My favorite math teacher was famous for saying, “Numbers tell a story. What story are you reading?” That sentence is both authentic and true when you look through the lens of valid and reliable third-party testing. The data from independent, professionally recognized, third-party testing:
- maintains a documented chain of custody for testing materials,
- adheres to the ASTM, NACE, AMPP, or other professionally recognized standards for testing,
- ensures a standard unit of measurement for success,
- eliminates researcher bias, and
- results in a report showing all conclusions – without regard to the desired outcome.
This blog will look at just three of the third-party tests that EonCoat has completed. Additionally, we will break down the science and data for you to review. Then, we’ll see “what story the numbers tell us.” Let’s start with a well-known test, ASTM B117.
Who Completed EonCoat’s ASTM B117 Testing?
The American Society for Testing and Materials (ASTM) develops voluntary consensus standards, products, systems, and services. ASTM makes it easier for global companies like EonCoat to do business because standards don’t change, even if the language does. EonCoat had its ASTM B117 testing completed by the highly recognized folks at Assured Testing.
What is ASTM B117?
The ASTM B117 was initially developed in 1939. Essentially, the test,
“is a non-cyclic test, which means that the surface is continually exposed to “salt air.” In this test, the panels are exposed at a 15 to 30 degree angle from vertical to continuous deposition of an atomized 5% NaCl (sodium chloride or salt) solution at 35 degrees Celsius and 97% humidity.
In the test, EonCoat was spray applied to the sample panels. Next, a scribe line was created on the sample panel, as seen in the image below. Then the testing commenced for 1,500 hours. While most coating manufacturers stopped at 1500 hours of testing, EonCoat continued testing until we reached the 5,000-hour test mark.
What Does the Data from the ASTM B117 Say About EonCoat?
EonCoat passed with flying colors (pun intended, because EonCoat doesn’t come in colors!). The corrosion that formed in the scribe line did not creep any further. See the image below for your visual inspection. The photos show the EonCoat-protected sample panel after 5000 hours in the chamber.
When you apply EonCoat to carbon steel, a contiguous and intimate bond is formed between the coating and the substrate. The scribe line is placed on the panels to test corrosion creep under any barrier coating. EonCoat has an intimate chemical bond to the steel and carries reserves of phosphate. Therefore, the corrosion stops at the scribe line and does not creep under the coating.
To see how a three-coat protective paint system would perform, consider the picture below:
Our competitor is on the left, and EonCoat is on the right. As you can clearly see, the corrosion formed in the scribe line, as expected. However, for the carbon steel “protected by” the three-coat paint system, the corrosion continued to creep to the end of the panel. For EonCoat, there is simply a scribe line of corrosion.
EonCoat stopped corrosion in its tracks. The story of EonCoat is that 0% corrosion is the right number! Now that we know what the numbers tell us from one of the oldest coating tests let’s look at the number from one of the newest tests around.
What is a Houston Pipe Test?
A large oil and gas company in Houston, Texas, United States, decided to test EonCoat’s Corrosion Under Insulation (CUI) coating. To be clear, currently, there is no standardized test for CUI coatings. We were excited about the opportunity for testing to occur independently from our headquarters in Fuquay Varina, North Carolina.
When you look at the picture below, the test is for pipes protected by EonCoat, which are subsequently wrapped in insulation.
The Houston Pipe Test simulates heat, moisture, and cooling. As you can see from the graph below, the pipes were heated while exposed to moisture. The heat was maintained for 8 hours. The pipes were then allowed to cool normally for 16 hours. This 24-hour model was repeated a total of 30 times.
Why Is Testing For CUI Protective Coating Important?
CUI is prevalent in carbon steel when the temperature range is between -4° C (24.8° F) and 175° C (347° F). EonCoat’s CUI protective coating is important on mission-critical pipes because:
- The insulation, which is needed due to thermodynamics, traps moisture, causing a significantly increased level of corrosion.
- Most other coatings fail because of the temperature ranges.
- If the insulation must be removed so the pipeline can be inspected, the pipe must be shut off, causing lost production opportunities (LPO). LPO is when you lose revenue because you must take a pipe out of production to inspect and/or make repairs.
- EonCoat CUI is cured in 15 minutes compared to hours or days for other coatings. This also reduces LPO.
The need for a corrosion-resistant CUI coating becomes essential when you consider everything pipelines carry today.
What Does the Houston Pipe Test Say about EonCoat?
Once again, EonCoat outperformed the test result expectations and amazed everyone involved. When the testing was complete and the insulation was removed, there was no corrosion on the pipe. See for yourselves in this next image – 0% corrosion is the number that tells the story here.
We’ve shared how 0 is the right number for corrosion creep and CUI on pipes. Now let’s turn our focus to why 0 is also the right number when you talk about VOCs, HAPs, and Toxins.
What’s the Right Number for VOCs, HAPs, and Toxins?
Columbia Analytical Services performed the test that allows us to report that EonCoat has 0 VOCs, HAPs, Toxins, or Odor. The report acknowledges the chain of custody for samples, giving the test and subsequent report both validity and reliability.
When you ask about VOCs, HAPs, and Toxins, there should only be one number – 0. This is because no VOCs, HAPs, Toxins, or Odor should be in any protective coating. EonCoat has eliminated all of them. Let’s dig into why 0 is the correct number for both the applicator and the environment.
VOCs and HAPs – Stop Using Them
Before we dig into the test results, let’s ensure we’re all using the same language. According to the EPA, a VOC (volatile organic compound) is “a compound that contains carbon and reacts with nitrogen oxides in the presence of sunlight to form ozone.” Likewise, HAP (a hazardous air pollutant) “are air pollutants that are known to cause cancer and other serious health impacts.”
When you look at the EPA’s list of VOCs and their list of HAPs, you quickly realize why every protective coating applicator, contractor, and community with corrosion should demand the removal of VOCs and HAPs. The short- and long-term health implications and environmental impacts are devastating.
EonCoat has eliminated VOCs, HAPs, and Toxins through its safety-first engineering and the use of plural pumps. We eliminated the dangerous toxins and solvents by keeping EonCoat Part A (acid) and Part B (base) separate until they mix, atomize, and reach the surface.
Consider the following highlights quoted directly from the report:
- When discarded or spilled, this product is neither a hazardous waste as defined in current federal regulations 40 CFR, Part 261 (RCRA) nor toxic pollutant as currently defined by the federal EPA per section 307 of the clean water act.
- This product does not contain any substances that are considered by OSHA, NTP, IARC, or ACGIH to be “probable” or “suspected” human carcinogens.
- Waste from this product is not hazardous as defined under the Resource Conservation and Recovery Act (RCRA) 40 CFR 251.
- Not regulated for transportation.
- No ingredient in this product are subject to SARA 313 (40 CFR 372.65C) notification.
Even the numbers in the CFR (Code of Federal Regulations) tell a story. Every protective coating manufacturer knows those numbers. The difference is that you select EonCoat to protect your carbon steel – so you don’t have to worry about it.
EonCoat’s Numbers Speak for Themselves
When the data results from third-party testing result in statements like the ones above, the numbers have told a story. The story of EonCoat is about applicator and environmental safety. It’s the story of permanent corrosion protection. It’s the story of millions of dollars saved for just one offshore platform for an oil company.
Are you interested in learning more about EonCoat, its numbers, and its technology? Click the banner below to sign up to receive our Free E-Book (we never sell your email address). You’ll receive one email daily for five days and be prepared to begin permanently tackling corrosion.
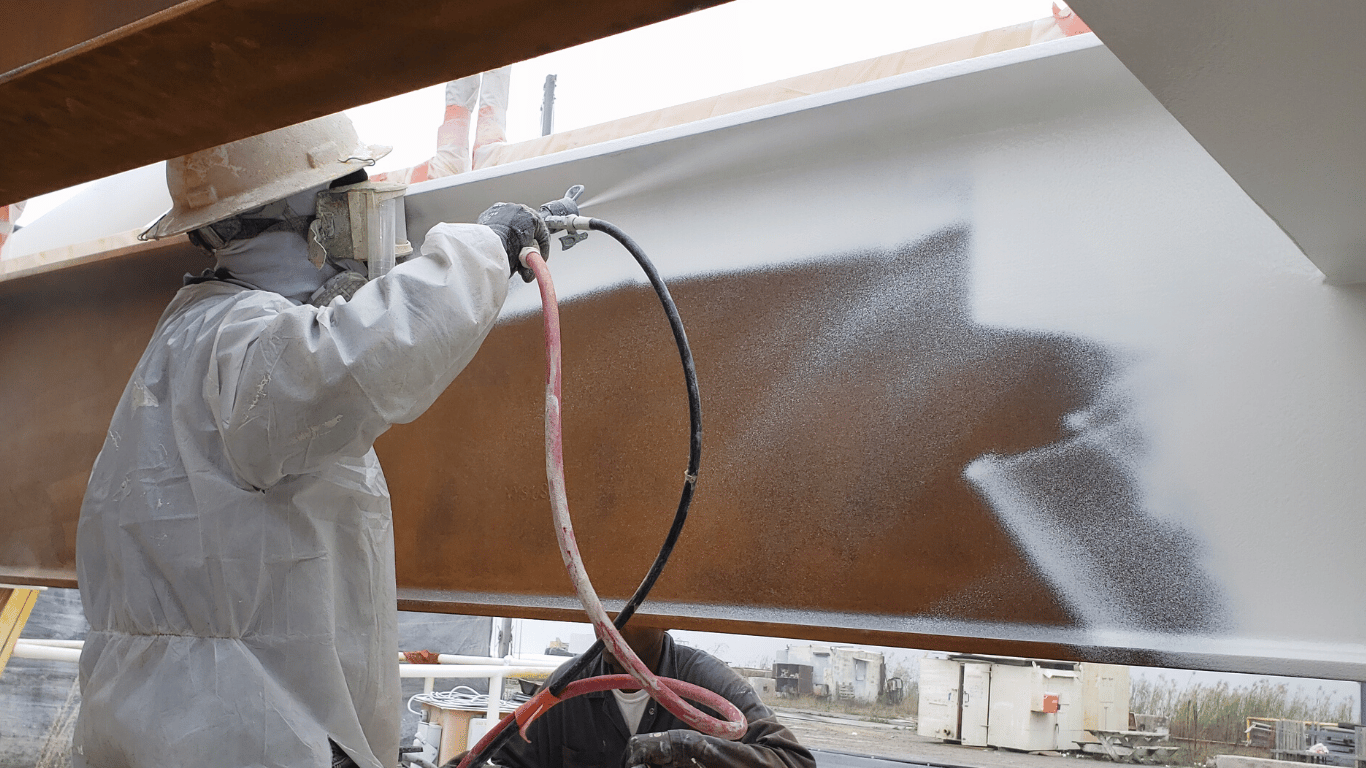
Ready to Learn More About EonCoat?