EonCoat’s History with the Rail Industry
Thank you for coming back for week two of the Intercity Passenger Rail service Grant Applications. If you’re still reviewing the Notice Of Funding Opportunity (NOFO), this blog article may help you polish off the remaining details of your grant application.
Alternatively, if you’re in another industry (we see you, bulk storage tank owners) and you came back to learn how folks utilize EonCoat in infrastructure projects, we’re glad you ‘came along for the ride.’ See what I did there? Telling more dad jokes is still a goal for 2023.
Our Roots in Rail
The use of EonCoat in railroad components dates to the beginning of a rail study conducted by the Federal Railroad Administration (FRA) starting in September 2012. The first study culminated in the report published in July 2014. EonCoat has been ‘full steam ahead” with the rail industry ever since.
For this Phase I study, Amtrak, Long Island Rail Road, Port Authority Trans-Hudson, and Norfolk Southern Corporation all participated in the study “in response to the specific issue of track damage and derailment resulting in corrosive underside attach to the rail.” The essential takeaway from that Phase I study is as follows:
“EonCoat was effective in preventing corrosion in saltwater environments. It enabled extended fatigue life, even on damaged rail subjected to aggressive corrosive environments, and gave performance similar to that for undamaged, uncorroded rail.”
In the second study, the Phase 2 report results noted:
“In severe corrosion locations, rail may be replaced annually. At the time of this report, several of the Phase 2 rails are still in service. Since some of these rails are still in service after more than 2 years of field installation, it appears that the coating does provide added protection for the rail.”
The Phase 2 conclusion is very clear about the importance of preventing rust and corrosion in the rail industry:
“Rail base corrosion represents a significant safety concern for passenger and freight rail operating on tracks in highly corrosive environments, such as locations near platforms, in tunnels, under overpasses, or on rail lines operated near bodies of saltwater. Untreated rail, even in the absence of electrification, succumbs to environmental corrosion attached very soon after installation. These regions are not easily accessible for inspection, which is of great concern to the rail industry. Having some form of corrosion protection between the rail base and the tie plate would be useful.”
The takeaway from the Phase 2 study is that the use of EonCoat in the rail industry can:
- reduce the dependence of railroad companies on replacing steel every year,
- reduce the number of rail lines being taken out of service to exchange for new rail parts, and
- increased safety for passengers, goods, and employees.
You can read EonCoat’s blog article about both FRA studies at this hyperlink.
At EonCoat, along with valuing reliable and valid third-party testing data, we also highly value customer feedback. Keep reading to see what one specific rail customer has to say about using EonCoat.
What Do Our Customers Say About EonCoat?
Chicago Transit Authority utilizes LB Foster as its steel manufacturer and supplier. As a result, the two organizations worked together on a presentation at the 2021 Virtual International Crosstie & Fastening System Symposium. Specifically, the presentation by Sheen Fong of LB Foster and Matt Gibbs of Chicago Transit Authority is entitled “Direct Fixation Track: History and Development.” You can see the entire presentation at this hyperlink.
Let me help you out with the highlight reel by showing the specific times when EonCoat is discussed:
- 6:59 LB Foster and CTA are using EonCoat-protected fasteners for corrosion resistance to extend the previously anticipated lifecycle.
- 12:32 Current Issues are as follows:
- Installation of the track is critical and sub-standard track will have a decreased life span and increased maintenance costs.
- Water leaks and moisture severely affect track systems.
- Repairs can be time-consuming, expensive and affect train operations.
- 14:30 This slide shows the “Future of Direct Fixation at CTA,” with point three being “fasteners with corrosion resistance” The photo section of that slide shows the Foster F50-1 with EonCoat protecting the exposed carbon steel.
- 22:16 There is an ongoing focus on higher-performance, corrosion-resistant coatings to “significantly extend the useful life of our fasteners.”
- 24:01 “High-performance, corrosion-resistant coatings such as EonCoat. EonCoat is a two-part coating that uses a ceramic coating that significantly improves abrasion resistance and also improves our corrosion resistance.”
- 29:54 At their test lab in Suwanee, Georgia, LB Foster has engaged in extensive testing, including environmental chambers and electrical test equipment.
- 30:40 On this “Looking Forward” slide, the presenters once again spotlight that the use of EonCoat represents “advancements in material technology that allow for higher performance … or different coatings to help extend the service life of our fasteners such as the EonCoating.”
- 30:56 Agency specifications are evolving to reflect the next generation of direct fixation fasteners … different loading conditions for high resilience fasteners …”
How Does EonCoat Specifically Help the Rail Industry?
That was the question I posed to Tony Collins, our CEO, as I was trying to grasp a deeper understanding of the subject. His explanation (and world-famous whiteboard drawings) helped make everything clear. Here’s what he taught me.
The global problem with rail is that it will break in two, which is known to cause train derailments. The breaking can be so bad in highly corrosive areas that daily inspections are mandatory. These daily inspections are the only way to ensure train, employee, passenger, and freight safety.
The folks at Edison Welding Institute (EWI), who did the research mentioned previously in this article, were contracted to help address this problem.
To test the strength and lifecycle of the rail, EWI devised a test where the rail was placed over two supports. They then placed a cyclic load of 15,000 pounds (15 Kips) atop the rail. This setup mimicked the real-world experience of rail, and the cycling began.
- The first level of testing identified that the new rail will complete 5 million cycles without breaking.
- The next phase of the test involved cutting a Charpy notch into the base of the rail and then submitting that rail to the 15 Kips cyclic load. A rail with a Charpy notch will break in 2.5 million cycles, essentially cutting the life cycle of the rail by half.
- Another testing component had the rail with the Charpy notch placed in a salt fog chamber with the same 15 Kips cyclic load. We learned that rail will break in 15,000 cycles. What does that mean? Mathematically, a piece of rail intended to operate in a corrosive environment with a Charpy notch will last 0.03% of its expected lifespan.
- If every train car represents four cycles, the rail in the corrosive environment with the notch will only last approximately 4,000 cars worth of service.
- Put all the above data together on a rail line that serves Class 1 trains, which can pull more than 100 cars, using 100 as an average. For the rail with the Charpy notch, in a corrosive setting, only 40 class one trains can travel on that rail before it needs replacement.
The rails with the Charpy notch were then treated with EonCoat, loaded with 15 Kips of cyclic load, and placed in a salt fog chamber. At 3.6 million cycles, the test was stopped because the crack had not propagated, nor had the rail even started showing signs of stress corrosion cracking.
How is that possible?
While EonCoat is effective in many industries against many types of corrosion, EonCoat is the solution for stress corrosion cracking for the rail industry.
What does that mean for the Intercity Passenger Rail Grant Applications?
Let’s take the Northeast Rail Corridor (NEC) as an example of the implications of corrosion protection on rail, plates, and fasteners. In the United States, 17% of the population lives along the approximately 457 miles of Northeast Corridor rail lines. That’s a lot of folks commuting along a big swath of tracks.
- Imagine if rail, plates, and fasteners last longer because EonCoat protects them.
- Imagine if more trains ran on time because there was less repair-related delay.
- Imagine if freight and passenger rail services replaced less carbon steel, lowering their carbon footprint.
- Imagine if freight and passenger rail services replaced less carbon steel and significantly reduced their inspection, maintenance, and repair (IMR) budget.
Image Extracted from: NEC-Commission.com
The US Department of Transportation has added an additional $2.2 billion to this grant process. When the additional money was allocated, the grant deadline was adjusted. Applications are due no later than 5:00 PM ET on April 21, 2023.
All the information we’ve presented means the grant money you receive and earmark for corrosion protection or corrosion prevention on rail, plates, and fasteners can best be obtained by selecting EonCoat Corrosion Protection.
Are you working on your grant application and ready to speak with a corrosion expert? Click the button below, and a Corrosion Expert will reach out to you within one business day.
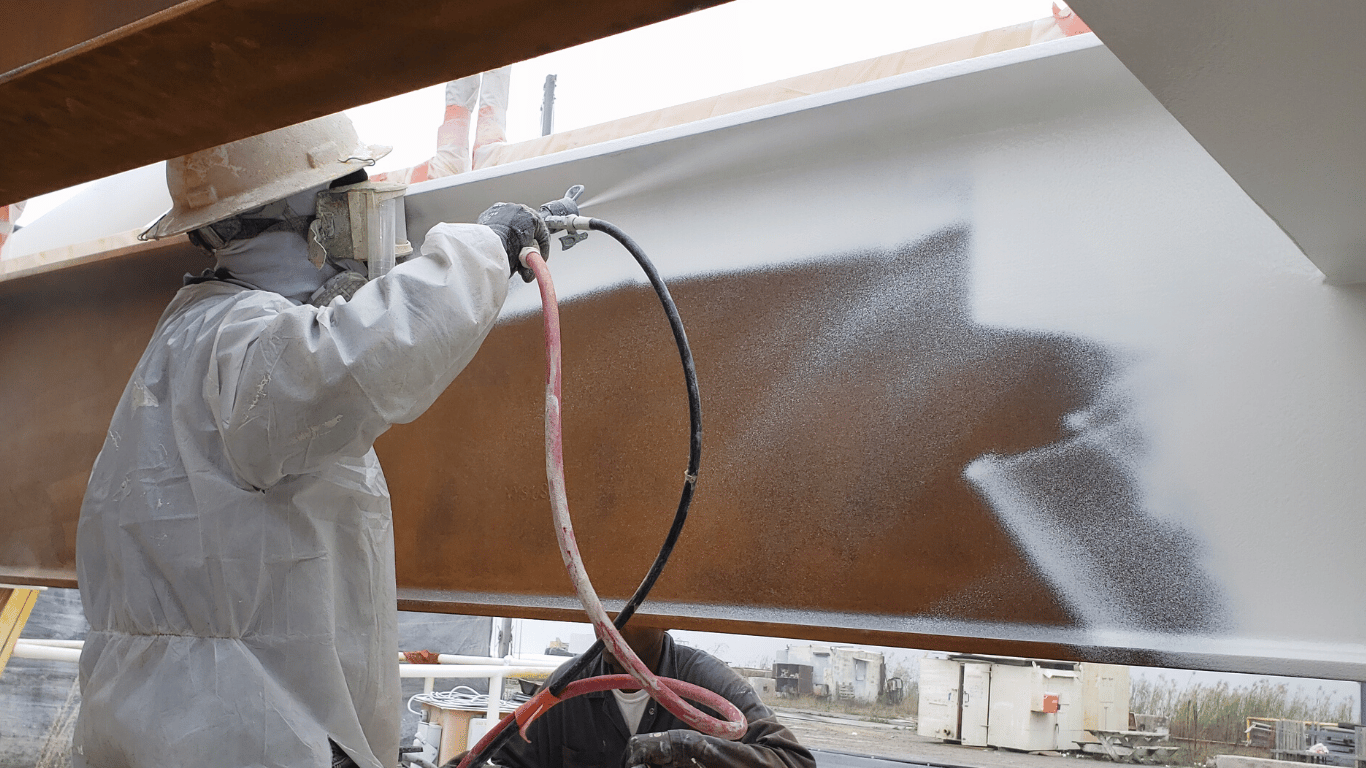
Ready to Learn More About EonCoat?