High-Pressure Plural Pumps Are For Applying EonCoat to Large Carbon Steel Assets
We’ve already answered your Surface Preparation questions and your Dual Component Spray Gun questions. Now it’s time to answer your top three High-Pressure Plural Pump Questions. This high-volume application method is effective for jobs such as storage tanks, pipelines, structural steel, offshore platforms, and early in the manufacturing process for certain fabrications. That list is not exhaustive because potential customers are constantly approaching us with all sorts of new application scenarios.
FAQ #1: Do the lowers and the mix manifold have to be stainless steel?
Yes, both the lowers and the mix manifold must be stainless steel. Let’s start by clearly defining these two very different metals. Stainless Steel is a generic term for corrosion-resistant alloys containing 10.5% chromium by mass. By comparison, the definition of Carbon Steel is an alloy of iron and carbon. Carbon steel has a higher carbon content, lower melting point, and greater durability than stainless steel.
The Chemistry Behind The Answer
To understand why you must use Stainless Steel lowers and mix manifolds, you need to understand a little of the chemistry behind EonCoat. Part A is acid, and Part B is a base. Do you see what we did there? We made it easy to keep straight. However, even as independent components containing a high level of phosphates, they will cause corrosion.
The mix manifold must also be stainless steel because that is where the EonCoat magic (also known as a chemical reaction) starts to occur. If the mix manifold isn’t stainless steel, it will clog within minutes. You can watch this video we created to see and understand just how quickly the two parts of EonCoat react when they meet.
Recommended Equipment
We consistently recommend two specific high-pressure plural pumps – listed here in no particular order. First, the Cosmostar SD100-X30 – where you can request the stainless-steel lower pump material. Next, is the Graco XP35-SST 1:1 Plural Spray Machine that will automatically come with stainless steel lowers.
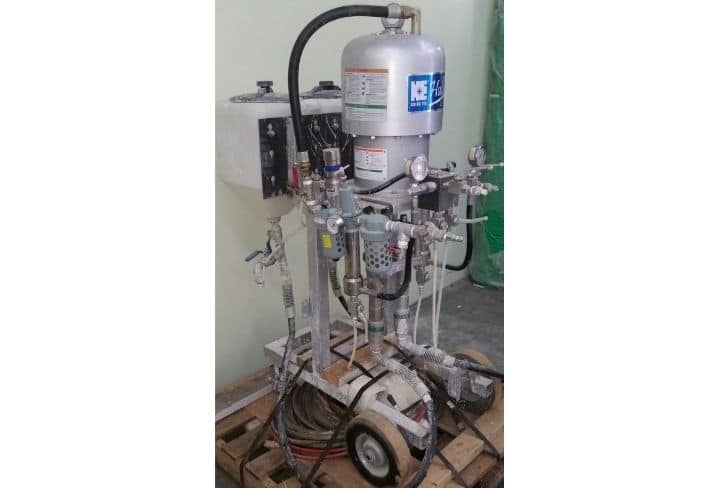
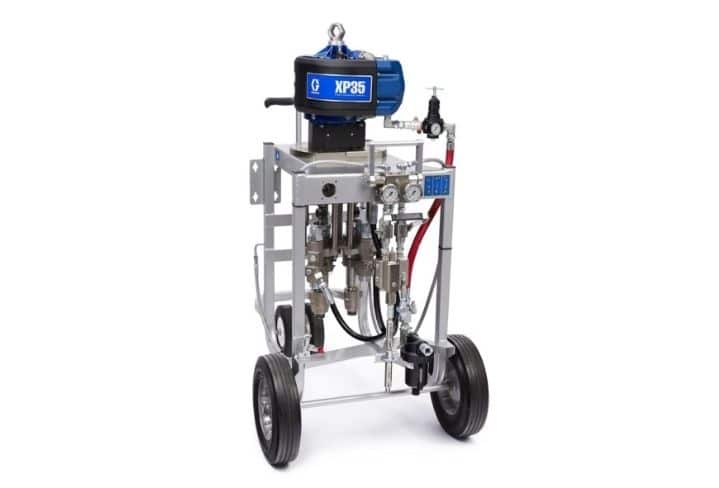
Keep in mind that we recommend stainless steel 304/316 for any equipment parts that come into contact with Part A. Do not use any equipment coated with lead, zinc, or other reactive material in the supply path for Part A.
FAQ # 2 – What is the typical coverage expectation?
The typical coverage comes with a range because life comes with a range. Let’s start with loss factor. The loss factor is the difference between the theoretical and practical spreading rates expressed as a percentage of the theoretical spreading rate. Because EonCoat is a single application, mathematically, the loss factor will be the same percentage for EonCoat as it is a 3-application product. However, because EonCoat only requires 1 application, there is less volume loss. Let’s look at the details that impact the range of applications.
Our goal in recommending that you estimate a 30% loss factor is to help you reach the end of your application job and have everyone say, ‘that was a smooth application project.’ If you underestimate your loss factor and consequently have too little product, you will end up stopping the application job because you run out of product. While you can always order more EonCoat, we don’t make any product until your order is complete because of our high manufacturing standards to provide you with maximum shelf life. In conjunction with our high manufacturing standards, the practice of under-estimating the amount of EonCoat could produce an unwanted and unnecessary delay.
The Math of EonCoat
We like for the customer to understand the process of determining the amount of EonCoat they need to order! That’s why we’ve created and constantly share some of our favorite calculators. We have a Tank and Structure Calculator to help you determine the surface area of your carbon steel asset that needs to be treated and protected by EonCoat. Based on your outcome after using the Tank and Structure calculator, we have a Surface Area Calculator for both square feet and square meters. Now you know how much EonCoat you’ll need to order. If you have any questions about your specific application, feel free to reach out to us.
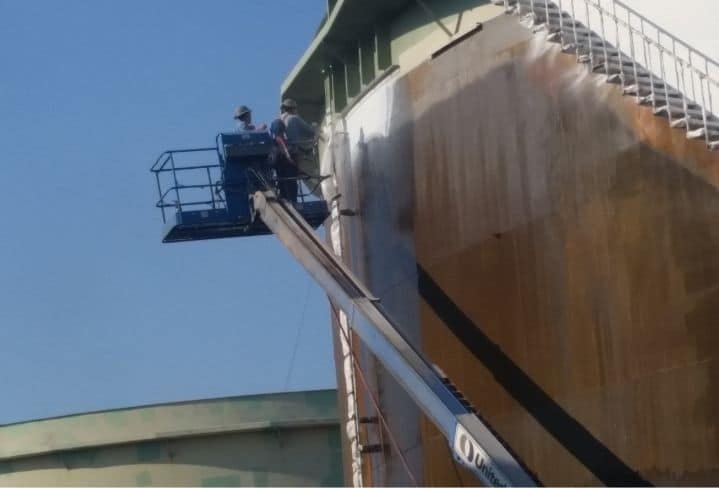
We Can’t Control The Weather
The factor none of us can control is the weather. A windy day will have a higher loss factor rate than a day without wind. The best way to control how the wind drives your dry fall and loss factor rate is to either spray on a windless day or erect a temporary, upright barrier – such as a tarp – to reduce the wind flow. Any day we see the flags on a pole fully extended, we know that any application occurring that day will have a higher loss factor. If your company is flying a flag, that’s an easy gauge for wind flow. Based on this, you would want to see that your flag is barely moving – that’s an ideal application environment.
The Applicator Matters
The experience of the applicator is another factor in the loss factor. When we train new applicators, we can see a significant loss factor at the initial stages of training. However, as the training progresses with each hands-on experience, the application of EonCoat becomes closer to the required minimum thickness earlier in the spray application process.
Shape, Size, and Small Details Matter
Yet another consideration for the loss factor is the size and shape of your substrate. A larger substrate with a flatter surface will have less loss. It’s easier to apply EonCoat on that type of surface because you can get the EonCoat where it’s supposed to go and keep moving. A smaller pipeline (think a few inches in diameter) will have a higher loss factor by the simple laws of nature and physics.
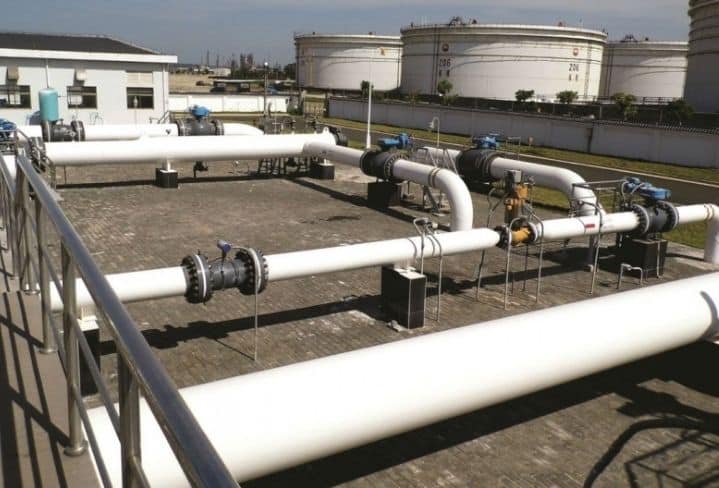
FAQ # 3 – What solvents do I need to clean the equipment?
It’s simple – you just need water. Part of our dedication to being applicator- and environmentally-friendly is removing unnecessary solvents and chemicals from the application and clean-up process.
We realize that as humans, everyone takes breaks and eats meals – so here’s how you take care of your equipment. If you stop spraying for more than 30 seconds, you must purge the spray gun with water. This is why part of our training standard is to train applicators in teams. If you have two applicators working the pump together, you can keep the application process moving.
If you must stop the application process for 8 hours or less, you can leave the material in the hoses and pumps without pressure. You would need to release the pressure from the pump, gun, and hoses. This practice will prevent the possibility of crossover at the mix manifold.
To maintain your equipment long-term, at the end of each day, run water through the parts and the machine until the water runs clear. For example, to clean the hoses that deliver the EonCoat, flush them thoroughly until the water runs clear. At a minimum of once per week, all the displacement pumps should be taken apart and thoroughly cleaned.
Do You Have Questions About High-Pressure Plural Pumps or EonCoat?
If you have questions about applying EonCoat’s permanent corrosion protection to your carbon steel, feel free to reach out to us. You can visit us at our Contact Us page or call us at 754-222-4919, Monday through Friday between 9:00 AM and 5:00 PM. If you prefer to receive written material about EonCoat, sign up for our Free E-book. When you sign up for our E-book, you receive only one email daily for 5 days.
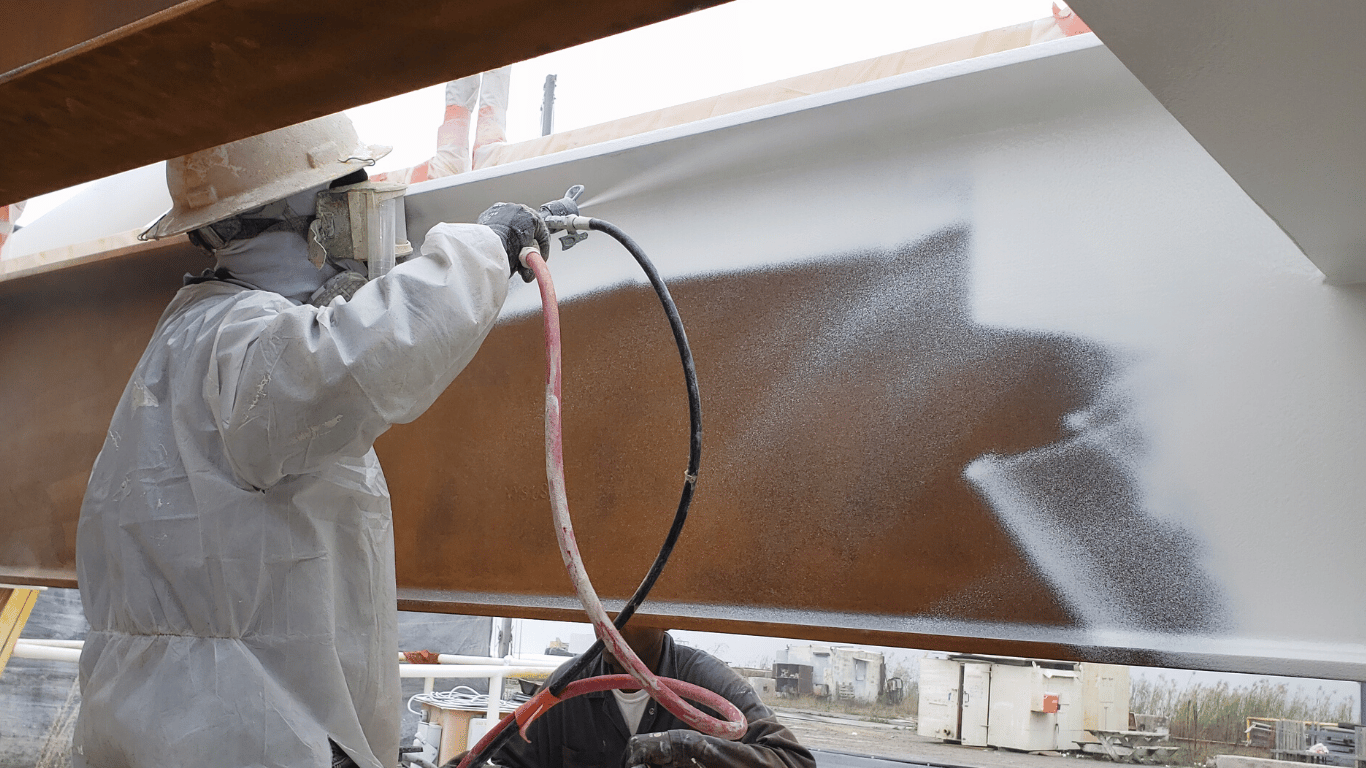
Ready to Learn More About EonCoat?