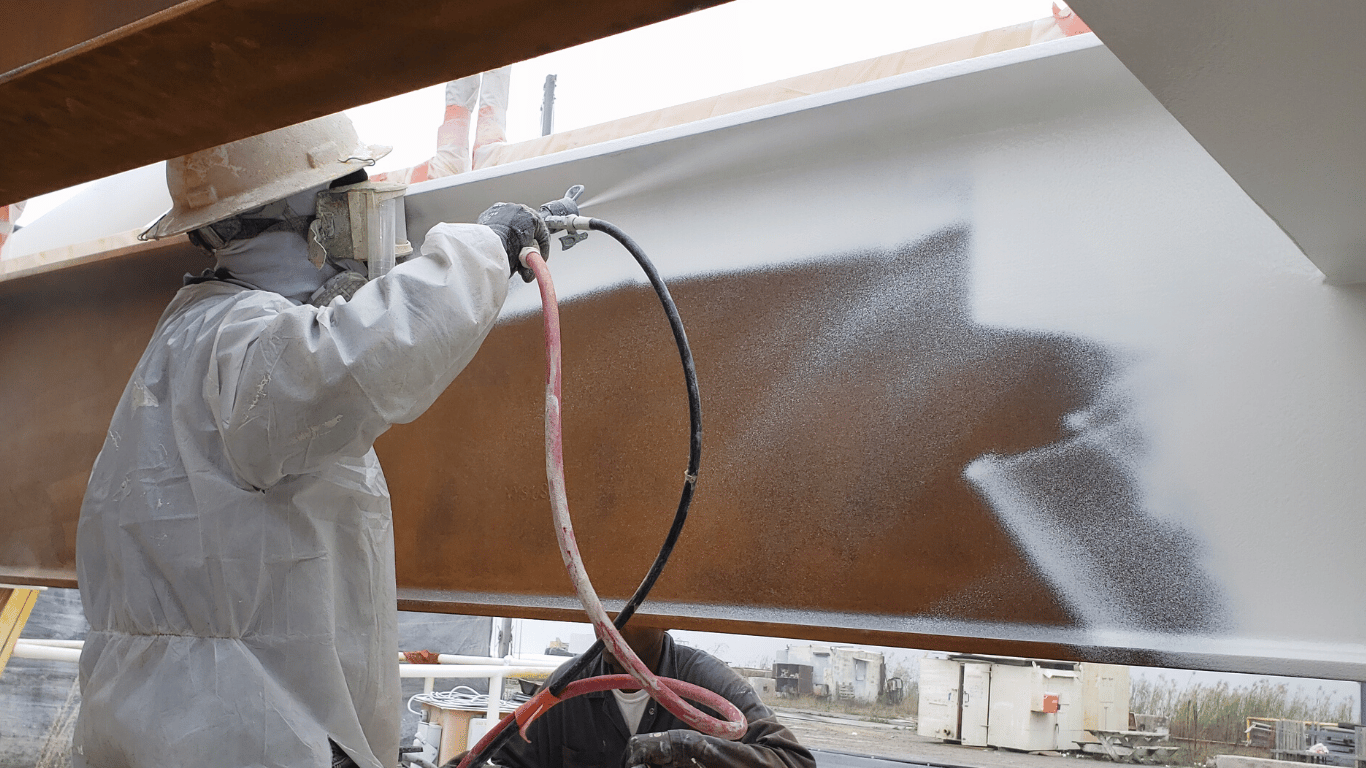
Ready to Learn More About EonCoat?