In July of 2014, the Federal Railroad Administration (FRA), a United States Department of Transportation division, issued a final report entitled Rail Base Corrosion and Cracking Prevention Study. The FRA funded the study, and the Edison Welding Institute (EWI) conducted the study. EonCoat did not charge for any product or application service as part of this research trial. It was initiated “in response to the specific issue of track damage and derailment resulting from corrosive underside attack to the rail.” Four of the biggest names in the railroad industry participated in the study: Amtrak, Long Island Rail Road, Port Authority Trans-Hudson, and Norfolk Southern Corporation.
The study’s overarching goal was to test “anti-corrosion treatments that render the rail surface immune to corrosion or mitigate its spread should initial corrosion occur.” Enter EonCoat. Other protective coatings mechanically lay on top of the carbon steel. However, EonCoat’s Part A (the acid) and Part B (the base) meet at the time of application and form an intimate two layers of protection that chemically alter the carbon steel surface and provide corrosion-resistant properties unlike anything else on the market. After exhaustive testing, the report concluded:
“EonCoat was effective in preventing corrosion in saltwater environments. It enabled extended fatigue life, even on damaged rail subjected to aggressive corrosive environments, and gave performance similar to that for undamaged, uncorroded rail.”
Considering how frequently rail parts and pieces are replaced, that statement was a clarion call to the entire rail industry.
Side by Side Salt Fog Chamber Testing Results of EWI Coating vs. EonCoat Corrosion Prevention Coating
Third-party validation of this magnitude had a significant impact on EonCoat. So you can imagine our excitement when they announced a Phase II study. The Rail Base Corrosion and Cracking Prevention: Phase 2 was also funded by the FRA, with testing also carried out by the folks at EWI. So, of course, everyone at EonCoat was “all in.”
The study started in March 2014 and concluded in April 2017. The same four railroad companies participated in the study by providing “rail segments and tie plates for treatment and covered the cost of installation and monitoring.” The primary goal of the Phase 2 study was to “place treated rails into the field for observation under true running conditions.” With approximately 160,141 miles of track in the US, anyone can see the importance of a well-maintained rail transit system carrying goods and passengers safely.
Overview of North American Rail System Extracted from ARCGIS
In the Background section of the Phase 2 study, the authors lay the foundation for the importance of fixing rail base corrosion, cite:
“Rail base corrosion has been observed by rail operators in areas where water is periodically present at the base of the rail … Some corrosion was invasive and found to advance as much as ¼ in. upward from the area where the rail base crosses tie plates. There is the possibility that the edge of the corroded area could act as a stress concentrator that would allow fatigue crack to initiate and propagate up the rail. Furthermore, the effects of corrosive antagonists can be amplified by mechanical abuse and fatigue, exposure to road deicing materials, and electrical currents transmitted through the rail base and tie plate path to earth ground … Treatment of the rail bottom surface has the potential to be effective in limiting the progression of rail corrosion, which leads to increasing rail life, reliability, and overall rail safety. Reducing or mitigating rail corrosion will improve the safety of rail operations and the reliability of its infrastructure.”
The four participating transit systems provided 40-foot-long rail segments in addition to tie plates. EonCoat prepared and subsequently applied EonCoat Corrosion Protection Version 4 to the steel rail and plates. Each railroad company then installed its own tracks in various corrosion environments.
In the Fall of 2015, reports were coming that were indicative of flaw detection with various corrosion rate data points. So, as chemists and engineers, we had to roll up our sleeves, start asking questions, and validating data.
Inspection and Investigation
When discussions began, EonCoat looked at five essential questions:
- What indicates something went wrong?
- When did the indications occur?
- How do we know what went wrong?
- Why did it go wrong?
- What did EonCoat do to prevent railroad corrosion in the future?
What Indicates Something Went Wrong?
The folks at the rail companies could visibly identify chipping and spalling on the rails. Of note:
“all the participating railroads reported that damage to the coating may have occurred during installation. They also reported that chipping and spalling are common on the rails themselves. Where coating is being lost, there is evidence of incipient corrosion. However, the tie plates appear to be holding up very well and generally did not display mechanical damage to the coatings.”
When Did Indications Occur?
The small bubbles in question were seen at the time of application. The initial reports of problems surfaced in the Fall of 2015, after 6 to 10 months of service. The exact time for chipping and spalling are unclear. The rail transit systems have a consistent and high-quality program that involves inspecting railway tracks for corrosion damage that may indicate the need for intervention.
How Do We Know What Went Wrong?
With the initial field reporting, EonCoat engaged in substantial additional, rigorous testing. With the new round of testing, based on the data from the field tests, EonCoat learned three key points. These new discoveries were pivotal in developing all future EonCoat versions and products.
Why Did It Go Wrong?
EonCoat learned three factors influenced the rails’ coating adhesion and anti-corrosive performance. Next, we applied the new information to the Engineering Cycle. Finally, EonCoat researched the problem, imagined possible solutions, and created EonCoat Version 5. Let’s look at the three key issues from which we learned.
- As mentioned, bubbles (likely hydrogen) were a problem. If the EonCoat Version 4 hardened faster than the surface could chemically react, hydrogen gas can form small bubbles. The layer with the bubbles would lead to a “weak interfacial layer and adhesion failure.”
- The chemistry of the steel rails is different from that of the steel tie plate. These differences “can produce a different surface grain structure and chemistry. This may influence adhesion as well. Therefore, both chemistry and processing can influence surface adhesion, with the adhesion of rail steel being inherently more difficult than adhesion to tie plates.”
- The third point we learned was related to the size of the carbon steel asset being protected. The report states:
“Therefore, it is possible the combination of size, surface chemistry, surface morphology, and coating time may have worked against good coating adhesion on the rails, while providing better mechanical performance on the tie plates. Taken in concert with the formation of bubbles and a foamy region near the steel surface, these linked concepts suggested that the causes for poor adhesion had been identified.”
All the questions above are essential. However, the most critical question we asked comes next in this story. What did EonCoat do to have a different outcome for future rail base corrosion detection and prevention?
What Did EonCoat Do To Prevent Rail Corrosion In The Future?
To quote Tony Collins, EonCoat’s CEO, “reducing the problem to its simplest form often causes the answer to fall out.” Once EonCoat clarified the issues, the two answers to preventing rail corrosion became clear.
- High carbon steels are less reactive and require more acid dwell time to passivate the metal. The very next version of EonCoat addressed this new knowledge.
Acid on metal creates hydrogen gas, which can form at the coating metal interface, causing the ceramic to disbond. The addition of an oxidizer eliminates the bubbles. Now the ceramic bond is even more complete and more intimate.
Initiating these changes has allowed us to go on and serve other rail industry customers, like Chicago Transit Authority and LB Foster, with success. Because of that, we are grateful for this early learning experience.
What do the Results of the Phase 2 Study say about EonCoat?
- The FRA published the Phase 2 Study results in April 2018. With respect to the EonCoat protected rail that had been installed in 2017, the report notes:
“In severe corrosion locations, rail may be replaced annually. At the time of this report, several of the Phase 2 rails are still in service. Since some of these rails are still in service after more than 2 years of field installation, it appears that the coating does provide added protection for the rail.”
Simply stated, even though there were some issues, EonCoat extended the life cycle of train rails by 100%.
1. As part of the Continuous Quality Improvement program at EonCoat and to answer the questions previously referenced, more sample panels were tested under highly corrosive conditions. Based on this additional testing, the report states:
“On the scribed plate, there is obvious pulling back of the coating from the scribe region, however, there is still rust protection outside the region. That is a trait of the EonCoat V system. It converts the surface, not just coats it, so there is additional resistance to corrosion with time in regions where coating has been physically lost.”
The improvements made to EonCoat allow scribes – or other types of organically occurring trauma – to self-heal and continue to protect the carbon steel.
1. The conclusion of the report is very clear about the importance of preventing rust and corrosion in the rail industry:
“Rail base corrosion represents a significant safety concern for passenger and freight rail operating on tracks in highly corrosive environments, such as locations near platforms, in tunnels, under overpasses, or on rail lines operated near bodies of saltwater. Untreated rail, even in the absence of electrification, succumbs to environmental corrosion attached very soon after installation. These regions are not easily accessible for inspection, which is of great concern to the rail industry. Having some form of corrosion protection between the rail base and the tie plate would be useful.”
Utilizing EonCoat to protect carbon steel in the railroad industry changes the rail landscape. Specifically, the dynamics of:
- dependence on railroad companies purchasing new steel every year,
- rail lines being taken out of service to exchange for new rails, and
- increased safety for passengers, goods, and railroad employees
All these can significantly add value to the return on investment for any railroad stakeholder.
What Is the Next Best Step?
While writing this blog, I received a timely news update about rust and corrosion on a new track. The Metro train system in our nation’s capital needs an Emergency Response Drill on a new rail line so the safety certification can be issued. Unfortunately, the rails were so rusted that the drill had to be postponed. Imagine if they had applied EonCoat – the rust and corrosion would not have been a problem. It’s not too late. EonCoat can be applied to the new rails being installed and prevent this from happening again.
If you’re in the rail industry and want to talk with someone, feel free to click the Contact Us Button below or give us a call. We’ve coated so many different tie plates that we may already have a mold that would make for easy application. Our experience in coating train tracks can help you save time and money. If you’d like to learn more, sign up for our Free E-Book
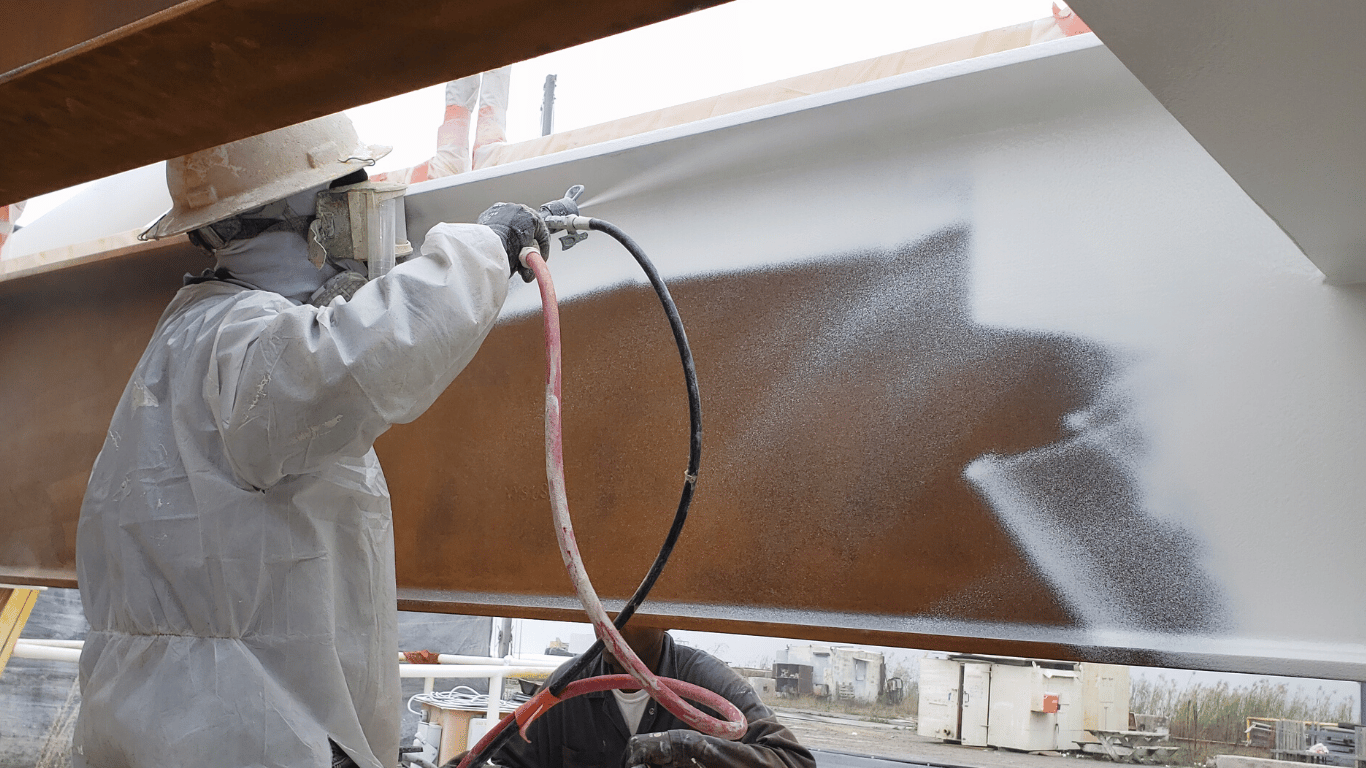
Ready to Learn More About EonCoat?