Corrosion takes many different forms. Some types of corrosion, such as pitting or crevice corrosion, are easily identifiable by visual inspection. Others, like cavitation or exfoliation, may need an additional examination to identify.
But there are three types of corrosion, each a form of environmental cracking, that can only be detected with an optical microscope or an electron microscope: stress corrosion cracking (SCC), corrosion fatigue, and hydrogen embrittlement. Read on to discover environmental cracking and the damage these three types of it can each cause to carbon steel and other metals.
Environmental Cracking
Environmental cracking refers to the brittle fracture of normally ductile metal, caused by the effects of corrosion in the environment.
Stresses that cause environmental cracking include:
- Cold work;
- Welding;
- Machining;
- Grinding;
- Shearing, punching, or cutting;
- Bending, crimping, or riveting.
The cracks form and spread at right angles in the direction of the tensile stresses. The material fractures under lower stress levels than would normally cause fractures if the material was in a non-corrosive environment. When the cracking penetrates more deeply, it weakens the material’s supporting cross-section and causes structural failure due to overload.
Grain boundaries are not positioned in a regular crystal array. An anodic electrode potential results from increased strain energy. Consequently, corrosion can arise selectively along grain boundaries.
Stress Corrosion Cracking
Stress corrosion cracking (SCC) is the result of tensile strength in a corrosive environment. SCC typically occurs in specific combinations of alloy and environmental stress. It is classified as a catastrophic type of corrosion, because it’s difficult to detect the fine cracks, and the damage isn’t easy to predict. Failure may happen without warning, and with minimal material loss.
SCC doesn’t usually attack the metal’s surface. Fine cracks penetrate the material, which when examined under a microscope, reveal an intergranular structure or a multi-branched “lightning bolt” transgranular structure. SCC fractures appear brittle to the naked eye.
Stresses that cause this type of corrosion include:
- Cold deformation and forming;
- Welding;
- Heat treatment;
- Machining and grinding.
See how are EonCoat Weldable Coating is changing the way we protect our welded steel assets from corrosion.
Corrosion Fatigue
Corrosion fatigue occurs when corrosion is combined with repeated cyclic loading at lower stress levels to cause metal fractures. Corrosion fatigue ruptures the protective passive film, causing quicker corrosion. Because of its exposure to a corrosive environment, the metal failure can take place within a shorter time or fewer cycles than in a non-corrosive environment.
Fatigue corrosion is commonly brittle, with transgranular cracking that doesn’t present the branching found in SCC. The corrosive environment can produce faster growth of cracks and/or growth at a lower tension level than in dry air.
Stresses that cause this type of corrosion include:
- Cyclic stresses;
- High-stress concentration;
- Rapid changes of loading, pressure, or temperature;
- Internal stress;
- Fluttering;
- Vibration-producing or vibration-transmitting design.
Hydrogen Embrittlement
Hydrogen embrittlement is a type of corrosion that causes metals to become brittle and fracture due to the ingress and diffusion of hydrogen into the material. The higher the strength of the steel, the more susceptible it is to hydrogen embrittlement. This makes aluminum alloys, titanium alloys, and electrolytic tough pitch copper the main contenders for this kind of corrosion. Ultimately, hydrogen embrittlement decreases the metal’s ductility and load-bearing capacity and causes cracking and catastrophic brittle failures at stress levels below the material’s yield stress.
There are two recognized types of hydrogen embrittlement: internal hydrogen embrittlement and environmental hydrogen embrittlement. Each type of hydrogen embrittlement is caused by different factors. Internal hydrogen embrittlement is the result of hydrogen entering molten metal. The material then becomes supersaturated with hydrogen after it solidifies. Environmental hydrogen embrittlement, on the other hand, occurs when solid metals absorb hydrogen. This can happen:
-
- During high-temperature thermal treatments;
- During electroplating;
- By contact with maintenance chemicals;
- By corrosion reactions;
- By cathodic protection;
- When operating in hydrogen under high pressure.
As the name suggests, hydrogen embrittlement is generally brittle, with intergranular fractures. Currently, the mechanics of hydrogen embrittlement are not completely understood, and detection is difficult.
Example of Hydrogen Embrittlement
In 2013, six months before opening, the east span of the Oakland Bay Bridge failed testing. After just two weeks of use, catastrophic failures were found in shear bolts. This failure was credited to embrittlement, most likely from the environment.
With carbon steel so extensively used in so many industries, it’s vital to know how to protect it. EonCoat is one of a kind coating system that can protect your steel asset.
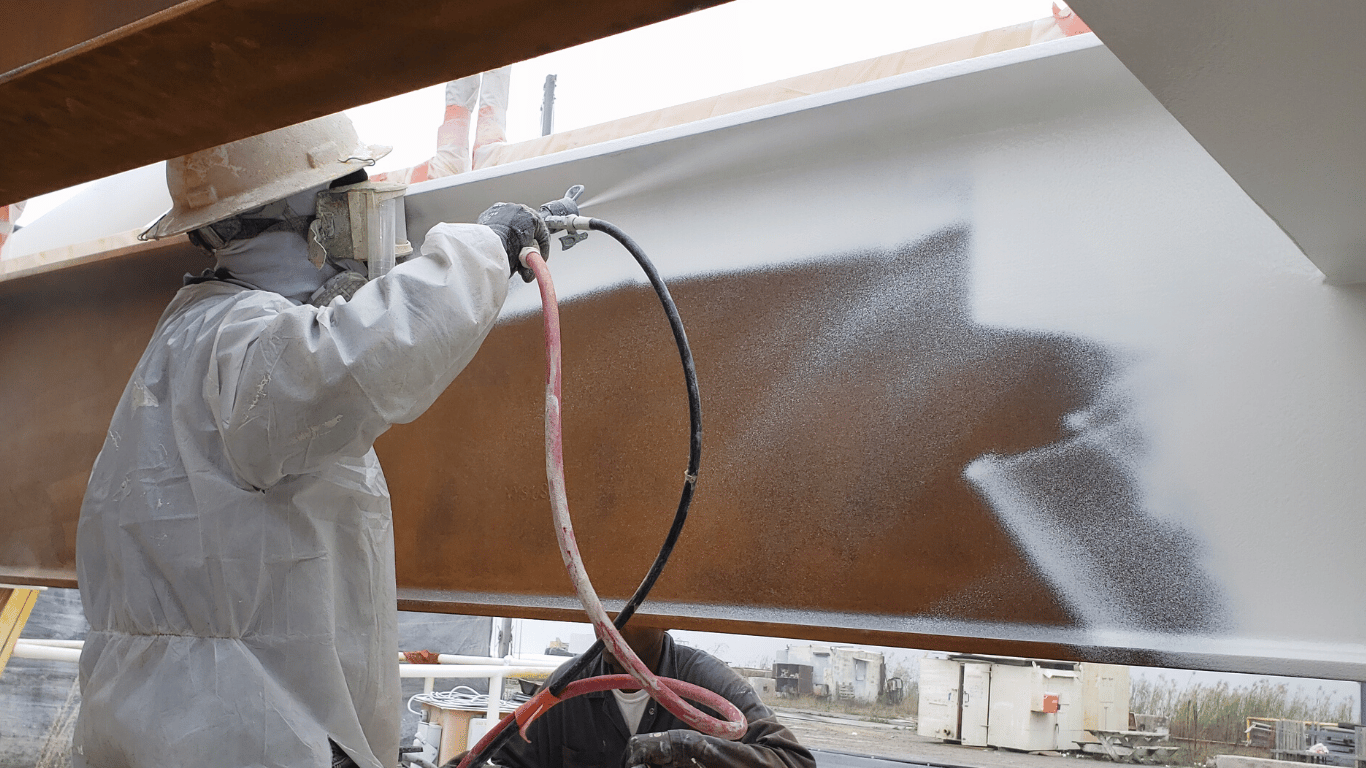
Ready to Learn More About EonCoat?