You may be surprised to learn that not all steel is created equal. In fact, there are three definitive types of carbon steel, all with their own specific uses and features. The type of carbon steel also determines how well it alloys with other components, which is vital when it comes to corrosion prevention. Whenever you’re looking to work with carbon steel, it’s important that you identify which type you’ll need and if it will need any alloy additions or heat processes to increase its strength.
In order to demystify the various types, we’ll define the three-carbon steel types below — take a look at their description and use cases to determine which type is right for your project.
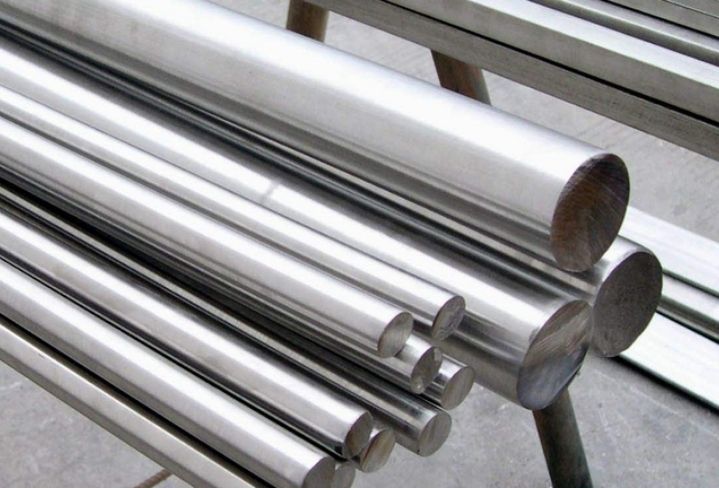
Low Carbon
Also known as “mild steel,” low carbon steel is the cheapest option in terms of value, but it’s also easy to bend and shape, which makes it perfect for a multitude of uses (including sheets, screws, and concrete reinforcement bars). It can be frequently found in the kitchen in the form of cookware or eating utensils (stainless steel is low carbon), but this steel type’s low carbon content means it’s unsuited to being case hardened (but it can stand up to the dishwasher without rust forming).
Although it’s not quite the strongest steel in its natural state — just think of how easily you can bend a stainless steel spoon with your hands — other alloys can be added to increase or modify its base properties. This can include adding aluminum for drawing quality or increasing the manganese content for structural steel. To raise the strength of low carbon steel, even more, the surface hardness can be increased through the process of carburizing, which makes it more resistant to abrasion.
Medium Carbon
Medium carbon has a slightly higher base carbon component than low carbon (0.31% to 0.60%, as opposed to low carbon’s 0.04% to 0.30%) and a bit more natural manganese as well. Because of this, medium carbon may be stronger than low carbon, but it’s also more difficult to shape. It’s still got many uses, however — thanks to its strength and wear resistance, it’s perfect for various machine or car parts.
Medium carbon typically has alloys like chromium, nickel, and molybdenum added in order to increase its stress resistance — perfect for creating items such as studs and gears that will encounter a lot of wear and tear. If additional hardening is needed, medium carbon steel can be heated and held until it reaches a uniform temperature, then soaked and cooled.
High Carbon
Also known as “carbon tool steel,” the strongest carbon steel you can buy is also, as expected, the most inflexible. High carbon steel has more carbon than the other two types (between 0.60% and 1.4%), yet it too can accept alloys in order to change its properties. Chromium and manganese alloys can be added to high carbon steel while it’s being formed to help the material avoid corrosion. It’s also an ideal type of steel to subject to heat treatments in order to increase its hardness.
One thing to keep in mind, though, is that heat treatments can make high carbon steel very hard but also brittle, which means that other measures need to be taken to prevent cracking. The Misumi blog uses the example of 52100 steel, which is commonly used for linear shafting, and notes that the surface is hardened for loaded ball contact while the inner core remains unhardened, so the shaft does not become brittle on the inside.
Choose Your Steel Wisely
When you’re determining what kind of carbon steel to work with, it’s important that you familiarize yourself with the different properties of each of the three types: low, medium, and high. Depending on what the material is being used for, you’re going to want to choose the type that best suits your needs, or that can best be treated with additional alloys or heat in order to make it perfect. In any case, don’t forget to equip your carbon steel with a good anti-corrosion coating — it can make all the difference in the lifespan of steel.
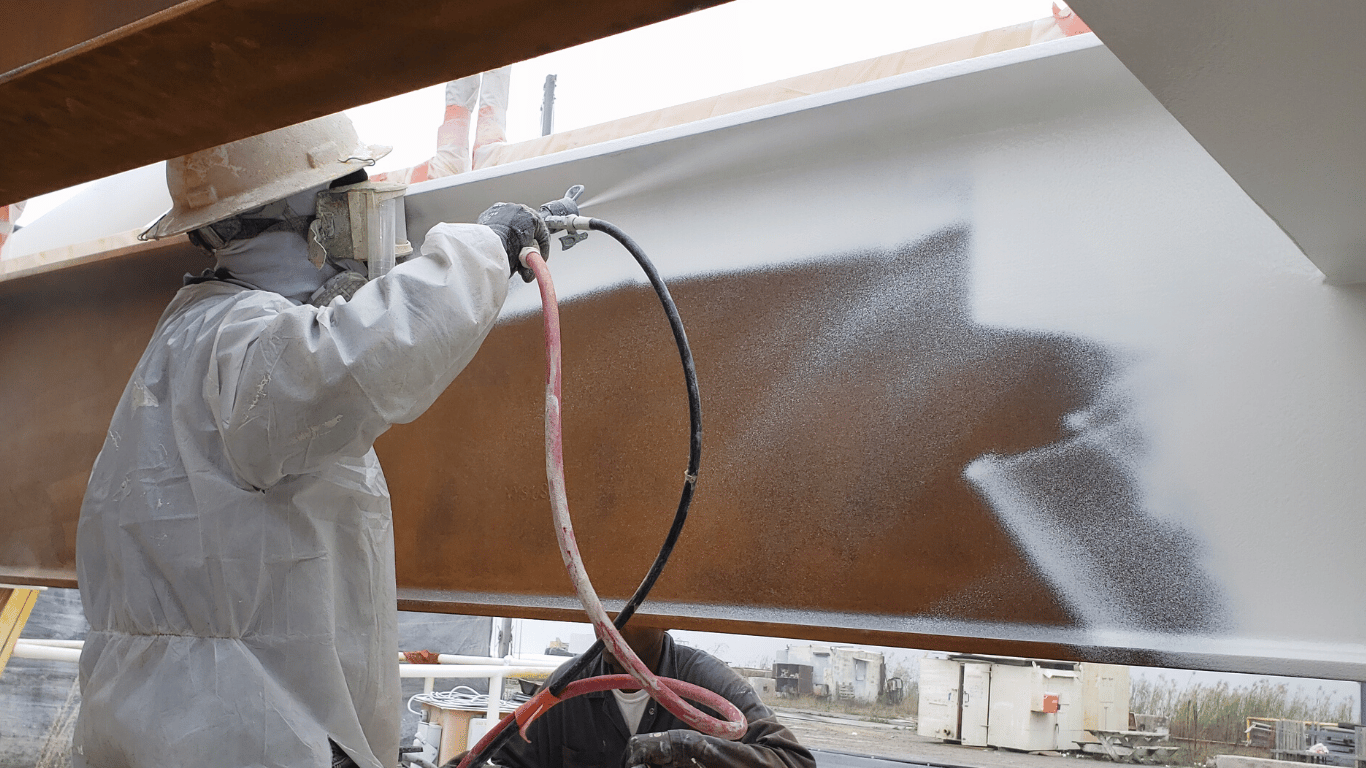
Ready to Learn More About EonCoat?