What Is CUI?
Corrosion Under Insulation (CUI) is localized, external corrosion that occurs on carbon steel (and stainless steel) that has been insulated. It is – literally – the corrosion that occurs between the carbon steel and the insulation material. The typical purpose of the insulation is to keep a hot asset from transferring heat.
The side effect of the insulation is that it provides space between the high temperatures of an asset and the environment. In that space, oxygen and trapped moisture can meet and cause corrosion.
The High Costs of CUI
While that is a simple explanation, the costs of CUI are anything but simple. The estimated cost of corrosion is $2.2 trillion worldwide each year, which is 3% of the world’s GDP. The estimated cost of CUI is 40% – 60% of pipe maintenance costs. Now that we’re all on the same page with the costs of CUI, let’s dig a little deeper into the detection and prevention of CUI.
The Temperature of CUI
Insulation is typically installed when the exterior carbon steel exceeds a high temperature of 50°C. This temperature-rated standard is intended to prevent both work-related injuries and heat loss. CUI is prevalent in carbon steel when the temperature range is between -4°C (24.8°F) and 175°C (347°F). The highest risk of CUI occurs between 77°C (140°F) and 110°C (248°F).
Figure 1 Extracted from (Armacell)
Environmental Factors in CUI
Now let’s look at the environmental factors that contribute to higher rates of CUI:
- Hot or humid environments
- Marine environments
- Steam tracing leaks
- Climates with higher rainfall
- Contaminants from the insulation or the atmosphere (such as chlorides and sulfides) dissolving in water
- Systems that operate below atmospheric dew point
- Intermittent wet-dry conditions
- Insulation systems that don’t allow moisture damage
- Insulating materials that hold moisture
Between the temperatures and the environmental conditions, it’s easy to see how most, if not any, CUI projects can be susceptible to corrosion. This easily explains why all industries impacted must be vigilant in monitoring and aggressive in both preventing CUI and stopping CUI when it has been detected.
The tricky part is that the heated carbon steel assets, including storage tanks, pipelines, and other structures, typically carry some of the most essential components of the oil, gas, petrochemical industries, and other process facilities. Speaking practically, this means essential assets may require being removed from service so they can be inspected for signs of CUI.
How Do You Detect CUI?
The first, and most obvious way, to inspect for CUI is also the most destructive – you remove the insulation. If you’re in an older facility and the insulation involves asbestos, then you have the added expense of asbestos abatement. Even without asbestos, if this method was only conducted for areas that are prone to CUI, this involves the significant costs of removing the insulation, engaging in the inspection process, and reapplying the coverings.
Nondestructive methods for detecting CUI include:
- Visual Inspection
- X-rays or Radiography
- Real-Time Radiography
- Computed Radiography
- Digital Detector Array
- Ultrasonic Thickness Measurement
- Pulsed Eddy Current
CUI is about more than money
If you’re starting to think that the focus on CUI is about the money, please don’t misunderstand one of the most important points. Where there is high-temperature carbon steel and assets potentially under pressure, there will be people. We commend the folks at Dow, who published their own internal review after a near-miss incident involving CUI. In March of 2008, Dow’s LHC plant had an 8-inch carbon steel hydrocarbon line failure.
The report details, “The event began with a small pinhole leak, detected by operators. While the operators were isolating and de-pressuring the line, it failed catastrophically. Fortunately, this catastrophic line failure produced such explosive force that the line bent in two locations – essentially sealing itself and avoiding a major release.”
The substance in that particular line was 40% ethylene. If you’re unfamiliar with ethylene, it is highly flammable, reactive, and an explosion hazard.
Fig.1, Fig.2, Fig.3 (Wermac.org)
Is there a cure for CUI?
The high temperatures that require insulation eliminate a certain amount of protective options and present a unique challenge to protective coatings. Three options are TSA, three-coat systems, or EonCoat’s CUI / High-Temperature Coating. Keep reading to see the comparisons.
Some folks might recommend thermal-sprayed aluminum (TSA) as one option to prevent CUI. As we’ve discussed in a prior blog, EonCoat is 15x less expensive than TSA and is 12x faster to apply than TSA.
Your benefit from all of those cost savings occurs before we even get to the toxic risks associated with TSA.
(Laboratory Results For : EonCoat Product Testing)
Still, other people might recommend a standard, three-coat paint system to go between the carbon steel and the insulation material. One of the downsides to the three-coat system is that the paint must be rolled on instead of spray applied. Rolling on anything – but specifically rolling on three distinct coats – is an exercise in wasting time. Unless you’re the person being paid to roll on the three layers of paint – then a three-coat roll-on job is fabulous!
EonCoat’s CUI / High-Temperature Rating product is a two-part system that only requires one application. The two parts meet during the spray application and immediately form an alloy layer when they reach the carbon steel substrate. This chemical reaction is what sets EonCoat apart from the other systems. Other systems mechanically lay on top of the carbon steel until something interferes with the mechanical connection – in the case of CUI – moisture.
Additionally, most protective three-coat paint systems require the surface preparation standard of Near White/SSPC SP10 / NACE No 2 / ISO 2 ½ standard. When you compare the Near White standard to the Commercial SSPC SP6 / NACE No 3 / ISA SA 2 required by EonCoat’s CUI High-Temperature Coating, EonCoat has saved you money before you’ve even started the application.
At the end of the application, EonCoat is dry to touch in 5 minutes and cured in 15 minutes. When that rapid cure time is combined with the knowledge that EonCoat doesn’t require a topcoat before the insulation is reapplied, you’ve just saved even more money. Your carbon steel asset can be returned to service as soon as the insulation is in place!
Has EonCoat’s CUI / High-Temperature Coating Been Tested?
After extensive testing of EonCoat, Chevron U.S.A. found that EonCoat CUI will successfully “prevent atmospheric corrosion” and “prevent corrosion under insulation.” The same report details some of the extensive, third-party testing that EonCoat has accomplished, one of which is the ASTM B1117 test. You can see the benefits of EonCoat in the graphic below:
If you’re ready to learn more about EonCoat’s CUI / High-Temperature Coating, or the other EonCoat family of corrosion protection products, sign up for our FREE EonCoat E-Book. You’ll get just one email per day for five days and learn more about the science and technology behind EonCoat’s success.
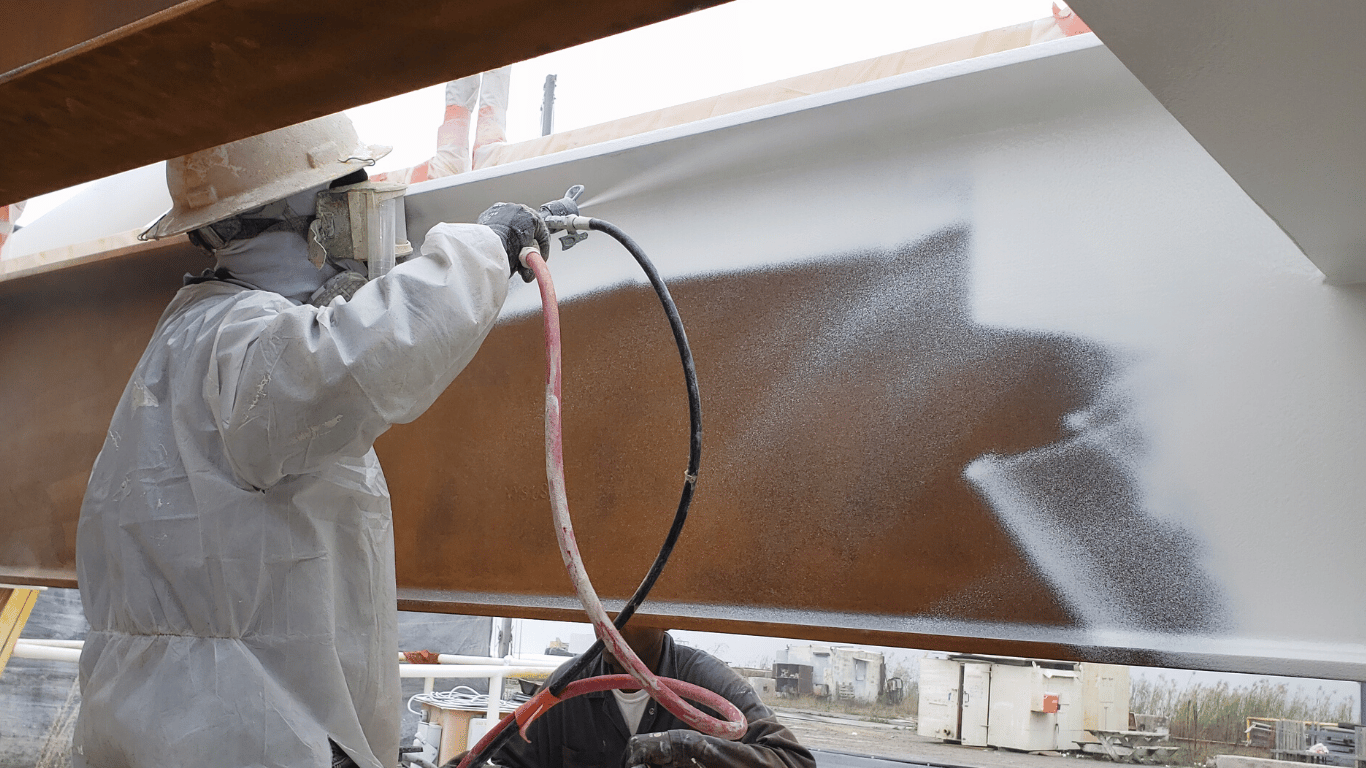
Ready to Learn More About EonCoat?