There are many ways to prevent corrosion and galvanization is one of the most popular. Galvanization involves coating the base metal with zinc for protection from the outside environment. Despite its widespread use, there are dangers to galvanization, and we’re not just talking about the costs to your business! Read on to learn about the drawbacks of this process and how they compare to other solutions like EonCoat.
The Basics of Galvanization
Galvanized metal is everywhere around us, from stop signs to car parts. This is because metals are prone to corrosion (rust is a common form of corrosion). Companies use various methods to protect their metal goods, including galvanization. Specifically, galvanization protects in the following ways:
- Creates a protective layer that separates the base metal from its environment. The zinc layer on the lamp post protects it from wind, rain, and ice.
- Protects the base metal through galvanic corrosion. The zinc layer has different electrochemical properties from the base metal. When both are in the presence of an electrolyte, the zinc layer corrodes at a faster pace while the base metal corrodes at a slower pace. In other words, the zinc layer is sacrificing itself to protect the base.
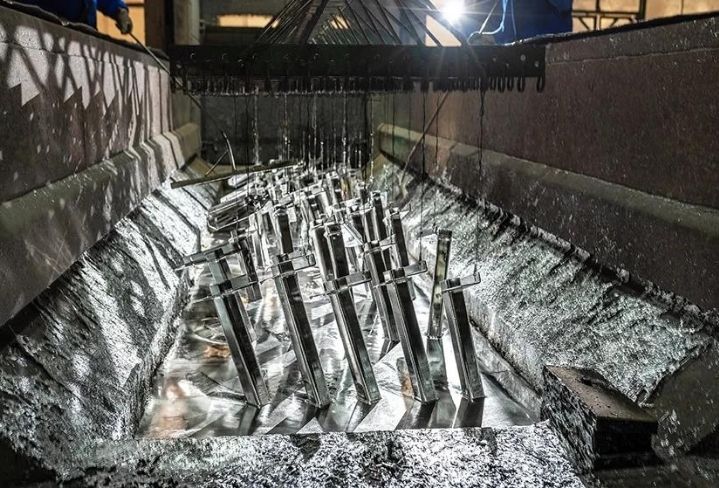
Types of Galvanization
Let’s walk through the four different ways companies galvanize their metals:
- Electro galvanizing: The metal is placed into an electrolyte solution, typically zinc cyanide or zinc sulfate. The zinc will then grab onto the metal to create a layer of protection.
- Hot-Dip: The metal is placed in a bath of molten zinc. Alloy layers and an outer layer of zinc are created by the reaction between the molten zinc and the base metal.
- Metallic Spraying: A zinc coating is sprayed onto the base metal, then heated to form the protective layer.
- Sherardizing: The metal is placed in a closed container with zinc powder. The container is then heated in a furnace, where the zinc melts to form a protective layer around the base metal.
Drawbacks and Dangers
Unfortunately, galvanization doesn’t come without drawbacks. First, scratches or peels that cut through the zinc layer make the base metal vulnerable to outside elements. For example, a deep scratch on a lamppost leaves the possibility for water to seep through during the next rainstorm. This could lead to corrosion over the moistened area and spread throughout the rest of the post. Lampposts aside, compromised metals can result in dangerous situations. Galvanized water pipes that corrode can release lead into the water supply — a little more concerning than a corroded lamppost.
Dangers with galvanization also lie in the processes themselves. Hot-dip and sherardizing involve molten solutions, which pose risks to worker safety. Exposure to fumes from zinc oxide or magnesium oxide can cause metal fume fever.
Finally, companies can’t dismiss the environmental effects of galvanization. Areas near industrial plants can see higher levels of zinc in their water supplies if wastewater isn’t treated properly. This could lead to a rise in acid levels which would affect nearby wildlife. Though zinc is a more sustainable element than lead, human error can still lead to environmental impacts that outweigh the benefits.
EonCoat – The Safer Solution
Skip the dangers of galvanization and turn to EonCoat for corrosion protection. Our two-part ceramic coating is completely inorganic, eliminating the possibility of corrosion starting from within the protective layer itself. The coating spray can be used with any industrial pump, eliminating the need for using dangerous chemicals or processes. Finally, the outer layer, a phosphate reservoir, replenishes the inner alloy layer to prevent exposure from cuts or peels. While Galvanization isn’t going away anytime soon, EonCoat is a safe and more effective solution that companies are sure to take notice of.
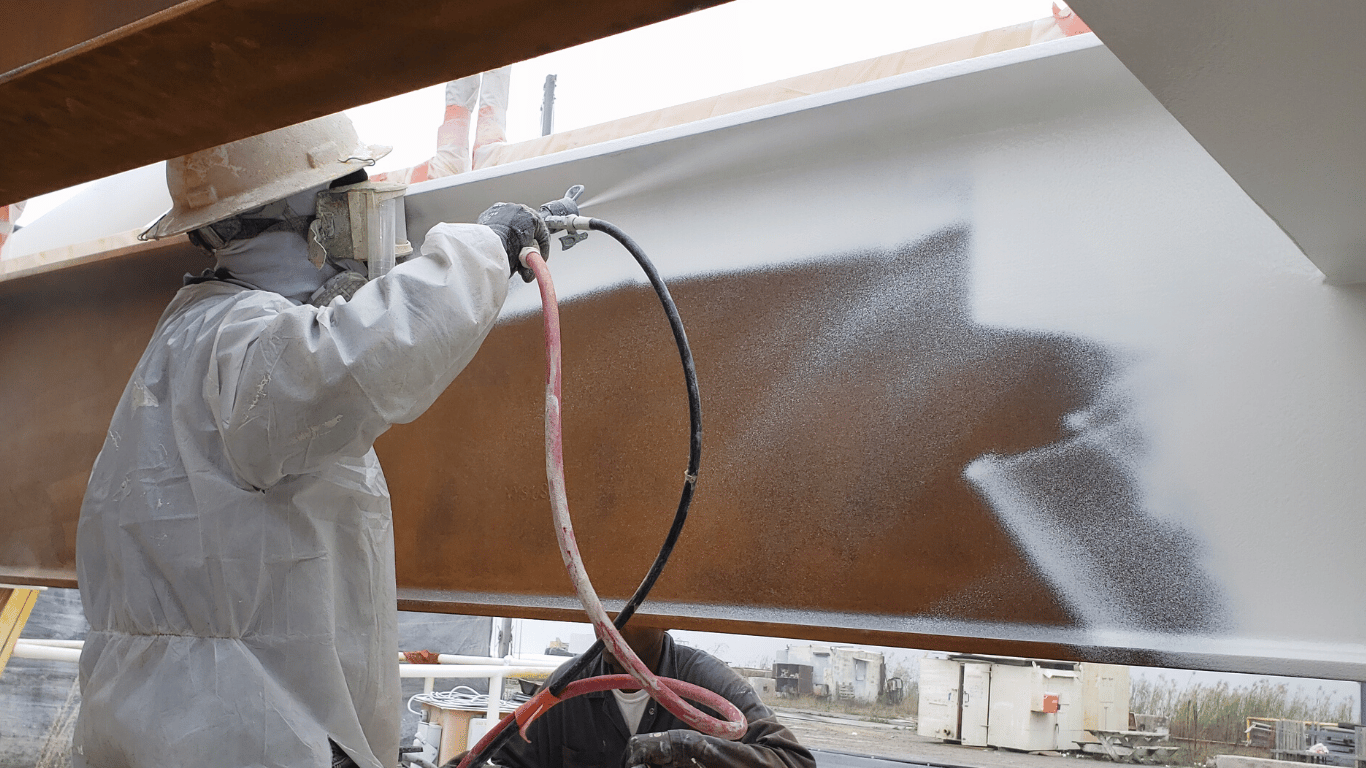
Ready to Learn More About EonCoat?