The global cost of corrosion was estimated in 2016 by NACE International at $2.5 trillion, but 15-35% of this cost could be curtailed using pre-existing corrosion-control methods.
If you work in utility, transportation, infrastructure, government, or production and manufacturing (inclusive of the oil and gas industry), your industry is one of the most likely to be affected by the high costs of corrosion.
The cost to your bottom line comes in the form of equipment downtime, maintenance costs (80% of the $7 billion annually spent on monitoring American pipelines is related to corrosion), replacing expensive rigs, and the threat to human safety and wellbeing — making it imperative to understand the significant threat of corrosion, and how to safeguard your organization.
Identifying Corrosion
While some forms of corrosion — like pitting or crevice corrosion — are easily identifiable, many others (including some of the most dangerous) require professional examination. Erosion, intergranular, fretting, cavitation and exfoliation corrosion, as well as selective leaching (or de-alloying) are each significant threats.
Specifically, environmental cracking (from cold work, welding, machining, grinding, shearing, bending, crimping, and riveting) can cause stress corrosion cracking, corrosion fatigue, and/or hydrogen embrittlement — the latter of which was found in 2013 in the eastbound span of Oakland Bay Bridge. These potentially costly and life-threatening issues must be tested, monitored, and prevented by professionals using top-grade technology.
The Oil & Gas Industry
The oil and gas industry must be particularly conscious of the costs of corrosion, especially considering that 40% of all steel produced is allocated just to replacing steel that has previously corroded. Monitoring is crucial in the production flowline, water injection systems, and import and export lines — 36% of a refinery’s maintenance costs relate to mitigating corrosion, and upwards of half of all pipeline leaks occur due to corrosion.
With machinery and rigs rusting at rapid rates, especially in high corrosion sectors, prevention and protection is of utmost importance. Corrosion is often found at the bottom of pipes, where even modern monitoring technology struggles to adequately reach and treat the assets. For many industries, corrosion inhibitors and coatings are the first line of defense against losing their assets to rust.
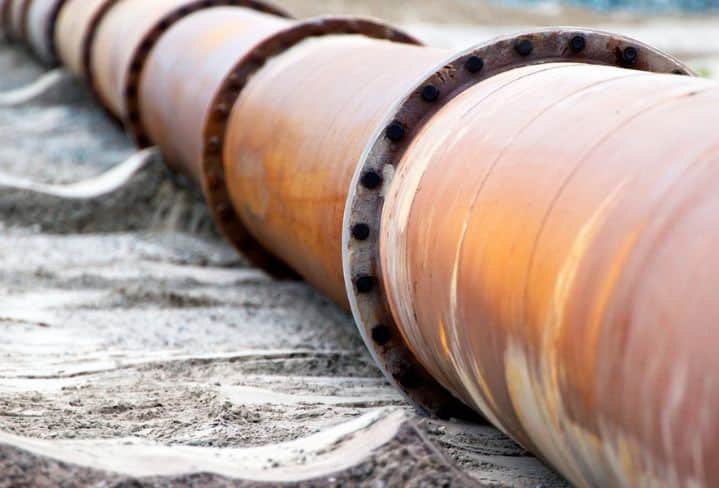
Pipeline Problems
Despite improvements to pipeline integrity and monitoring after the dawn of the new millennium, costly and dangerous pipeline failures continue to occur. Over the past three decades, pipelines have cost nearly $7 billion in property damages.
Indeed, the trend is worsening. From 2010 to 2013, the average number of incidents annually topped out at 67. Meanwhile, the total number of U.S. pipelines transporting hazardous liquids have increased by more than 11% since 2004. As the American pipeline infrastructure continues to age (most of it was built in the 1960s and added onto, not replaced), these critical incidents will only increase if corrosion is not mitigated or controlled.
The Worst-Case Scenario
Corrosion and damage to pipelines and steel structures will hurt your bottom line due to maintenance and repair, but far worse are the costs when corrosion hurts people in your community.
According to ProPublica, pipeline accidents have killed more than 500 and injured more than 4,000 over the past thirty years. In one such example, a 2010 Pacific Gas and Electric pipeline explosion in San Bruno, California, killed eight and injured dozens.
A judge recently ordered PG&E to take out 60-second television ads and full-page ads in the San Francisco Chronicle and Wall Street Journal to explain their offenses and describe how they will prevent future disasters like the San Bruno explosion. PG&E was also required to pay a $3 million fine, and they have been sentenced to five years of probation and independent safety monitoring, as well as 10,000 hours of community service.
The Best Way to Combat Corrosion is to Prevent It
With the annual cost of corrosion coming in at $276 billion in the US, companies can’t afford not to protect their steel assets. Prevention is integral to avoiding expensive repairs and upkeep, plus harm to the public and the environment.
Using EonCoat’s proprietary coating system, you can fully prevent corrosion in your carbon steel assets and protect your bottom line from the high costs of maintenance, damage, and disaster repair for decades. Requiring only a thin layer of topcoat and no intermediate coating, EonCoat saves companies on application costs in the short term and corrosion-related maintenance costs in the long run.
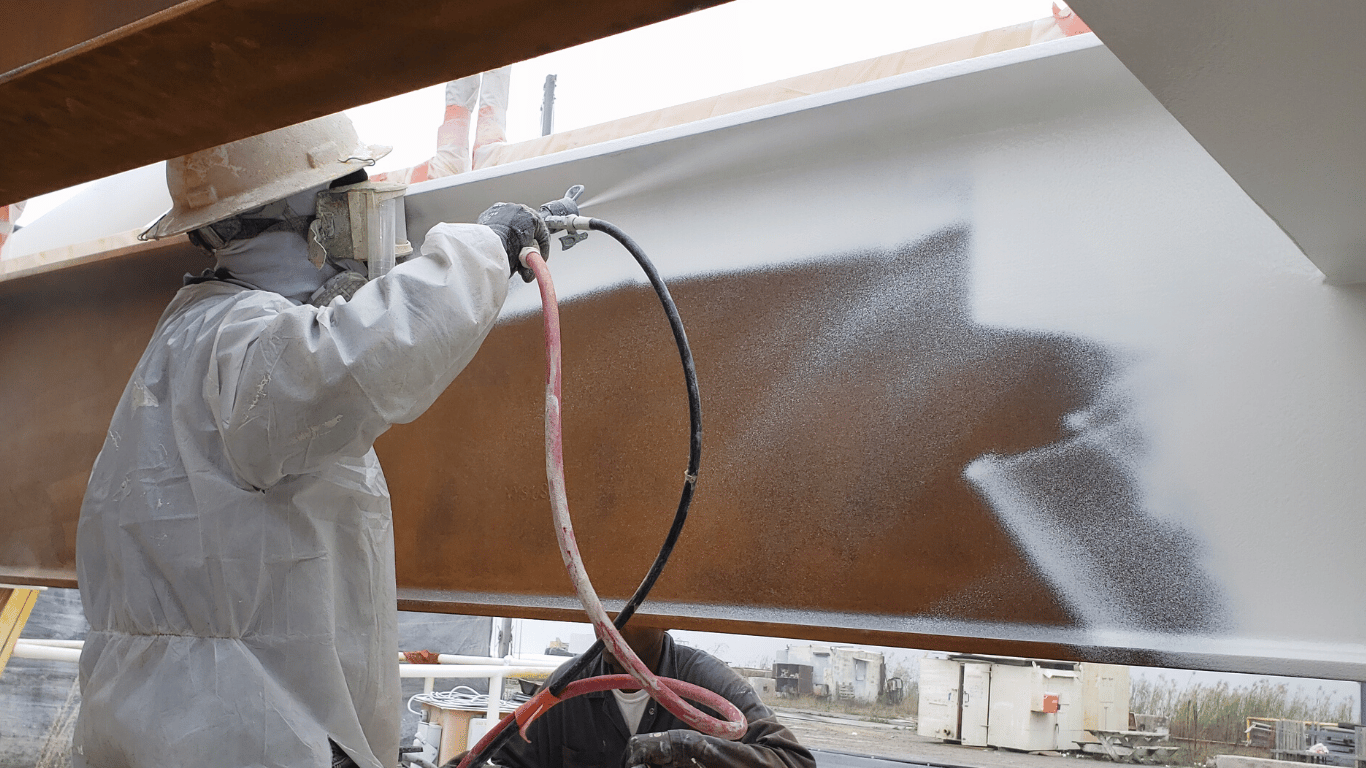
Ready to Learn More About EonCoat?