If you’re familiar with Lean manufacturing or business operations, you’ve probably experienced The 5 Whys of root cause analysis. This is an effective method for identifying the root cause of a problem.
I recently had the opportunity to be the proverbial ‘fly on the wall’ as an organization worked through its unique problem. So, without identifying the customer, I decided to share their journey with you.
As a reminder, the goal of using The 5 Whys is to “prevent the problem from recurring by eliminating its underlying causes.” That aligns nicely with EonCoat’s Mission Statement, “Our reason for being here is to permanently end corrosion safely and with respect for our environment.”
Sometimes it helps to see the process laid out graphically, as below.
Presenting Problem: We have corrosion because of our salt air environment.
The statement ‘we have corrosion’ seems straightforward at first glance. If you have metal, you either already have or will have corrosion. If you’re an asset owner or manager, you know you can’t afford to lose the war against corrosion. So, let’s start at the top of the funnel, “We have corrosion because of our salt air environment.”
Why #1: We have corrosion because carbon steel corrodes.
Yes, the statement above is factually correct. Carbon steel does corrode if you fail to utilize corrosion protection or corrosion prevention. Let’s dig a little deeper.
The current cost of carbon steel is $788 per metric ton in the US. You could argue using Hastelloy at $3,500 per ton USD. Some might even argue for stainless steel, currently priced at $4,720 per ton in the US.
Examine the costs of each of those metals. When you do the math, you quickly arrive at the obvious conclusion. You realize that for the price of a ton of Stainless Steel, you can buy the carbon steel, complete the surface preparation, and apply the EonCoat. After completing the application project, you will still have money left over for your stakeholders or reinvestment in your company.
Why?
Why #2: We have corrosion on carbon steel because we are in a salt-air environment. Salt is conducive to corrosion.
Salt air is corrosive because it’s hygroscopic – it attracts water. The salt attracts moisture from the environment to the carbon steel substrate, which speeds up the oxidation (rusting) process. Salt is in the environment, which means the effects of salt can be found on the surface of your carbon steel asset.
While you may think this salt air corrosion is a problem for salt water coastal communities, think again. Salty air has been found 900 miles inland. Defining a salt air environment as something that pertains to offshore structures is no longer relevant. One researcher detected sea spray in Boulder, Colorado. This data leads us to suggest that we must re-think the definition of “salt air” to “air.”
Additionally, some industries and companies simply can’t choose where to do business. For example, the Sabine Pass LNG plant was built where natural gas is easily obtained. Therefore the facility sits “less than four nautical miles from the Gulf of Mexico.” It would make no sense to move that plant further inland.
In addition, approximately one-half of the world’s population lives in coastal regions. These numbers are related to how humanity spread and transportation developed throughout human history. Therefore, a significant portion of industry also occurs near coastal regions.
In addition to naturally occurring salt air, you must account for salt mines and other product-related processes involving salt. Just in the United States, 26 companies operate 63 salt plants in 16 states. Of the top seven producing states, only three have a coastline; and the others are inland states. Salt is everywhere.
Why?
Why #3: We can’t control the salt air environment, so our carbon steel assets are not adequately protected.
Once again, the why is an accurate statement. You can’t control the air. We also can’t control the naturally occurring salts that speed up corrosion.
There are tools to measure the amount of salt on a carbon steel substrate after surface preparation has occurred. The tools are necessary because many protective coatings have a narrow tolerance for salt on carbon steel. This is when some protective coatings will tell you must “hold the blast.”
While holding the blast keeps the surface from oxidizing, it adds excessive time and cost to any application project. Preventing salt from reaching the substrate is costly. You may even find osmotic blistering because of the inability to maintain a low salt level before applying your protective coating.
Why?
Why #4: We picked what we thought was the best coating (option) at the time.
This why has less to do with data or science and more with human behavior. We tend to fall back to “we’ve always done it this way” instead of exploring newer technologies that can serve us better. In other instances, instead of returning to a prior way of providing corrosion protection, we return to the consultant relationship that sold us less-than-the-best corrosion protection. This can happen without fully exploring technologies, options, or the consultant’s financial incentive to recommend a particular corrosion-resistant coating.
Why?
Why #5: We didn’t know about EonCoat or understand its science.
Now you know about EonCoat, so let’s break down the science and relate the science to the five why’s. Now that we’ve identified the Five Whys let’s talk about the countermeasure for each why.
Countermeasures to salt air.
Why #1: Carbon steel corrodes:
Corrosion occurs because a carbon steel atom loses an electron and bonds with oxygen to restore the charge imbalance. If sufficient phosphate is present, the iron will choose to bond with the phosphate instead of the oxygen, thus preventing the corrosion from ever starting. EonCoat lays down a layer of phosphate next to the carbon steel and chemically bonds to the steel. Iron Phosphate never gives up its electrons.
With EonCoat, the naturally occurring process that causes corrosion actually causes EonCoat to prevent corrosion successfully. The two layers are why EonCoat can offer their customers a 30-year warranty.
Why #2: Salt is conducive to corrosion.
EonCoat has salt in it. Yes, you read that correctly.
You can apply EonCoat, which has salt as part of its patented formula, to a carbon steel substrate. Even when (not if, but when) the substrate has salt on it – in a salt air environment – you won’t get corrosion. Instead, you’ll get permanent corrosion protection. So, whether you’re 900 miles inland or at the coastline of the Atlantic Ocean, like NASA, a salty environment is where EonCoat shines.
Why #3: We can’t control the salt air environment.
With EonCoat, you don’t have to control the environment, and you won’t have to hold the blast. You don’t even have to stop an application project because of rain. Once you have accomplished the SSPC-SP6 / NACE 3 / SA 2 surface preparation, you can apply EonCoat. It really is that straightforward.
Why #4: You thought you picked the appropriate corrosion prevention method.
That’s okay. We’re all human. Are you unsure how to approach EonCoat with questions about your corrosion or anticipated corrosion prevention application? At EonCoat, permanent corrosion protection starts with a conversation and grows into a relationship.
If EonCoat is not the correct solution to your corrosion problem, we’ll be upfront and tell you. When I started here at EonCoat, Tony Collins’ wise advice was, “the worst sale we could ever make is one that doesn’t meet the customers’ needs.” We continue to tell that to potential customers, many of whom are left speechless by that practice.
Why #5: You didn’t know about EonCoat.
Now you know about EonCoat. Additionally, you have a better understanding of the straightforward science that makes all three of our corrosion protection systems so effective. You can now develop into the hero that guides your organization toward permanent corrosion protection.
If you’re ready to learn more about Eoncoat, the industries it serves, and more, click the button below. You’ll be able to download our Free E-Book. Additionally, you’ll receive one email per day for five days and be on your journey toward permanent corrosion protection.
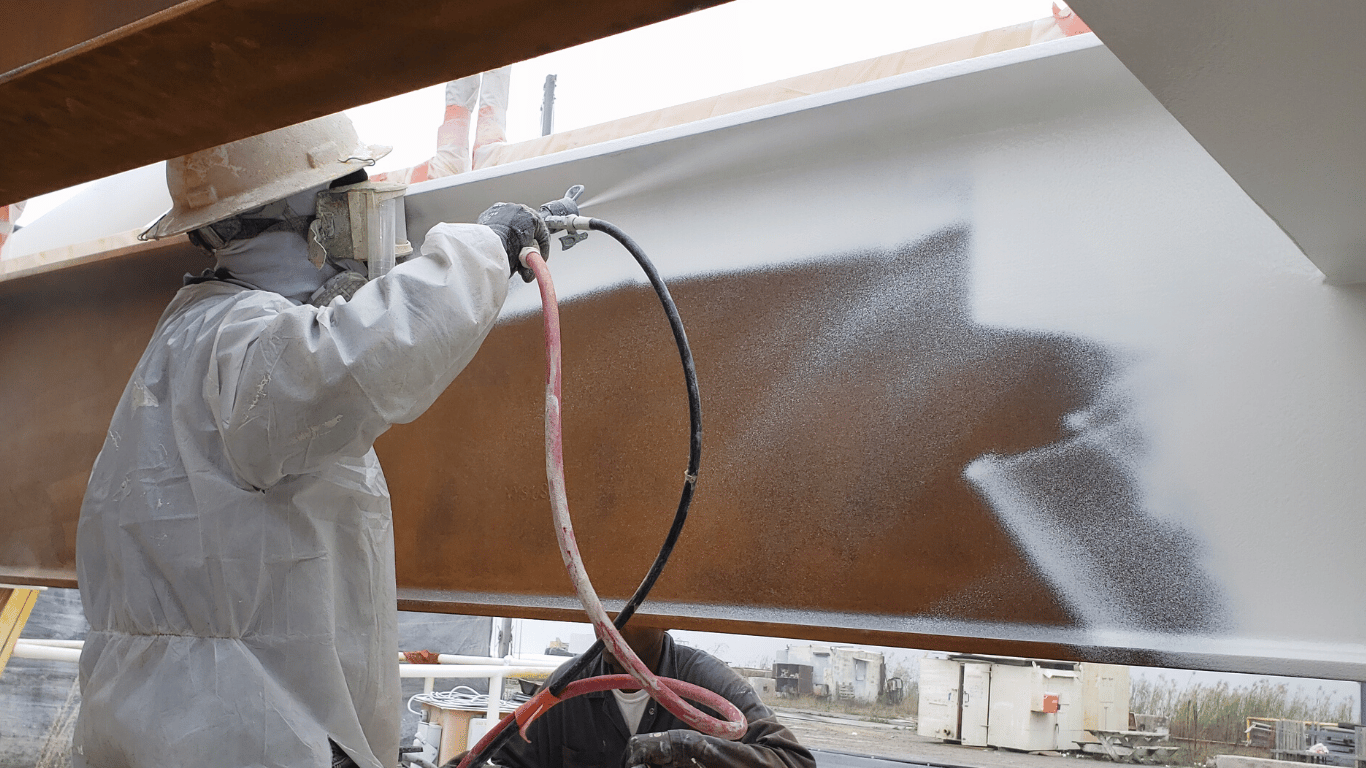
Ready to Learn More About EonCoat?