The Cost-Benefit Analysis Of Surface Preparation Done Well
While we all wish surface preparation time and material expenses didn’t show up in our operational spreadsheets, they exist for a reason. The cost-benefit analysis of a well-done surface preparation job comes down to the cost of surface preparation versus the cost of a catastrophic failure for a mission-critical carbon steel asset with loss of time, loss of revenue, and potential environmental- and employee-exposure risks. To quote Tony Collins, “I don’t see a standard that says, ‘Skip the surface prep and just start applying.”‘
The Root Cause Of All Rust
First, let’s understand the root cause of rust to help you understand the why behind the importance of correctly completing surface preparation tasks. As Tony has taught, corrosion happens when a carbon steel atom loses an electron and bonds with oxygen to restore the charge imbalance. Applying EonCoat directly to the carbon steel allows the electron balance to be restored. When you understand that – everything about surface preparation becomes instantly clear.
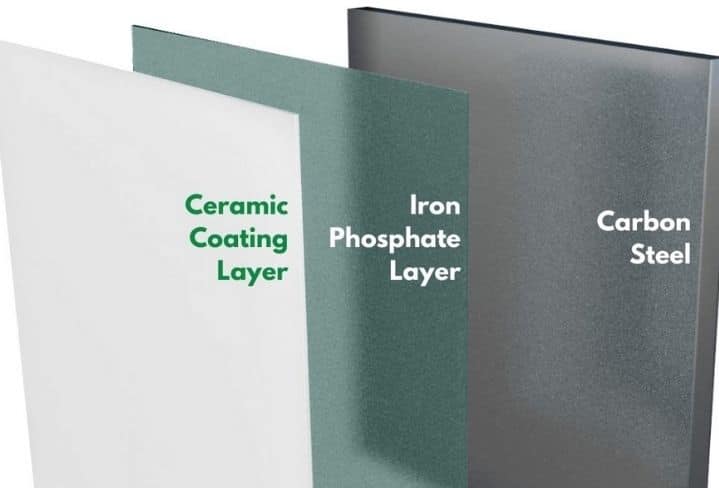
FAQ # 1 Can I Spray On Top Of Old Paint?
The short answer to your question is no – you cannot apply EonCoat on top of old paint. While this is our most common question when people are applying EonCoat, let’s take a moment to go a little deeper – and talk about mill scale and shiny surfaces while we’re at it. Because of the frequency of this question, Tony Collins, our CEO, even wrote a blog post about this topic.
The answer to this question will tie into the answer for FAQ # 3 shortly. Previously painted carbon steel must be prepared to the SSPC – SP6 / NACE 3 / Commercial standard. Chemically speaking, the soluble phosphate must be next to the steel to create an alloyed layer. The higher the phosphate concentration, the better the protection works, and the more corrosive environment the metal can endure while staying protected from corrosion and asset failure.
Mill Scale
Mill scale forms during the rolling process and consists of iron oxides that are bluish/black in their appearance. Mill scale is an initial protection against atmospheric corrosion. However, if left in place, mill scale will ultimately be a barrier between EonCoat’s protective phosphate and the carbon steel.
The need for this uninterrupted alloy layer is why removing all paint and mill scale is critical for the success of the bonding between the EonCoat and the carbon steel. If the alloy layer cannot occur, the protective coating will fail, and your carbon steel asset will corrode.
Shiny Surfaces
Let’s not forget that we said we would discuss shiny surfaces. In EonCoat-speak, a shiny surface is not a reactive surface. Instead, a shiny surface tells us that the carbon steel is now too smooth and too flat for EonCoat to bond successfully. But, again, you will fix this with the abrasive blasting process.
FAQ # 2 Do I Need To Hold The Blast?
No. Let me say that one more time – the answer is no – you do not have to hold the blast of your carbon steel asset prior to applying EonCoat. After you have prepared the surface according to SSPC SPC 6/NACE 3/ISO SA 2/Commercial, you do not need to hold the blast after preparing the surface. Therefore, you do not need to waste time and money applying any name brand of HOLD*BLAST. You can prepare the entire carbon steel asset surface at one time and then apply EonCoat at one time. There is no more clean-a-small-section-apply-a-small-section. The only comparison I know would be vacuuming a small segment of your carpet, putting away the vacuum, looking at the carpet, and then getting your vacuum out to clean another small segment of your carpet. It’s both wholly inefficient and totally unnecessary.
Not having to hold the blast is where the cost savings of EonCoat start to show up. Holding the blast is more expensive than performing the commercial blast and allowing flash rust to form. In addition, you do not need to worry about rain, humidity, or other environmental delays. You don’t even need to worry if your applicator has a family matter and needs to take time off.
EonCoat Loves Flash Rust
The carbon steel asset can contain a moderate (M) level of flash rust, as described in SSPC-SP WJ-2, and EonCoat will successfully bond. Remember, EonCoat performs equally well on white metal (that’s a more expensive level of preparation) as it does flash rust. The acid phosphate in the EonCoat will bring the iron on the surface into the solution to create a magnesium iron phosphate alloy layer.
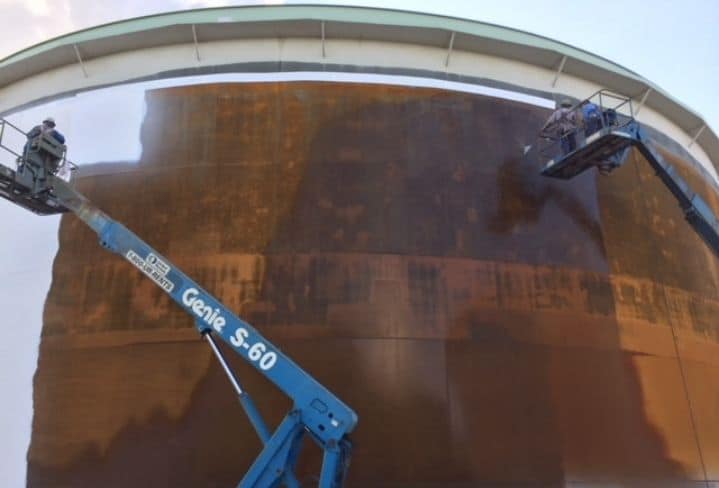
What does this mean to the applicator on the job site? It simply means that flash rust is great, so long as it’s tight and not loose or dusty. As seen in this video, flash rust tells us the steel is reactive and tells us the substrate will bond well with EonCoat. The rated-as-moderate acceptable level of flash rust allows you to clean the entire carbon steel substrate at once. EonCoat’s ability to bond with flash rust makes it easy for folks with bulk tanks, lengthy pipelines, or a rainy season. Preparing everything and then applying EonCoat takes a typical 2-month job and reduces it to a 10-day job – that’s a cost savings of 50 employee days.
FAQ #3 What standard does the profile need to meet after blasting?
This is a great question with a simple, short answer with a more engaged full explanation. The simple answer is that no standard perfectly meets the surface preparation requirements for your carbon steel asset. However, the closest standard that will result in reactive carbon steel is SSPC SP6/NACE 3/ISO SA 2/Commercial preparation standards. Keep reading for the full context explanation!
We’ll start with SSPC / NACE:
In North America, the original surface prep standard was written by
an architectural group in the 1960s for steel workers in Pittsburgh.
The Society for Steel Painting Structures formed around the
standards. The SSPC standards are text descriptions, not pictorial,
although they are accompanied by visual guides (VIS) with photo
references. SSPC/NACE numbers them in reverse order, by
increasing surface cleanliness.
In Comparison to ISO 8501:
ISO 8501 was published by the International Standards Organization
in 1988, after combining the content from the 1967 Swedish Standard
SIS 055900 with the German DIN 55928. ISO 8501 is a pictorial
standard showing the appearance of different rust grades at various
levels of cleanliness, although it also contains text descriptions of
the cleanliness levels. ISO 8501 ranks cleanliness levels in order of
increasing work required.

Because EonCoat must be applied directly to a carbon steel asset with no barrier in between, the SSPC-SP 6/NACE 3/ISO SA 2/Commercial is the closest standard. The practical definition of that standard “allows for stains or shadows up to 33% of each unit area of the surface to remain … removes all visible oil, grease, dust, mill scale, rust, coating, oxides, corrosion products, and any other foreign matter on the surface.” Please note that because EonCoat alloys to the metal, it is unnecessary to remove all iron oxide (remember, the most common form of iron oxide is rust).
SSPC-SP 6/NACE 3 falls between Industrial Blast Cleaning and the SSPC-SP10/NACE 2 Near-White blast cleaning. Near-white and white metal blast cleaning have higher associated costs. EonCoat’s requirement for Commercial/SSPC SPC 6/NACE 3 has a much lower cost point. This more accessible level of blast cleaning amounts to the customer having substantial savings for labor- and material-related costs.
Oil, Grease, and Irregular Surfaces
What I’m about to say may seem obvious to those in the industry, but let’s take a moment and clarify two basics. First, I want to make sure we’re all on the same page for oil and grease, as well as irregular surfaces.
First, you must remove any oil and grease prior to any blasting preparation process. If you don’t remove the oil and grease first, the blasting process will smear those two obstacles across the surface. Therefore, in our Detailed Application Guide, we specify that any cloth material or compressed air used in the cleaning must be clean – and free of oil and grease. In addition, you can refer to ASTM D4285, the Standard Test Method for Indicating Oil or Water in Compressed Air – to verify that the compressed air you will use in the preparation process will not leave a greasy residue.
The second basic has to do with the removal of irregular surfaces. Before the blast cleaning, you must remove all irregular surfaces. Irregular surfaces include:
- fins,
- slivers,
- burred or sharp edges,
- weld spatter,
- and slag.
We’re Here To Help
If you would like to learn more about Surface Preparation for EonCoat, feel free to visit our webpage. We even have a Surface Preparation Checklist to make life easier for the applicators in the field. You can tell us about your unique needs at our Contact Us page. We feel so strongly about supporting our customers that we are available by phone, Monday through Friday, from 9:00 AM to 5:00 PM EST.
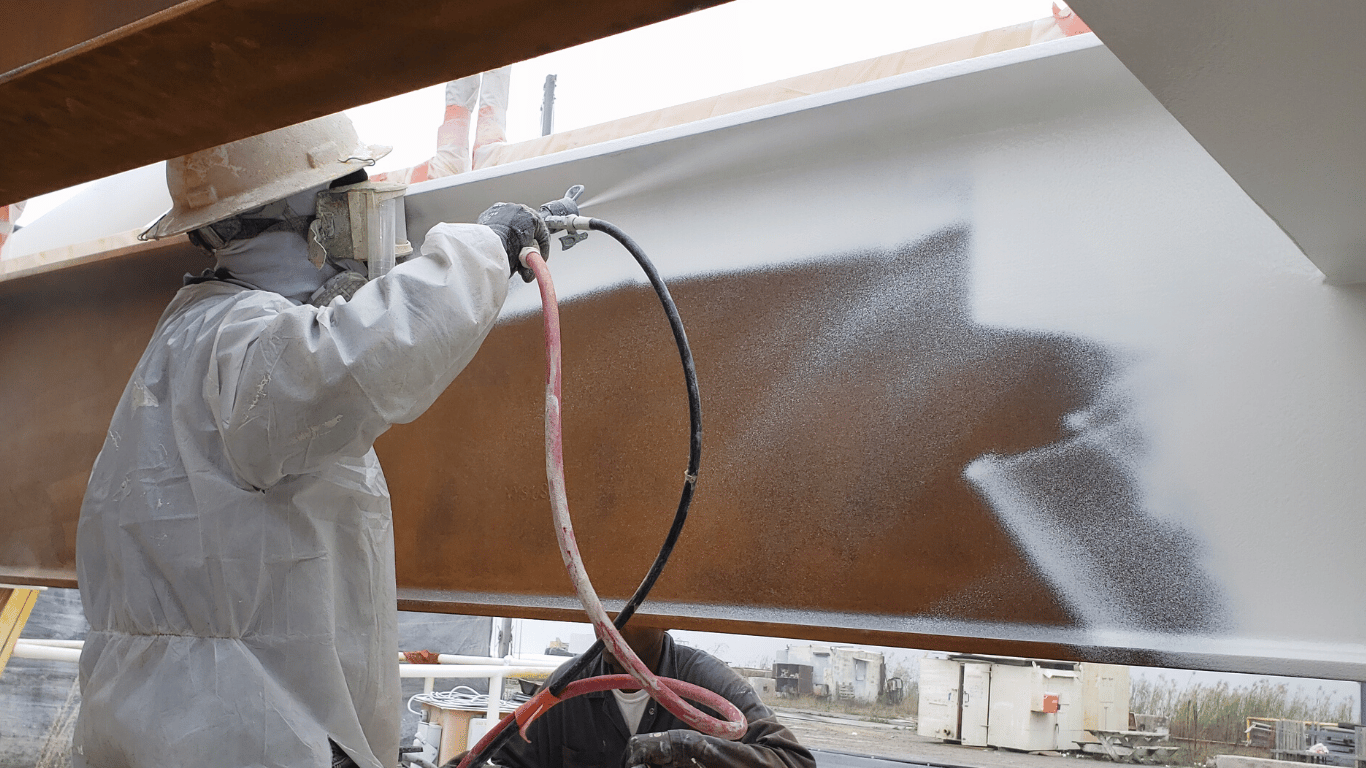
Ready to Learn More About EonCoat?