I Like Questions From New Employees
One of our newer staff members recently asked, “Hey, Carlos, how is it that EonCoat can offer a 30-year warranty, but our competitors don’t offer the same thing?” I thought that was a great question, so we spent some time at the whiteboard mapping out why EonCoat is successful and can offer that one-of-a-kind-in-the-industry warranty. But then, that same staff member said, “You should put all of that information into a blog.” And here we are.
The easiest way of understanding how we got to a 30-year warranty is to walk through the engineering cycle as it applies to EonCoat.
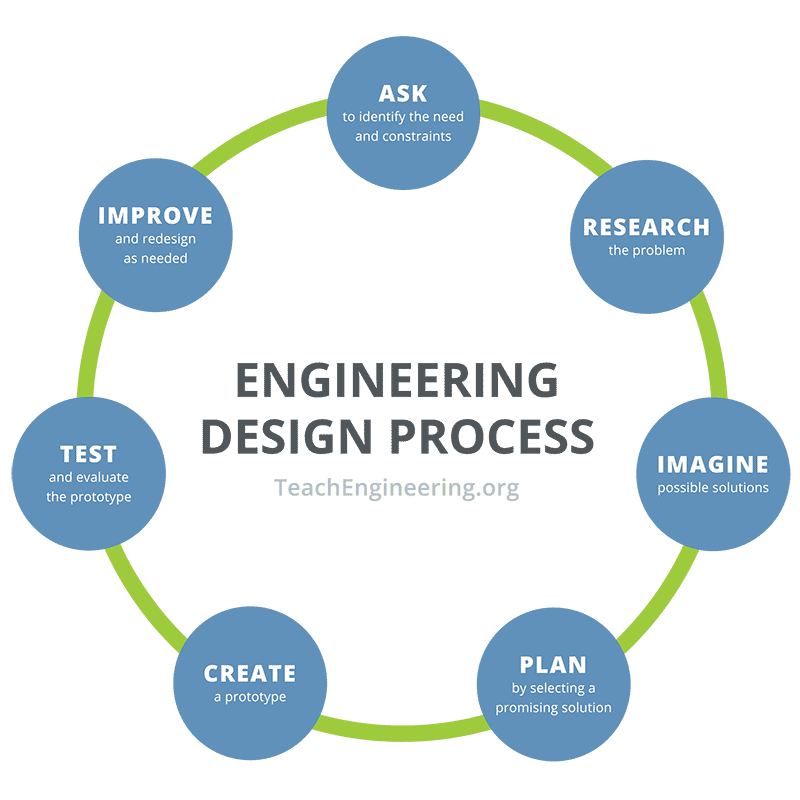
We Ask Questions
ASK: Daily, everyone at EonCoat is constantly asking questions from various points of the Engineering Design Process (like the one in the image above). Tony Collins, our CEO, has intentionally created and fostered this questioning environment. Let me be clear, it’s not that we’re open to questions; we set questioning anything through the engineering cycle as the expectation of our employees.
We constantly engage in this first step of the Engineering Design Process. When a potential customer approaches us, we engage in the first step. We identify the needs of the potential customer. Then, we examine their needs through multiple lenses – engineering, chemistry, atmospheric conditions, etc. We think through and frequently discuss the constraints of a customer’s unique application setting. Sometimes we have to talk about the constraints of EonCoat. More than once, I’ve heard Tony Collins tell someone that the worst thing we could do is sell EonCoat to a customer when what they really need is a different solution.
We continuously ask:
- how we can improve EonCoat’s current products
- what we want EonCoat to be able to do in the future, and
- what we can do to improve applicator and environmental safety.
If you doubt our corporate culture to question everything – and answer every question – follow us on LinkedIn. You’ll commonly see Tony Collins responding to some pointed questions from our community of followers. Also, if you have a question about a social media post, don’t hesitate to engage.
Asking never stops.
We Research
RESEARCH: We never stop in-house research on products we are still developing. We stay engaged in the industry news from around the globe. As you walk through our mixing and chemistry labs, you’ll see any number of research experiments in various stages of development. Tony Collins and Sameer Patel are always engaged in ongoing research. I am constantly researching new ways to reach and teach customers and applicators. Our warehouse team is continuously researching safer and more effective ways to work.
Research never stops.
We Imagine
Imagine: That same corporate culture carries over into daydreaming over lunch and imagining the unlimited possibilities of EonCoat’s current and future products. No one is “hands-off” regarding suggestions and dreams at EonCoat. Can you imagine what our current computer technology might be limited to if Google didn’t encourage the same thing with their “20% time concept”?
Imagining never stops.
We Plan
Plan: We plan relentlessly at EonCoat! Let me say that again, we plan relentlessly. We plan multiple and different research projects that will take anywhere between 30 days and 18+ months. We plan tests for our already-established products as well as our products that are currently in development. Additionally, we plan and design training, meetings, and periods of learning. We even utilize a particular application to manage all of our ongoing project planning and management. This blog is being written in between planning sessions that will guide EonCoat for the remainder of this year.
Planning never stops.
We Create
Create: If you ever stop by our corporate office, you’ll see Sameer Patel’s Wall of Fame. We’ve held on to his prototypes for what did eventually become our family of EonCoat products. The day we realized we had a weldable product was monumental. We’ve created lots – and thrown lots in the trash can because that’s part of the process.
A fair number of our employees are what’s known as kinesthetic processors. It’s not at all uncommon for someone to take a walk during the day so they can create – whether it’s a product or a customer’s solution. Now that we are moving beyond COVID restrictions, we are creating new Certified Applicator Trainings.
Creating never stops.
We Test
Test: We have a commitment – to ourselves and our customers – to both rigorous internal and external third-party testing. We have completed ASTM B117 1500-hour test at Assured Testing. EWI did testing for the Federal Railroad Administration. After 5,000 hours of testing, we had less corrosion our competitors had at 500 hours of testing. We have tested our panels internally for 12,000 hours (500 days). ISO 12944 is considered the toughest test with 25 cycles being the longest test. Passing 25 cycles indicates your product has qualities for splash zone performance. EonCoat tested and passed for 35 cycles.
We submitted our product to testing in some of the harshest environments to allow NASA to test for an environmentally friendly product that provides the best corrosion protection. Our panels were tested along with some of the biggest names in the industry. As a result, EonCoat was the first company to score a perfect 10 in this field-simulating test environment. And by field testing, I do literally mean in a field, along the Florida coastline, facing the Atlantic Ocean.
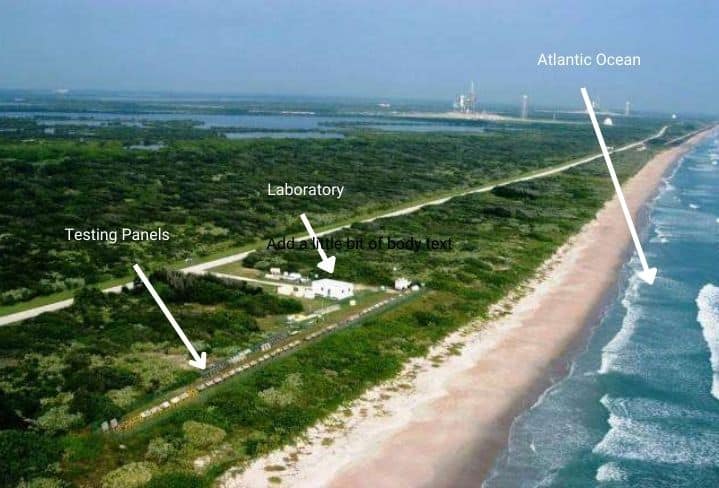
Chevron has also tested our CUI product extensively. Both the Houston Pipe Test and Chevron used tools to attempt to replicate damage to the EonCoat and carbon steel substrates. With damage, even after salt fog chamber testing for 1,870 hours, the alloyed layer did not corrode, and no corrosion spread. EonCoat has also been applied to tanks and pipelines since 2012.
Internal Testing
Because of our drive to cycle through the engineering design process, we asked enough questions to decide to internally test EonCoat on an already rusty piece of carbon steel. You read that right – we applied it right on top of the rust. We didn’t clean or prepare the surface. We then put that EonCoat-protected piece of rust into a salt fog chamber. At 7,000 hours of testing (that’s 291.6 days), we thought we may have pushed EonCoat to the point of failure. If you’re a fan of the engineering process, you realize there’s no failure – only improvement. This led us to revert to the engineering cycle and we decided to continue the test. At approximately 11,000 hours, we realized the panel had healed itself and would succeed!
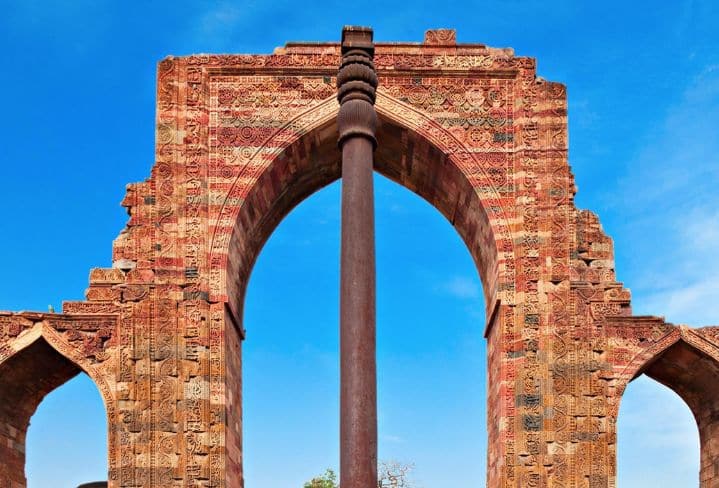
We had that panel dissected when we decided to take that self-driven test to the next level. What was in the middle of the panel was amazing – it was misowite. Misowite is the same product found in the Iron Pillar of Delhi. This pillar has stood without corrosion for 1600 years, and as it turns out, EonCoat mimics that ancient science and artifact.
Testing never stops.
We Improve
Improve: Everyone dreams of big improvements and innovations – including us. However, we are always looking for small improvements, as well. According to James Clear, the author of Atomic Habits, “focusing on one tiny action we can take today to get one step closer to where you want to be tomorrow,” is the way to make improvement a habit. We are constantly looking to improve our products, our testing, our sourcing of raw materials, a shipping option that costs less, and a warehouse process that saves time, just to name a few. The list of small processes and their improvements never stop.
Improving EonCoat never stops.
We Repeat The Process
All of this brings us full circle to the question at the top of this blog. How can we offer a 30-year warranty when our competitors don’t?
- The Iron Pillar of Delhi hasn’t shown any corrosion in 1,600 years with our product mimicking that chemistry
- ISO 12944 for 35 cycles of testing, 10 more than the standard
- EWI for 500 hours of testing and outperforming all of our competition
- NASA and Chevron testing
- A relentless commitment to in-house testing – including a rusted panel that healed itself
- Rigorous third-party testing
- Creating intensive training to become a Certified EonCoat Applicator and requiring a Certified Applicator for the warranty to attach to the completed application
- Constantly revolving and evolving through the Engineering Design Process
If you’d like to learn more about EonCoat’s 30-year warranty or our family of products, feel free to visit our website and sign up for our Free E-book to become more knowledgeable about EonCoat. Do you have questions about how EonCoat can provide permanent corrosion protection? Feel free to reach out to our Customer Success staff, and you’ll typically get a response within a few business hours.
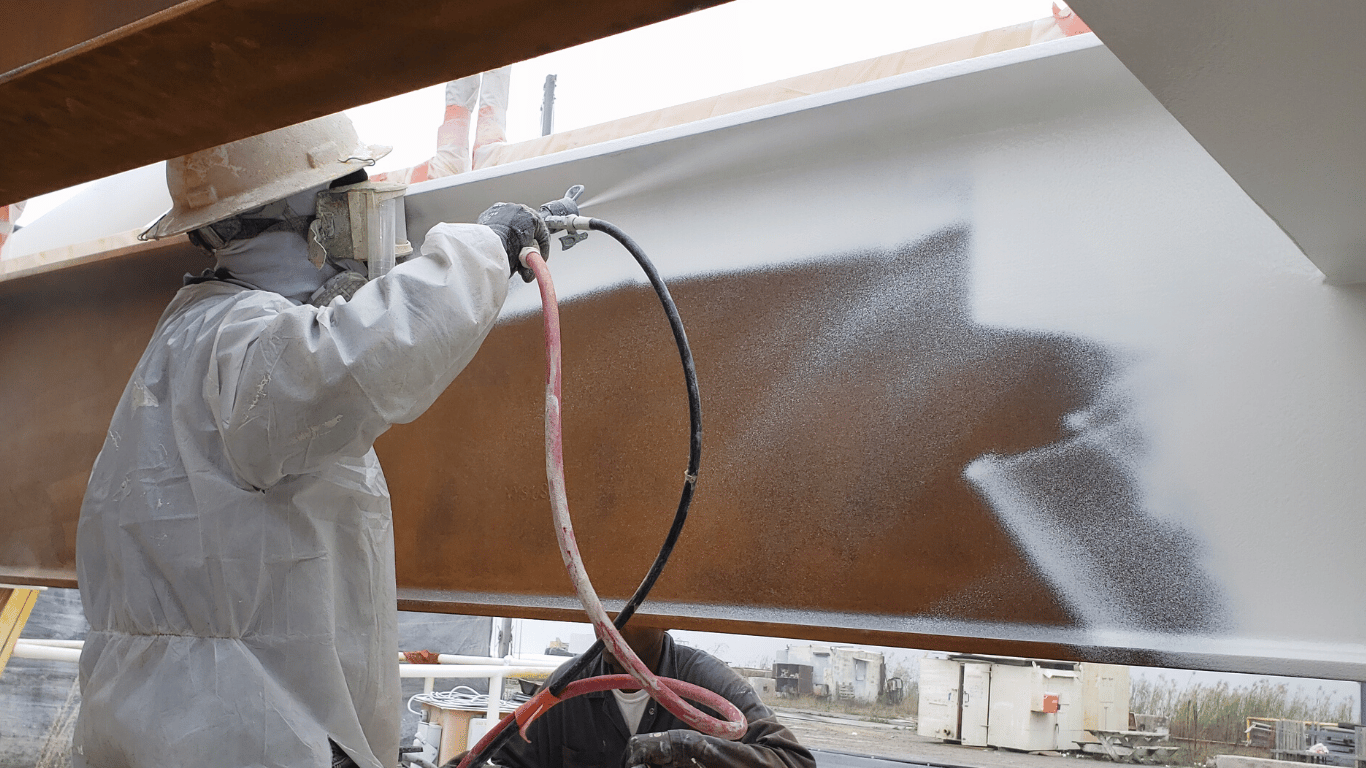
Ready to Learn More About EonCoat?