EonCoat is an anti-corrosion coating with a method of action that is fundamentally different than other commercial coatings. While traditional coatings simply sit atop the steel, EonCoat forms a chemically bonded alloy layer with the steel. And that alloy layer will re-alloy the steel if needed. Furthermore, this effective method of corrosion protection is achieved with minimal surface preparation and equipment downtime, and without VOCs, HAPs, odor, or flammability.
EonCoat’s efficacy in protecting carbon steel assets across industries has been put to the test numerous times. Read on to learn more about some of these tests.
Third-Party Testing
EonCoat underwent years of testing by leading scientists and other third-party organizations. When the American Railway Engineering and Maintenance-of-Way Association (AREMA) tested the effects of corrosion and fatigue on rail performance, it remarked that EonCoat showed “very good ability to prevent corrosive damage” after a battery of tests that included saltwater testing and drip testing. Additional fatigue tests by AREMA found that EonCoat was “effective in preventing corrosive attack … on damaged rail” as well.
NASA’s Evaluation for Environmental Risk Mitigation studied EonCoat as part of a long-term coating analysis. Of the 10 coatings examined, EonCoat significantly outperformed all others on the 18-month Atmospheric Exposure test, receiving full marks for resistance to rusting and blistering. EonCoat was also given high marks for its ease of application. Photography of NASA’s testing can be found here.
Seawater Testing
To demonstrate EonCoat’s protection against corrosion, it was placed into two challenging tests: Salt Chamber Testing and Seawater Corrosion Testing.
Salt Chamber Testing
Modeled after NASA’s sea spray test — an aggressive test designed to initiate and promote corrosion on various surfaces – a steel sample protected with EonCoat was placed in a corrosion chamber alongside samples of other anti-corrosion products. For 12 hours a day, seawater (not a salt fog as used in other tests) was sprayed on the samples. For the other 12 hours each day, the samples were exposed to a grow light, i.e. a multi-spectrum light.
By the fifteenth day of testing, the leading brand was showing signs of corrosion; after 45 days, it had severely corroded. On the contrary, the EonCoat sample showed no signs of corrosion (except on the scribe line).
Seawater Chamber Corrosion Testing
EonCoat samples were placed alongside samples of other brands in a specially designed seawater chamber of actual Atlantic Ocean seawater as opposed to a chemical formulation. Simulated sun lamps (426-nanometer light waves) would then blast the samples in four-hour intervals. The grueling test design can be further explored here.
EonCoat tested its strength against brands such as Carboline, Pitt-Tech, AFM, Sherwin Williams, and Rustoleum. Watch the entire test duration in this one-minute, time-lapsed video, and you can see the impressive results of EonCoat against other brands. Within a month, some samples began to show visible corrosion. By Day 170, all showed at least the beginnings of corrosion, and many showed much worse failure — except EonCoat.
Need to Know More About EonCoat?
What makes EonCoat so demonstrably effective?
EonCoat is an easy-to-apply anti-corrosive primer that consists of an acid and a base. These components combine to create a two-layer defense: an iron phosphate alloy layer and an outer ceramic layer. The patented coating converts the surface of the carbon steel into inert iron magnesium phosphate, resulting in a permanent alloy layer.
EonCoat then embeds a 20 mil-thick ceramic layer over the top, which serves as a phosphate reservoir for the alloy. The phosphate reservoir will re-alloy the steel if the steel and its surrounding alloy layer are ever gouged or damaged.
Because of the alloy layer, oxygen and humidity cannot penetrate EonCoat the way they can ordinary polymer paints once the surface of a traditional coating is scratched or compromised.
Get in touch with our team today to learn more about how EonCoat can benefit your company.
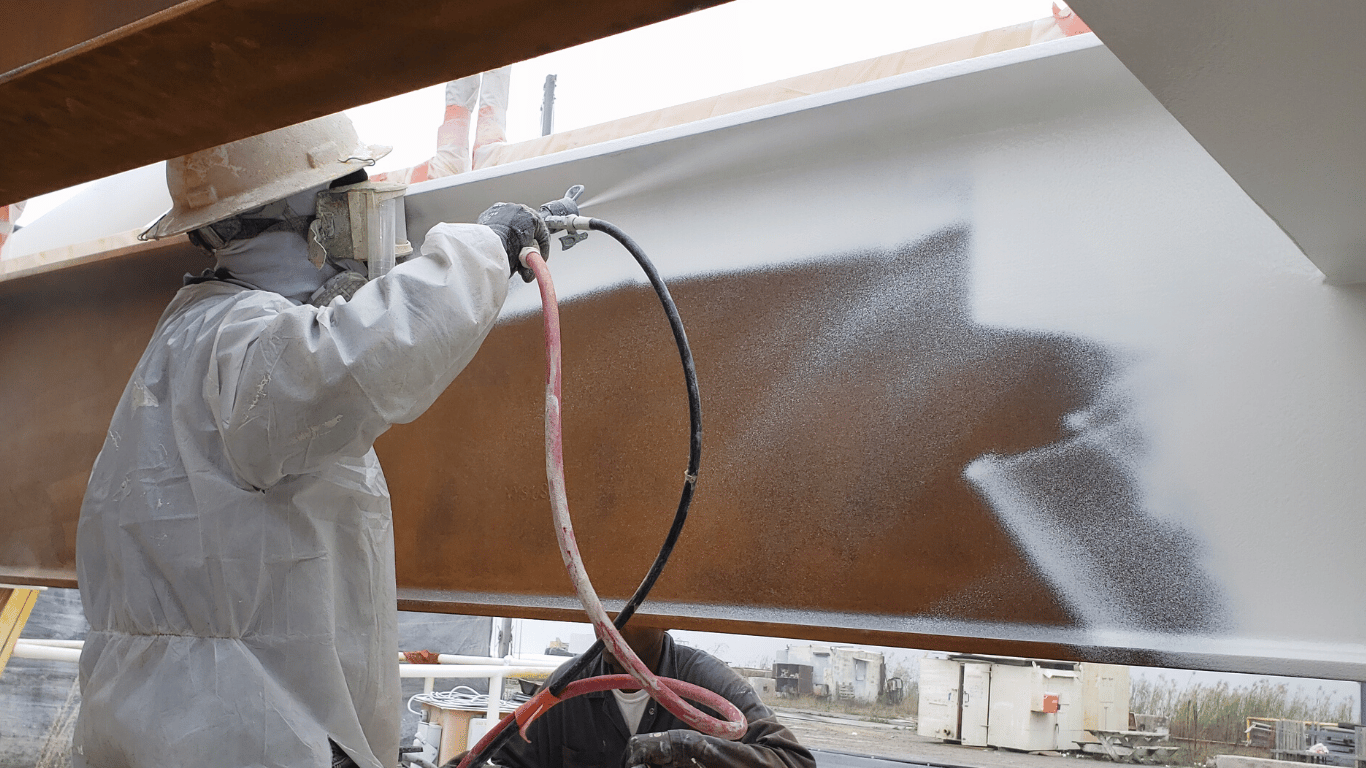
Ready to Learn More About EonCoat?