During the Spring of 2012, we had the good fortune of finding our coating in a laboratory at Hanyang University, Seoul Korea, where Dr. Ki Yong Ann (PhD., DIC., MPhil., ME., Department of Civil and Environmental Engineering ) performed electrochemical testing on our product.
Before we get into the test results a little background on Dr. Ann would be appropriate. He was not hired by us to perform these tests and is not affiliated with EonCoat. He heard about EonCoat from a third party and found the properties interesting enough that he wanted to run tests on his own. And as you can see from his impressive educational background, he’s incredibly knowledgeable about corrosion and corrosion-causing properties.
The Resume
Dr. Ki Yong Ann – EDUCATION
- DIC (2006) Imperial College of Science Technology and Medicine, London UK
- Ph.D. (2005) Imperial College of Science Technology and Medicine, London UK
- Thesis: Enhancing the chloride threshold level for steel corrosion in concrete
- MPhil (2002) Imperial College of Science Technology and Medicine, London UK
- Dissertation: Measurement techniques for steel corrosion in concrete
- ME (2000) Hanyang University, Seoul Korea
- BSc (1998) Hanyang University, Seoul Korea
He was kind enough to share his results with us and we thought it important to share some of that knowledge with you.
The surest way to test for the potential of corrosion – early indications of whether or not it has the potential to corrode – is to do an electrochemical test. These tests are costly and must be performed by experts who have the knowledge and experience to execute them correctly.
The Results
The simplified version of an electrochemical test is:
- Place the samples (in this case steel plates coated with EonCoat) in a beaker with saltwater
- Run voltage through the solution and measure the corrosion rate by measuring the leakage (what kind of current leakage there is across the coating)
- The leakage is measured in milliamps per square meter
- Simply put, the more amps that are flowing, the more corrosion will take place on the substrate
In a test such as this, the expectation is that a typical uncoated plate would measure about 150 milliamps per square meter. A coated plate should perform better. If a coated plate improved the rate of corrosion by a factor of 10, the result would be 15 milliamps per square meter, which would be a very good corrosion-resistant coating.
EonCoat coated plates tested at 1.15 the first time, and .85 the second. Anything below is 2 is considered to have no corrosion potential.
We couldn’t be happier that Dr. Ann took such an interest in our coating and shared his test results with us. We are very grateful for his willingness to share his findings.
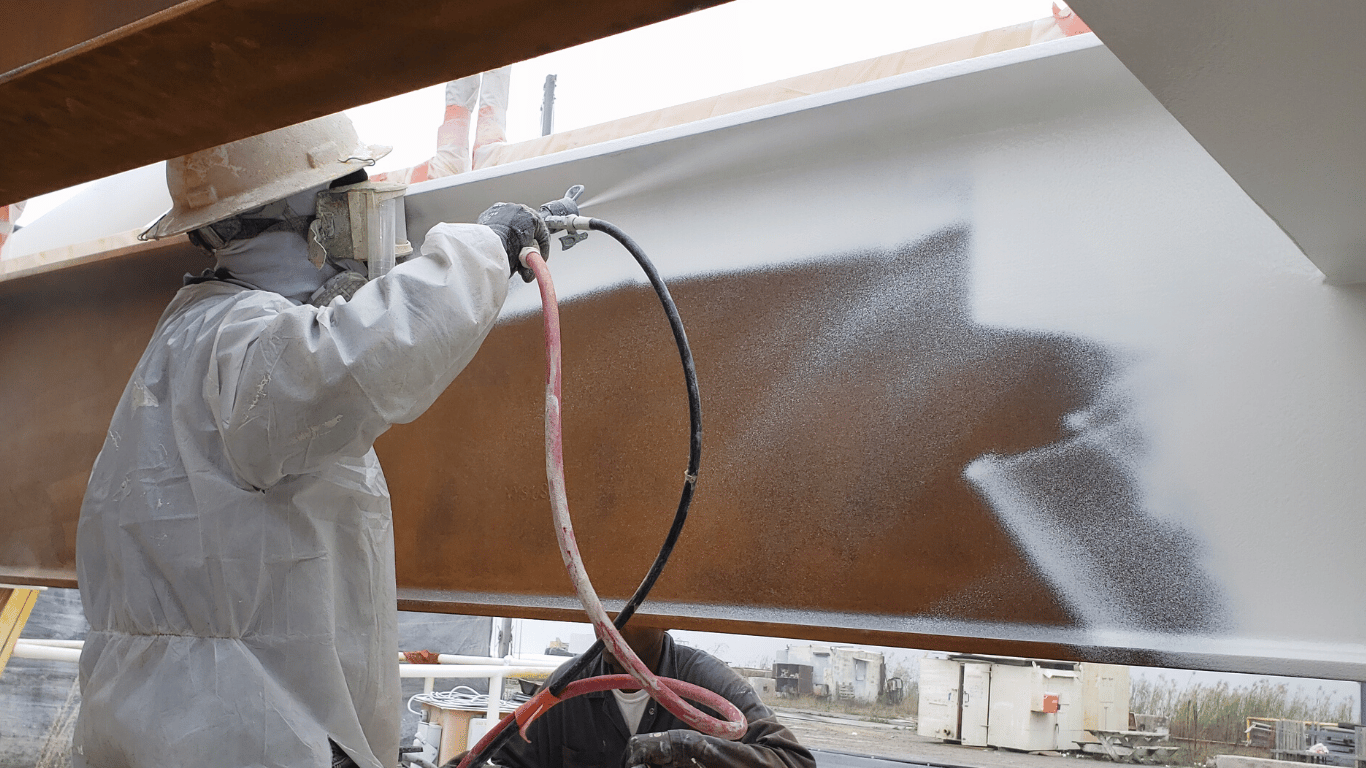
Ready to Learn More About EonCoat?