Monitoring for corrosion is extremely important for steel assets because if it goes unnoticed, corrosion can lead to costly and dangerous issues — including leaks, equipment failures, or even injury.
Despite its importance, corrosion monitoring has been a challenge in the industry as carbon steel assets stretch for miles and miles, often without enough inspectors to go around. While the government is responsible for oversight, they’re severely understaffed: as of late 2017, there are only 208 federal inspectors and 345 state inspectors. For every one inspector, there are almost five thousand miles of pipeline to review.
Corrosion is one of the costliest issues faced by oil & gas companies. According to estimates by NACE International, corrosion costs the industry over $1.3 billion annually. In response, companies are taking the task of monitoring into their own hands. Corrosion monitoring is undergoing a revolution. New technology is enabling companies to better monitor their pipelines and stay on top of potential corrosion issues. In this post, we’ll cover a few advancements that are helping companies improve corrosion management.
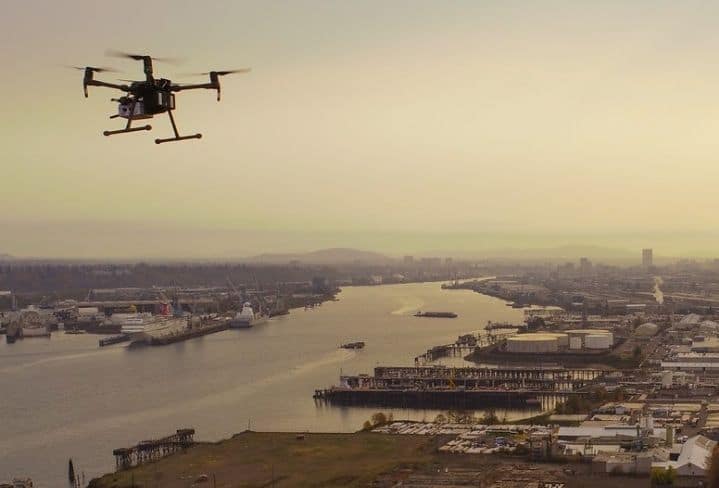
1. Drones
Drones have become valuable tools for companies to monitor their assets. The oil & gas industry, in particular, is turning to drone use as a strategy to reduce costs associated with corrosion monitoring. Currently, pipeline inspections are done by helicopter or by foot — both of which are expensive and time-consuming methods. Monitoring via drones is possible due to developing sensory technology that can fit onto a drone. These sensors would be sensitive enough to detect changes in pipeline conditions.
The use of drones to monitor pipelines can eliminate the risks of having inspectors and workers visiting pipelines in hazardous areas to check them manually.
2. Sensors and Probes
While drones may not yet be widespread corrosion monitoring tools, sensors themselves are already being put to use. General Electric, for instance, developed its Predictive Corrosion Management app using RightTrax PM digital sensors to monitor the thickness of pipeline walls. This real-time system allows companies to identify vulnerable areas of their pipeline systems without manual inspections.
Industrial company Teledyne Common uses electrical resistance probes to monitor wall thickness through ultrasound. Similar to sensors, these probes detect in real-time changes in wall thickness that can indicate corrosion problems.
3. EonCoat®
Of course, preventing corrosion in the first place can eliminate most associated costs of monitoring for corrosion. EonCoat’s patented dual-layer coating is designed to do just this. When applied to the surface of your steel assets, EonCoat® reacts with the steel to form an iron phosphate alloy layer. Next, a phosphate ceramic layer forms over the inner layer to protect the surface from scratches, punctures, and cracks. This ceramic layer also provides the alloy layer with a continuous supply of phosphate, if needed, to keep the alloy intact.
Unlike traditional coatings which sit on top of the steel surface, EonCoat® chemically bonds with the steel, leaving no room between it and the substrate for corrosion to occur. The strong chemical bond created, along with EonCoat’s self-healing nature, eliminates the need for routine reapplication or manual repair of the coating. EonCoat® only needs to be applied once, and it will prevent corrosion for decades; making monitoring your assets a breeze.
Making the Most of Today’s Technology
The U.S. Department of the Interior reports that half of the nation’s 2.5 million miles of pipeline are more than 50 years old. Corrosion monitoring remains a core concern for the oil & gas industry, and will only continue to grow in importance as the average age of U.S. pipelines increases and the demand for more pipeline development grows.
The technological advancements we’ve covered in this post are signs of great things to come, as the oil & gas industry continues to push into the digital era and leverage technology to improve operations. From drones to sensors to lasting corrosion prevention, the industry will continue to combat corrosion to deliver the world’s resources safely and efficiently. If you’re interested in how our advanced coating can prevent corrosion across your carbon steel assets, contact the team at EonCoat to speak with our experts about your corrosion protection needs.
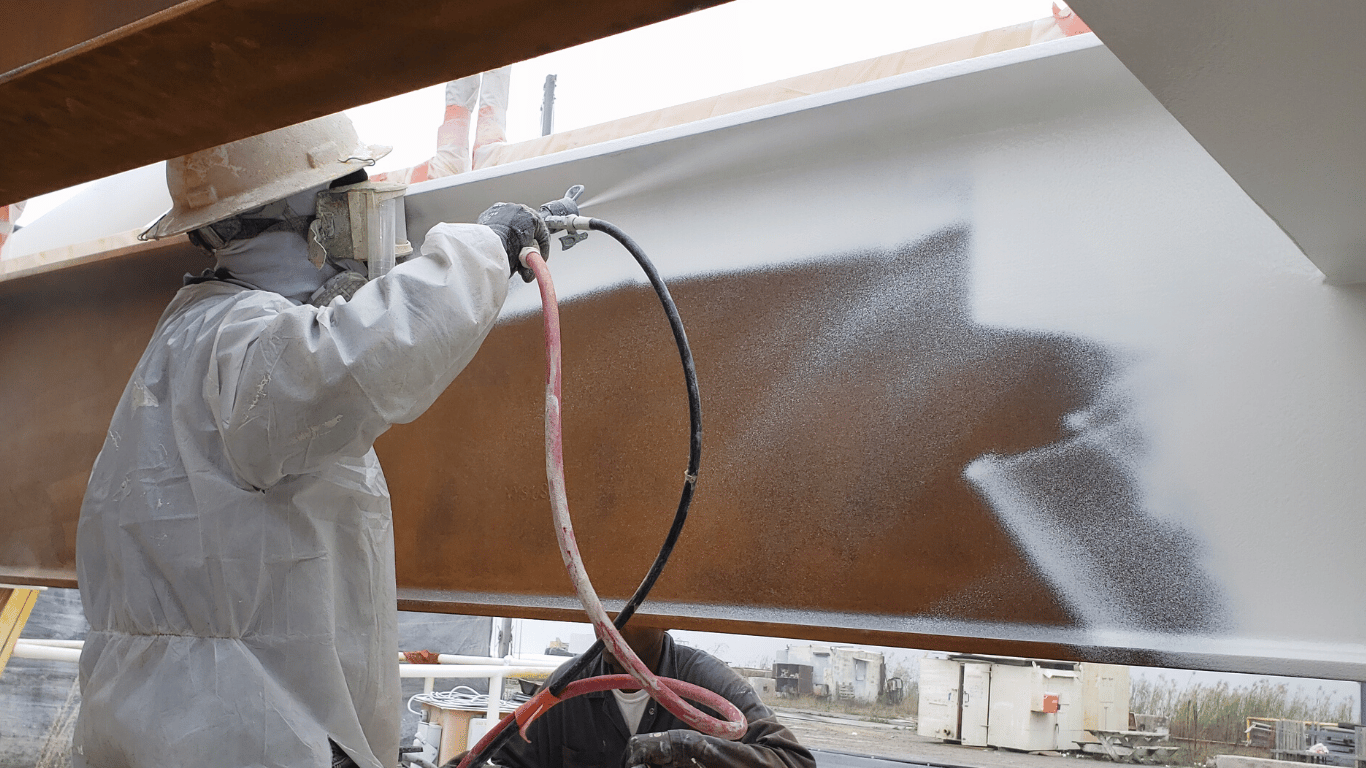
Ready to Learn More About EonCoat?