Corrosion tests show that coatings fail at the point of a scratch. The question is how fast and how far back from the scribe line the corrosion protection breaks down.
In order to understand some things ourselves (and perhaps to make a point), we decided to figure out what happens when the scribe line is really wide. So we tested some EonCoat samples where the ceramic layer was completely removed leaving just bare steel. That essentially makes the entire surface a scribe line, which is as wide as we could get it.
As anyone who has used or tested EonCoat knows, removing the ceramic layer leaves behind an alloyed top layer that continues to protect. It’s the alloyed top layer that EonCoat is famous for.
The Test
Test: Cyclic Sea Water Spray Test of exposed steel after removing EonCoat ceramic layer.
Cycles: The seawater spray test utilizes a 1-hour repetitive cycle that includes:
- A 10 minute period of exposure to seawater that is sprayed onto the surface of the samples
- This followed by a 50 minute drying period.
Drying of samples conducted by three means:
- natural
- air blower
- Sun system2 (SS2-MH-400) UV lamp
Fans and UV lamps turn on automatically at every drying cycle.
This is a replication of the NASA Sea Water Exposure Corrosion Test. (Reference to NASA test can be found here https://corrosion.ksc.nasa.gov/ ). Correlation to real-world conditions – NASA reports that:
- 1 cycle is equivalent to 2 days of “coastal” exposure.
- 24 cycles per day equate to 48 days of coastal exposure per day.
- Each month this chamber would simulate approximately 4 years of real-world service in a seaside town.
Corrosion Chamber
Chamber was made with PVC plastic housing with a seawater spray system, fan, and UV light mounted on top.
The Procedure
- For panel 11811-3 (panel farthest to the right): Ceramic coating was removed about an hour after EonCoat was applied on a mild steel panel. The coating was scraped off with wire a brush.
- For panel 120611 (panel in the center): Ceramic coating was removed by flaking of the ceramic layer. A shiny panel or unblasted panel was used to perform the test.
- For panel 042612-1 (panel farthest to the left): Ceramic coating was removed with abrasive wheels followed by a wire brush.
Panels were then left in the corrosion chambers and exposed to the sea salt spray test (as described above).
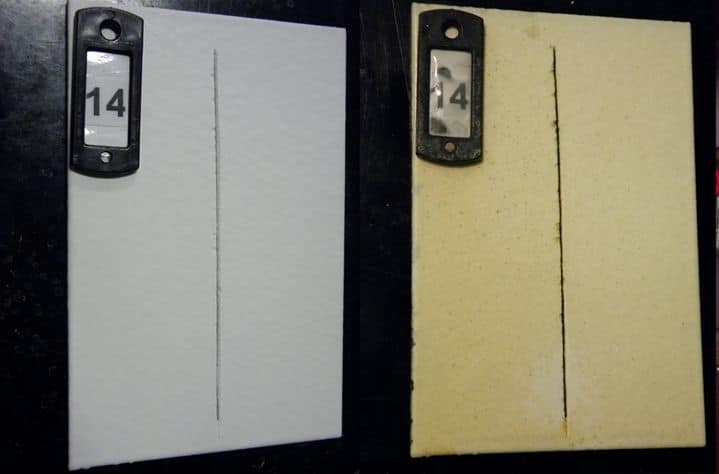
The Results:
Panel 11811-3 was placed in the corrosion chamber on 8th November 2011, with the top ceramic layer removed as described above. This panel was in the corrosion chamber for ~6 months (~4000 hours).
There was no corrosion observed on the panel during the test period.
Center panel 120611, was placed in on 6th December 2011. The top ceramic layer was removed as described above. This panel was in the corrosion chamber for ~5 months (~3500 hours).
There was no corrosion observed on the panel during the test period.
Panel 042612-1, was placed in the corrosion chamber on 26th April 2012. The top ceramic layer was removed before the test as described above. This panel was in a corrosion chamber for ~20 days (~500 hours).
There was no corrosion observed on the panel during the test period.
The Conclusion
There were three panels kept in the corrosion chamber over time and all panels showed no corrosion. This result indicates the presence of a passivation layer on steel (alloying of the surface) and the protection against corrosion is due to this passivation layer. The ceramic layer adds an extra level of protection (especially against abrasion), but the corrosion resistance is uninhibited by the removal of that ceramic layer.
The sample which was in the chamber for 6 months shows what would typically be seen in 24 years of real-world service in a seaside environment. And yet there was no corrosion.
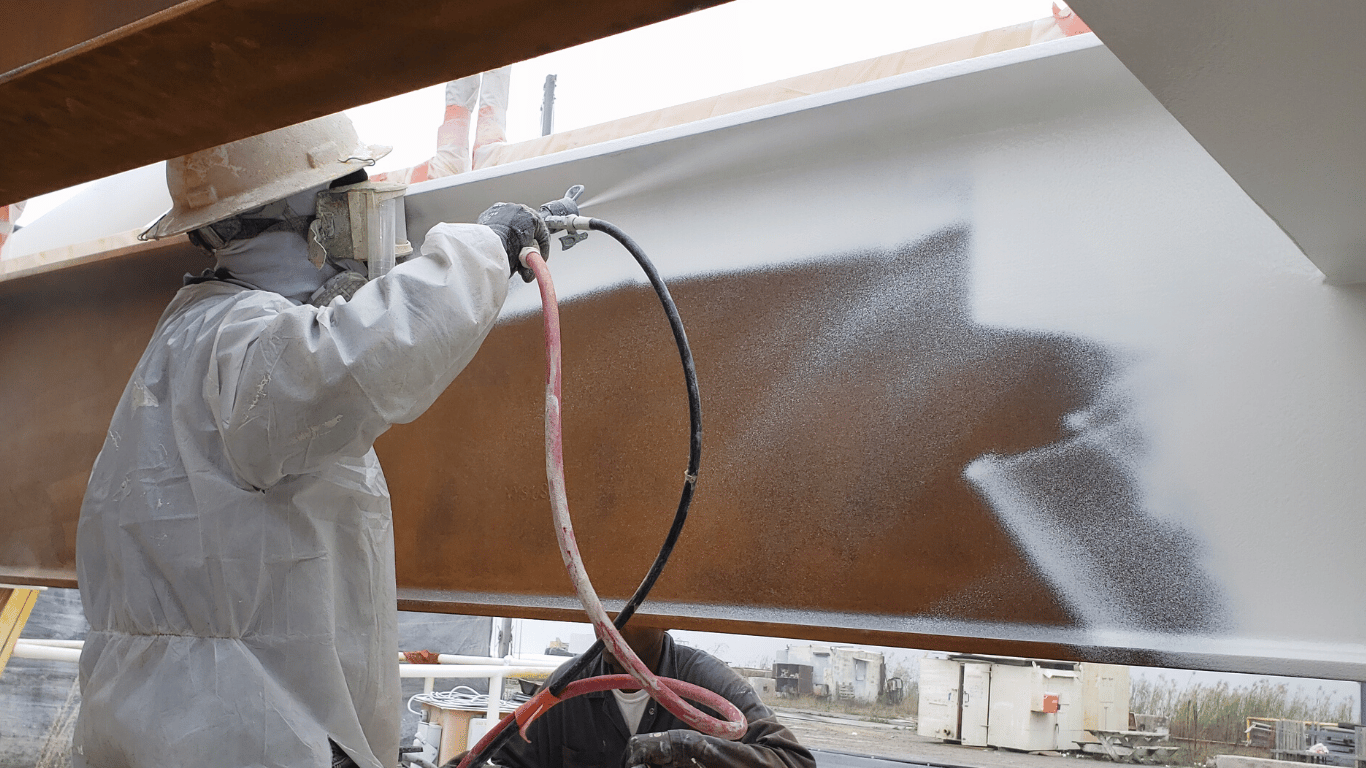
Ready to Learn More About EonCoat?