For many years there have been three primary methods of corrosion protection. Cathodic protection, sacrificial anode, and barrier coat. Now EonCoat offers a fourth method by enabling a passive/alloyed layer chemically bonded to steel that is stable (stable means a metal like gold or platinum that doesn’t generally react with other chemicals).
We’ve had a number of customers ask “Can we topcoat it?” The answer is yes. EonCoat has an inert porous surface with a pH of about 10 so almost all paints bond to it easily without further prep.
We’ve had samples in the seawater spray chamber for nearly a year that have a basecoat of EonCoat and are covered with various topcoats.
As sometimes happens, the most interesting results are unplanned. About 9 months ago one of our lab technicians and application specialist, Mark, put just a brush pass of EonCoat (maybe 2 to 3 mils) on a 3×3 plate with zero prep and sprayed it with a Krylon topcoat out of a can. He then tossed the plate into the seawater chamber curious to see what would happen. After 9 months this sample still looks new except for a couple of spots of organic growth on the surface, which can easily be wiped off by hand. Now if EonCoat can make a $3 can of Krylon last like a world-class protective coating, just think what it could do for a quality barrier coating.
For a long time, the most effective corrosion products have employed a system using multiple coating products that work together and complement each other. For example, it is common to use a sacrificial anode primer covered by a barrier coating. The idea is to use the barrier coating to keep corrosion promoters out but if they get past the barrier the sacrificial primer is consumed before the steel starts to rust. This same strategy could be applied to a combination of a topcoat over EonCoat. EonCoat creates a stable layer that does not react. While this layer should be permanent it is likely that at least a few molecules or ions of any substance will eventually dissolve in water. Adding a topcoat that reduces the amount of water that reaches the EonCoat passive layer would logically further reduce the possibility of ever seeing corrosion.
Additionally, a well-designed topcoat system can also improve performance because EonCoat is a ductile ceramic, but still a ceramic, and with that comes some inherent brittleness. A polymer is exactly the right material to cushion blows and improve the impact resistance of EonCoat in areas where impact is prevalent, like rocks hitting an over the road trailer.
Another Reason to Use EonCoat as a Primer
Over the last year, we’ve run a few tests in the corrosion chamber testing how topcoats work with EonCoat.
We’re learning more each day and what we’ve seen so far has been interesting, encouraging, and perhaps even game-changing in terms of corrosion protection. No matter how hard we’ve tried, the scribe line would not corrode in a severe cyclic corrosion test conducted over 6 months.
We’ve realized this means that with a topcoat, EonCoat will also provide anodic protection in addition to the iron passivation layer to prevent corrosion. We can speculate that potassium ions, which leach from EonCoat, react with corrosive chlorine ions to form potassium chloride, and thus provide anodic protection. Anodic protection is when a sacrificial metal reacts with corrosive ions to prevent reaction with the protected metal, in much the same way that zinc anodes are used to protect the steel components of a ship in saltwater.
This is a significant protection mechanism that we had not expected, and it provides a strong argument for top coating or sealing EonCoat.
We will be experimenting with other ways to take advantage of this mechanism without requiring an additional coat, but until then, using EonCoat as a primer is an excellent option for achieving corrosion protection that far outlasts any product on the market today.
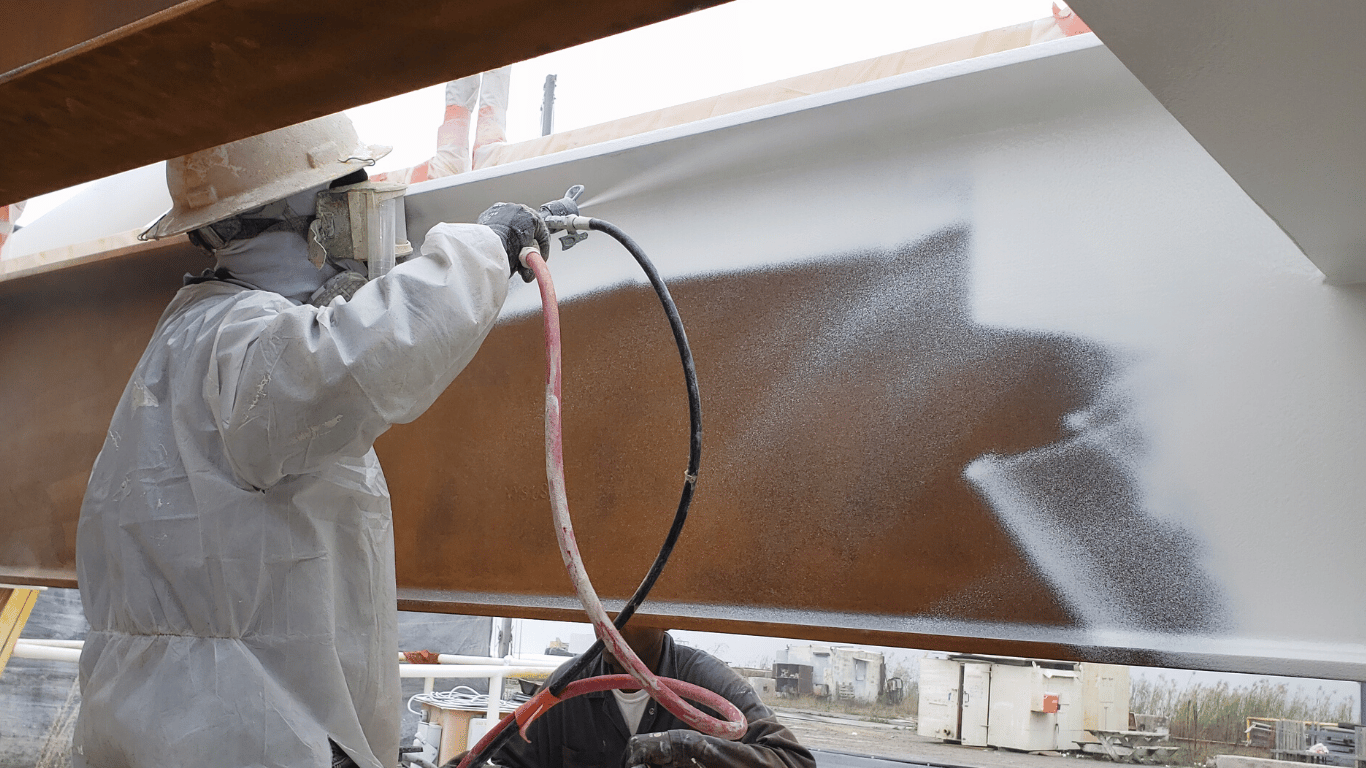
Ready to Learn More About EonCoat?