“What’s the difference between EonCoat and a three-coat paint system?” That has always been one of the most common questions our customers ask. So, when a customer from Pascagoula, Mississippi, United States, called in 2017 asking us to participate in a side-by-side storage tank corrosion-prevention coating comparison, we jumped at the chance to demonstrate the answer in a real-world setting.
Were the Storage Tanks Identical?
Because of the competitive edge provided by using EonCoat, many of our customers require a high level of confidentiality. Therefore, we will not be identifying the customer by name to honor that request. Additionally, we will refer to the tank protected by EonCoat as EonCoat Tank; in contrast, we will refer to the tank protected by the three-coat paint system as Three-Coat Tank.
Each of the two tanks represented approximately 16,000 square feet of surface area. For the EonCoat tank, the entire surface was prepared. Then EonCoat Corrosion Protection was applied to the tank surface in its entirety. For aesthetic purposes, a topcoat of Tnemec Enduratone 1028 was applied.
Meanwhile, across the driveway, Three-Coat Tank received an application of a standard 3-coat paint system. The primer was inorganic zinc, the second layer was a Hempel epoxy midcoat, and the top layer was a polyurethane layer. The two tanks are – literally – neighbors. Let’s take a look at how the neighbors did when the protective coatings were applied.
How Long Did the Applications Take?
Did we mention that in July of 2017, there were 22 days of rain in Pascagoula? Yet, despite the weather, the application project for EonCoat was completed in 9 days of labor, not including weather delays due to lightning. Yes, you read that correctly – it only took 9 days to protect a 16,000-square feet tank entirely and permanently!
When the EonCoat job was complete, we looked across the driveway at Three-Coat Tank being coated we were astounded at the “results.” The three-coat paint project was only 15% complete.
Mathematically, the three-coat system will take approximately 54 days to complete – compared to EonCoat’s 9 days. However, Sameer Patel, EonCoat’s Lead Scientist, had the opportunity to return to the customer in November, just a few months later. What did he discover? The three-coat paint system was still being applied.
How was the EonCoat project completed in only nine days?
Both projects involved applicators being in bucket lifts to cover the entire tank. In addition, both tank projects had the same weather. So, how was the EonCoat project completed in only nine days? The simple answer is that we engineered EonCoat to have straightforward surface preparation and application processes, so let’s break down the science.
With EonCoat, the entire surface was prepared all at one time and to an SSPC-SP6 / NACE 3 / SA2 standard. There was no need to hold the blast. There was no need to wait for the rain to stop or start the process after the rain.
As a chemically bonded phosphate ceramic (CBPC), the iron phosphate layer was alloyed to the carbon steel surface with trivalent magnesium-iron phosphate. The second layer provided a ceramic reservoir that reinforces the iron phosphate. The EonCoat customer received both layers of protection in one simple application using a high-pressure plural pump with stainless steel lowers. With one application, coating thickness had a WFT of 30 and a DFT of 24 – 28.
The applicators in Pascagoula did not need to be concerned about the appearance of flash rust. EonCoat can be applied on top of tightly bonded flash rust – which tells the operator the carbon steel tank substrate is reactive. We only had to stop the EonCoat application when lightning was in the area (we’re good, but we’re not that good). Now let’s compare how the job progressed on the Three-Coat Tank.
Meanwhile, on Three-Coat Tank
Meanwhile, on the Three-Coat Tank, a three-coat system means what it says. With three-coat paints, the applicators completed the surface preparation for a small portion of the area, then applied the inorganic zinc to that small portion. They then moved to another small section, completed the surface preparation, and applied the primer. They did this one small section at a time.
To quote Tony Collins, our CEO, that’s like getting out the vacuum cleaner, vacuuming one small section, putting away the vacuum cleaner, looking at the one small section of carpet … and then repeating that process over and over again.
The Three-Coat Tank applicators weren’t done after the inorganic zinc primer. They then had to apply the second coating. After the second coat was cured, they could apply the final coat. If it rained at the wrong point, they would need to start back with the surface preparation. The application job seemed to continue on and on.
So, what was the reason for the lengthy application project?
Any three-coat systems are barrier coatings. For the barrier to be effective, neither rust nor moisture can be trapped under the barrier coating. In the humidity for which Mississippi is famous, and in a July with 22 days of rain, that can prove tricky even for the most experienced applicator. In addition, having to redo work because of the weather is very inefficient.
Lessons from the EonCoat Tank
After the EonCoat Tank project, we were able to refine our messaging to EonCoat Certified Applicators and customers about three key points.
First, we strengthened our messaging to customers, emphasizing misting the substrate during the application process. to lower temperatures. While applying EonCoat during extreme (hot) temperatures, the process of misting the substrate slows the chemical reaction time and allows the full alloy bond to form between EonCoat and the carbon steel.
Additionally, we more consistently address that wind velocity isn’t the only wind factor to consider. Any applicator must also factor wind direction into the project plan. Essentially, if you spray any protective coating – including EonCoat – in the same direction the wind is blowing, you will have a higher loss ratio. Therefore, you want to spray in the opposite direction of the wind.
Finally, the EonCoat was applied to the chime while there was standing water. No protective coating can withstand application in standing water. However, because of our commitment to customer excellence, within 30 days, EonCoat’s technical team was back onsite fixing the small area.
During the follow-up visit, everything else about the EonCoat Tank project revealed a protective coating with intact integrity. We knew EonCoat would perform well. However, we wanted a little more data about the cost comparison from a neutral third party.
What was the Total Cost Savings?
One year later, the customer presented the cost comparison findings in a public forum. For all-inclusive costs, the financial estimate is that EonCoat Corrosion Protection represented a minimum 30% cost savings. Of note, the total price of EonCoat included the cost of 40 hours of technical support at the per-hour charge.
Are You Ready for Permanent Corrosion Protection?
At EonCoat, we focus on permanent corrosion protection, service excellence, and relationships. As a result, since 2017, we have had subsequent opportunities to work with this customer and protect 7 other assets with either EonCoat Corrosion Protection or EonCoat Corrosion Under Insulation (CUI).
If you’re interested in building a relationship with EonCoat to prevent corrosion permanently, click our Contact Us button below. Are you interested in beginning your journey as a corrosion prevention guru? Sign up to receive EonCoat’s Free E-Book. You’ll receive one email daily for the next five days, and your email is as safe with us as your tank is once it’s covered in EonCoat – permanently.
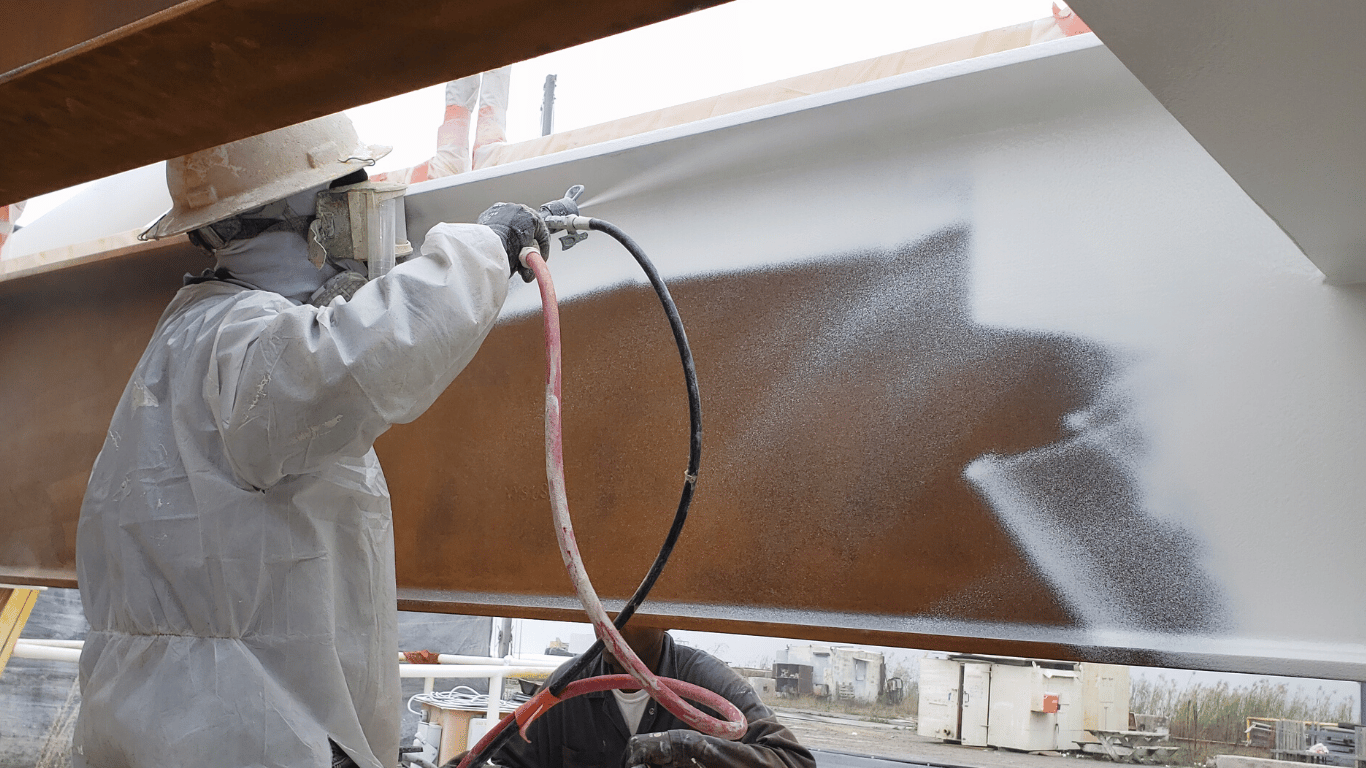
Ready to Learn More About EonCoat?