Everyone likes to avoid the hard work of surface preparation. As a result, we see many “surface tolerant” epoxies claiming that you can apply them to a rusted surface. However, if you look closely at the application guide, it will point out that the performance will always be better on an SSPC10/NACE 2 than over rust, though coating over rust is “acceptable.”
However, every paint and protective coatings expert will tell you that correct surface preparation determines whether the paint or coating job holds up. Conversely, all paints and protective coatings will fail on an improperly prepared surface. EonCoat’s patented permanent corrosion protection is no exception to this rule.
Standards – Everyone Has Them
First, let’s take a look at the minimum surface preparation standard based on the type of substrate:
- Iron & Steel: SSPC-SP14/NACE 8
- Previously painted: SSPC-SP6/NACE 3 (primer recommended)
- Concrete: SSPC-SP13/NACE 6
Additionally, when you look at the condition of the substrate, surface preparation recommendations look like the following:
- White metal blast (new/mill scale): SSPC-SP 5/NACE 1
- Near white metal (new or unused with rust over mill scale): SSPC-SP10/NACE 2
- Commercial blast (in-service or previously coated): SSPC-SP6/NACE
- Brush off blast (even layer of rust/oxide): SSPC-SP7/NACE 4
- High-pressure water jet (previously painted, loose rust or debris): SSPC-SP12/NACE 5
- Concrete (all surface conditions): SSPC-SP13/NACE 6
- Industrial blast cleaning (used, in-service, or previously coated): SSPC-SP14/NACE 8
I don’t see a standard that says, “Skip the surface prep and just start applying.”
EonCoat On Top Of Flash Rust
While EonCoat does have surface preparation standards, it has a much wider range of acceptable surface conditions to deliver outstanding performance. The most apparent surface work condition for EonCoat is that it will work well over a rusted surface. However, that statement does not mean you can coat over thick, flaky rust that will soon disbond from the base metal. No coating will tolerate that.
What you can do is apply EonCoat to tightly bonded rust, particularly the flash rust that begins shortly after you blast a substrate.
Furthermore, no paint or coating will be successful over a dirty, oily surface, so appropriate cleaning before applying EonCoat is essential. Before blast cleaning, you must remove 100% of the following from the carbon steel:
- Loose scale
- Large deposits
- Oil
- Grease
- Cutting Oils
- Residue
- Dirt
- Fins
- Slivers
- Burred or sharp edges
- Weld spatter
- Slag
- Previously applied paints
The EonCoat Application Guide does not say that performance will improve on an SSPC10/NACE2 surface because the performance of EonCoat over white metal or flash rust is the same. The reason is that the acid phosphate in EonCoat will bring the iron on the surface into the solution to create the magnesium iron phosphate alloy layer.
There is no iron in EonCoat, so it must take the iron from the substrate. It can do that from white metal, but it can also dissolve the rust on the surface and take the iron from there. It is a touch easier to get the iron from the rust because of the large surface area the acid gets to attack.
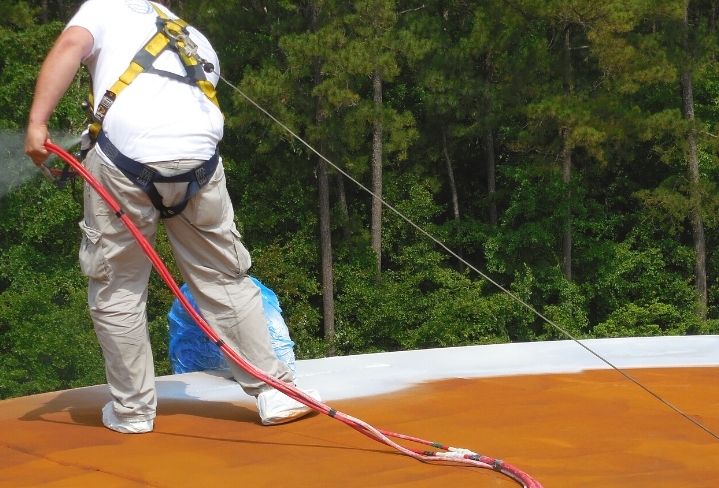
Easy Application Over Flash Rust
One of the most significant advantages of applying EonCoat’s protective coating over rust is that you can prepare the entire surface of the carbon steel asset at one time. Comparatively, with inorganic zinc, it is necessary to blast a small area to white metal and apply the zinc to that area before it flashes. Following the stop-and-go process of the zinc application makes it necessary to blast and coat small areas at a time. Doing things this way significantly extends the downtime of your carbon steel asset and increases all the related labor costs. It is like vacuuming your house five square feet at a time, then putting the vacuum away and getting it back out after each section.
With EonCoat, you can prepare the surface of an entire tank – inside and out – including the roof, in one continuous operation. The previously prepped areas will flash during the surface preparation process, which is not a problem. After the surface preparation is complete, you can apply EonCoat to the entire tank – including the flash rust.
You speed up the application timeframe significantly by preparing everything and then coating everything. It is common for a tank that takes 2 months via conventional methods to be completed in 10 days using EonCoat. In addition to reducing asset downtime, you’ll appreciate saving labor hours, rental equipment costs, and other overhead expenditures. We’ve seen so many companies experience such substantial cost savings that we’re giving you the calculator to see your savings!
There are 3 questions to ask yourself before you apply EonCoat over rust:
- Is the rust tightly bonded?
- Has the surface been cleaned?
- Are you holding a high-pressure plural spray pump or a dual cartridge spray gun in your hand?
If the answer to all three is yes – proceed to apply a minimum of 20 mils at one time. EonCoat will provide enough acid to consume the rust, and give you an excellent alloy layer accompanied by a 30-year warranty.
With conventional paints and coatings, painting over rust does occur. However, the coat-over-rust practice hurts both the life of the paint or coating job and the carbon steel. When you correctly prepare your surface and apply EonCoat, you aren’t just protecting the job and the asset – you are making it better.
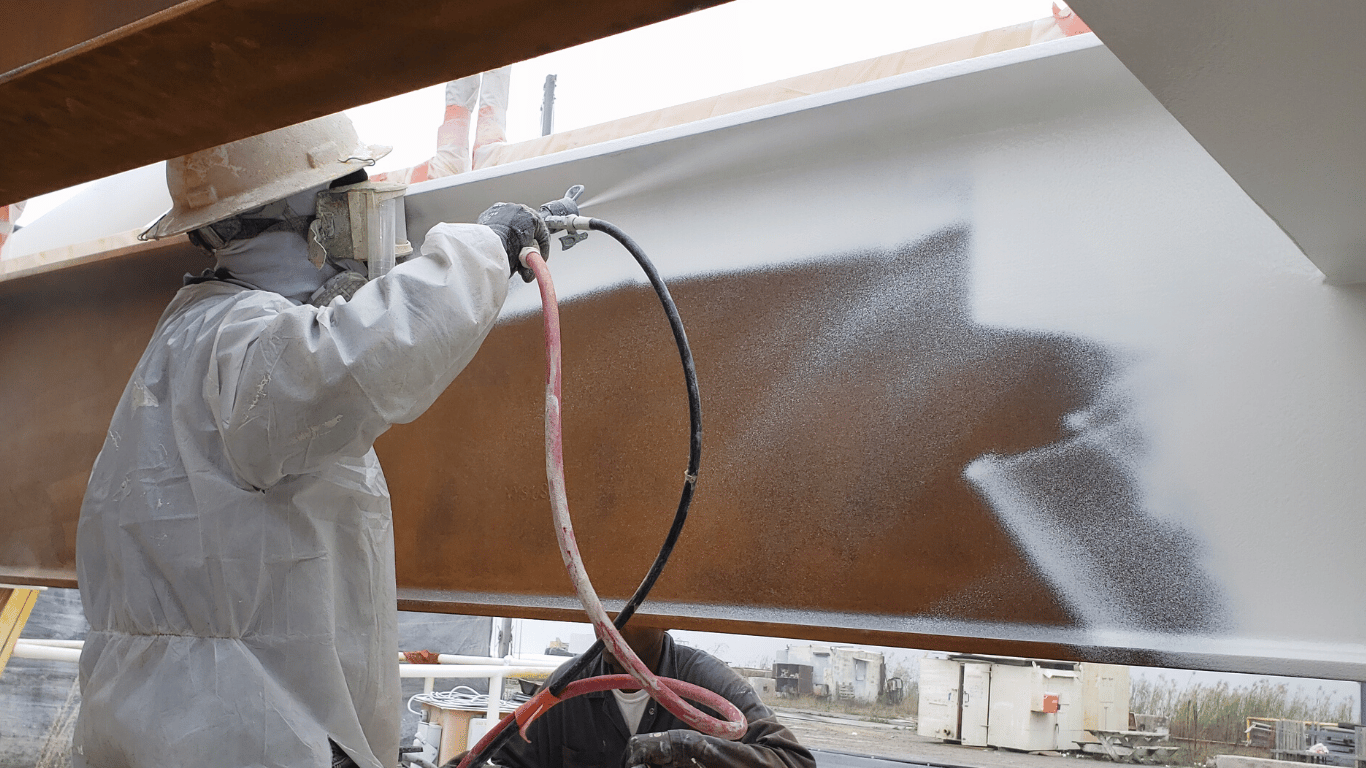
Ready to Learn More About EonCoat?