It’s not an overstatement to call rust the scourge of the industrial sector. The government estimates the direct cost of Corrosion to the U.S. economy is 3.1% of GDP. That’s $697 billion each year and disrupts everything from production to logistics. If you figure in the indirect costs which are even larger the bill is well over a Trillion dollars in 2021. Industries that rely on carbon steel assets know they need to manage rust, but it’s hard to control something that spreads so quickly and consequentially.
In many cases, it’s difficult to even apply a protective coating to an asset because flash rust occurs quickly after blasting and undermines the success of traditional coatings that are meant to prevent this very rust. When flash rust isn’t addressed during the application of a traditional coating, it can contribute to coating failure and leave your assets vulnerable to more severe corrosion.
As with most things, prevention is the best medicine.
This quick guide outlines everything you need to know to stay ahead of flash rust.
STEP ONE: IDENTIFY FLASH RUST
Flash rust has the characteristic copper color of rust along with an even, powdery surface. This makes it relatively easy to identify your carbon steel assets by sight alone.
Flash rust typically appears after dry blasting or wet cleaning methods. Rust can appear within minutes or hours after the cleaning and rapidly spread from a small patch to the entire surface.
STEP TWO: REMOVE FLASH RUST
There is no quick or easy way to remove flash rust. It must be re-blasted when it happens.
It’s a time-consuming and labor-intensive job.
And removing flash rust by re-blasting also means removing more metal.
When using traditional coatings, ignoring flash rust is not an option, but re-blasting is not a perfect solution either..
STEP THREE: PREVENT FLASH RUST
There are products in the market that claim to delay flash rust. These are predominantly citric acid and create iron citrate – this is still corrosion. The difference is that iron citrate is clear so you don’t see it.
Even if you coat properly before the surface “turns” or “flashes”, whether you apply zinc, epoxy, or polyurethane, these traditional coatings age and degrade with time, sunlight, and temperature. These coating options are a short-term solution — but there is a way to protect your assets for the long term.
EONCOAT HANDLES FLASH RUST IN A DIFFERENT WAY
EonCoat is revolutionizing the world of corrosion prevention and solving the problem of flash rust on carbon steel assets for good.
Unlike other coatings that sit on top of the material surface, EonCoat chemically bonds to the surface, creating an impenetrable corrosion barrier of alloyed steel. EonCoat’s proprietary dual-layer formula — consisting of an alloy layer and a protective ceramic layer — make it irrelevant if oxygen or moisture is present. The alloy layer is inert. EonCoat® has proven itself in industries such as oil and gas, where corrosion is a relentless enemy of carbon steel assets.
Even better, with EonCoat, you don’t have to remove existing tightly bonded rust from your assets. EonCoat® can be applied directly over flash rust after a commercial blast. You do need to remove the old paint and any mill scale. EonCoat uses flash rust to help build the alloy layer.
With ordinary coatings, there is no such thing as a minor outbreak of corrosion. After it appears in one place on your asset, it’s guaranteed to spread. EonCoat® changes this paradigm. It will stop rust even if starts due to an application error or physical damage to the alloy layer.
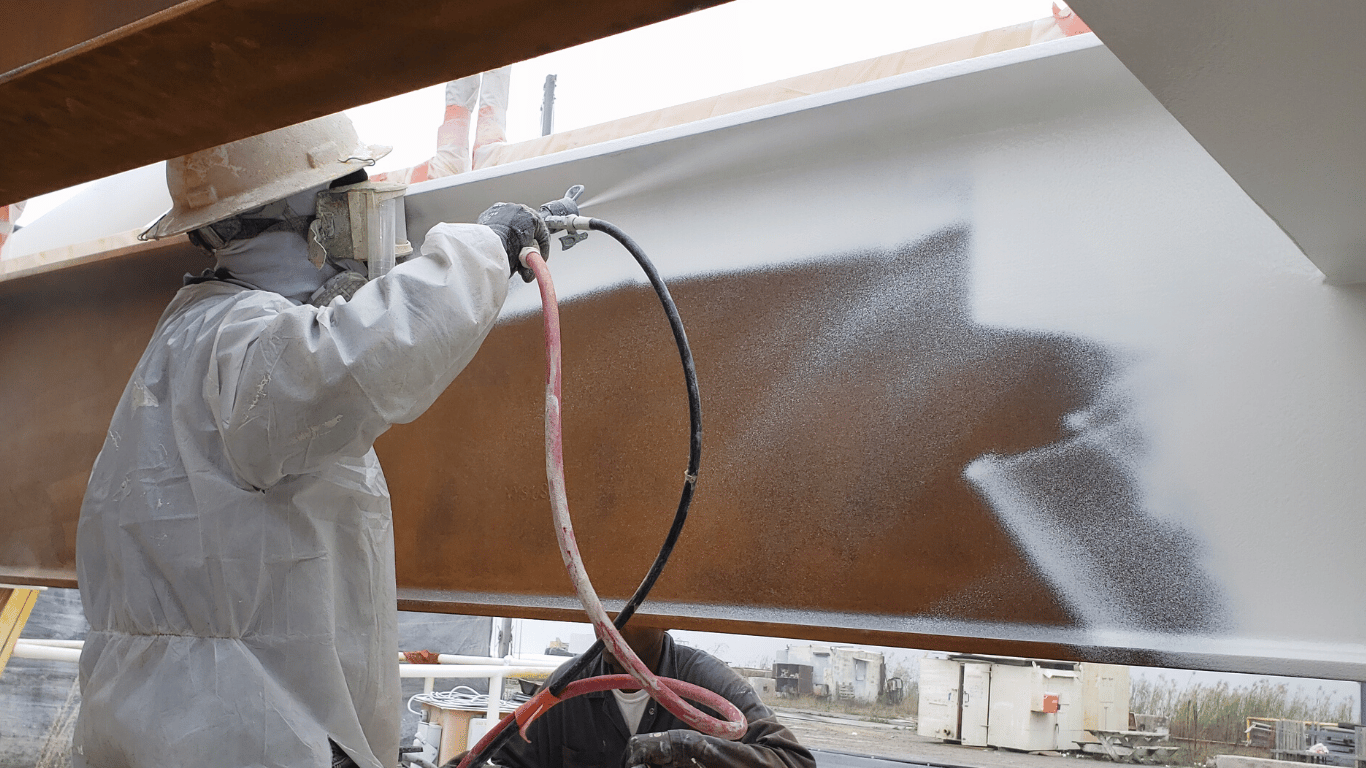
Ready to Learn More About EonCoat?