We all know that petrochemicals are made from petroleum and natural gas. Let’s dig a little deeper into the oil and gas industry to see how EonCoat can help eliminate corrosion in these globally critical processes and facilities.
Petrochemicals contribute to everything from tires, rubber, resins, protective coatings, paints, and embalming fluid. Petrochemicals are even in your laundry detergent. The current most significant uses of petrochemicals globally are plastics (in their many forms) and transportation. However, it’s not the finished product (that soda bottle sitting on your desk) that creates corrosion damage in the petrochemical facilities.
In the life cycle of oil and gas production, going from raw material to petrochemical to a finished product, corrosion prevention can be highly effective at the following intervals:
- The extraction points
- Transportation of raw materials (pipelines)
- Manufacturing of petrochemicals, including some of the final products
- Waste management and recycling of any materials.
Essentially, you sitting at a desk consuming your afternoon drink from a plastic bottle is the part that doesn’t need protection. However, the rest of the process can benefit from corrosion prevention and protection.
Natural gas production and delivery process:
What are the costs associated with corrosion problems?
We must realize that corrosion in the life cycle of petrochemicals and at a petrochemical plant present itself in a variety of ways.
Those corrosion-related costs can look like a loss of:
- Money
- Raw- or in-production materials
- Asset time
- Employee time
- Equipment
Ultimately each of these losses impacts saleable products and the company’s bottom line. Minimizing these costs is where EonCoat can be cost-effective. EonCoat requires straightforward surface preparation and application while offering corrosion protection for the lifetime of the carbon steel asset (ask us about our 30-year warranty).
What makes carbon steel prone to corrosion?
A simple understanding of corrosion in petrochemical, oil – or any other industry – helps the end-user understand how to prevent corrosion and realize how they will save money. Corrosion is a chemical process of electron imbalance, so it makes sense that the answer is as simple as fixing the electron imbalance. Apply that understanding to the current two-part or three-part protective paints used by many petrochemical plants.
Those paint jobs must be repeated every so often because the paints mechanically lay on top of the carbon steel. Eventually, something interferes with that mechanical connection, and then corrosion happens. As a completely different technology, EonCoat creates a chemical change by restoring the electron balance. In doing this, EonCoat forms a chemical alloy to the carbon steel surface.
Recently, we had a video conference with a plant manager who until now has had pipes and tanks recoated with three-part paints every two to three years. In the conference call, we saw him calculating how much it’s costing him in paint product, down asset time, and personnel over 30 years. His jaw dropped when he realized how much money he would save by protecting the same asset once with EonCoat.
EonCoat Vs. Thermal Sprayed Aluminum
Now let’s compare EonCoat to parts of the petrochemical refinement process that are already using a more traditional thermal sprayed aluminum (TSA). Along with the financial costs, the creation of TSA is a highly corrosive process with environmental costs.
- TSA is $30 per square foot, compared to EonCoat’s $2 per square foot.
- EonCoat only requires a NACE 3 commercial blast, but TSA requires a white metal finish (NACE1). That cost saving is significant.
- TSA application rate is 50 sq. feet/hour, but the same size EonCoat application job is completed at 600 sq feet/hour. If you must take that pipeline, tank, or other carbon steel asset out of service for coating – this comparison alone makes EonCoat the easy choice.
An asset’s return to service is often the most critical factor in a petrochemical refinery. Return to service includes surface prep time, application time, and time to dry or cure.
For example, suppose you’re on an application project and have a weather delay. In the case of an application-specific weather delay, you can appreciate that EonCoat has fewer application-related weather constraints than most other systems, which is a significant factor in return to service. Finally, EonCoat is dry to touch in 5 minutes and cured in 15 minutes. Many times, carbon steel assets are returned to service within the hour of an application job of EonCoat.
EonCoat vs. Common Three Coat Systems
Let’s look at the graphic below. You’ll start to see how much more efficient the technology behind EonCoat is, in comparison to traditional three-coat systems typically used in the petrochemical industry.
When applying EonCoat:
- Prepare the surface (SSPC-SP6, NACE3, ISO-SA2)
- Apply EonCoat
- Wait 15 minutes to cure
- Return asset to service
In a three-coat, protective paint coating system, you must:
- Prepare the surface (SSPC-SP5, NACE1, ISO-SA3)
- Paint the first coat – typically an inorganic zinc
- Wait for it to dry
- Paint the second coat – typically an epoxy
- Wait for it to dry
- Paint the third coat – typically a urethane or polyurethane
- Wait for it to dry
- THEN return your asset to service.
When was the last time you read an SDS or TDS for a zinc phosphate primer? We highly suggest you take a few moments to read one. Just ponder these terms directly from an SDS and TDS for a zinc phosphate primer:
- Flammable liquid and vapor
- Toxic to aquatic life with long-lasting effects
- May cause drowsiness or dizziness
- 12 hours to hard dry
- 5-7 days to full hardness.
With the onset of the COVID 19 crisis, we saw an unprecedented global decline in oil and gas demand. However, the recent changes just since 2022 started, have caused the oil and gas industry to experience an explosion of consumer demand for pretty much all things related to the petrochemical industry. Unfortunately, unpredictable fluctuations make any additional downtime extremely expensive.
In review, we understand how market, weather, geographic, and geopolitical conditions can create an immediate need for your carbon steel assets, which underscores why corrosion prevention is so important. For our customers in the petrochemical industry, EonCoat offers a much faster return to service due to less surface preparation requirements, rapid cure time, and fewer application-related weather constraints.
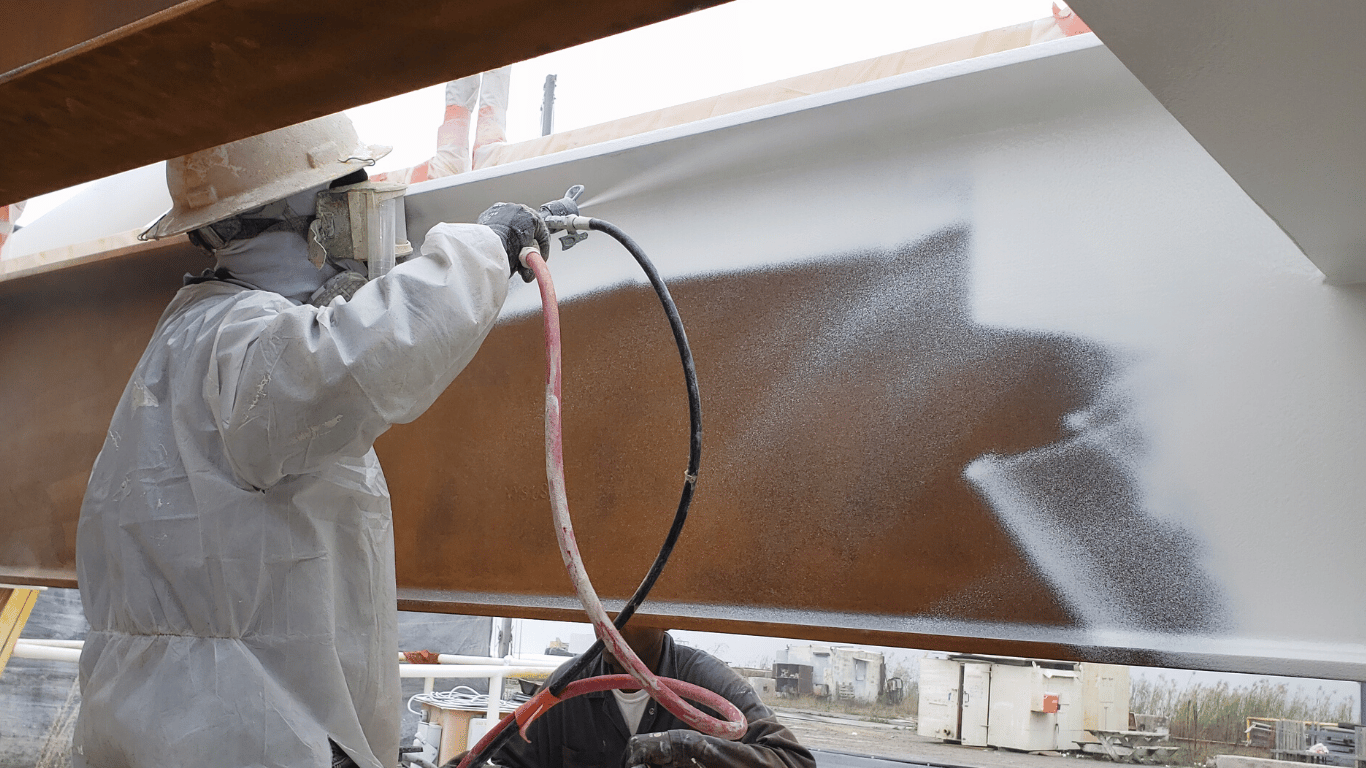
Ready to Learn More About EonCoat?