Money, Production, Environment, and Employee Health – Just To Name A Few
Our Customer Success folks tell me that customers frequently ask about the difference between EonCoat to galvanizing carbon steel. Primarily, companies tend to focus on the initial cost and the lifetime value. Those are great questions! Because EonCoat is a disruptive technology, engineers and fabricators who grew up with galvanized steel products may not immediately understand the differences.
An intelligent and thorough analysis will typically center on a few critical issues when comparing one coating system to another.
There are six main points to consider.
1- Corrosion performance
2- Initial cost
3- Long term cost
4- Damage to the environment
5- Health impacts to people on the job
6- Repair of damage to the coating
I’m going to break down each of these areas of focus.
CORROSION PERFORMANCE
Galvanic protection is a rugged covering that lasts for a long time in areas not wet or salty. In other words, it works well if the environment isn’t corrosive.
The charts below, provided by the American Galvanizers Association, show the thickness of molten zinc applied to steel and the corresponding typical corrosion rates. The cost estimates in this comparison are based on the thicknesses in these charts. Therefore, more zinc would mean a higher initial cost.
The math shows that galvanizing, applied at the minimum recommended thickness, will only last an estimated 5 to 10 years in wet and salty areas but can last for a century in inland urban areas – in a dry environment with no salt in the air.
An applicator has good reasons to apply the minimum specified thickness in the galvanizing process. First, there is no practical method to repair or replace Galvanizing once the structures are in place. So if corrosion starts, there isn’t a cost-effective repair technique. It would be necessary to remove all galvanizing via grit blasting and start over with another method. Galvanized steel, and the industry attached to it, have become the beast that needs to be fed.
The applicator can increase the thickness and can therefore extend the life of the protected carbon steel asset. However, the end-user needs to be knowledgeable because the galvanizer’s cost increases significantly as the relative thickness increases.
EonCoat, as the alternative and disruptive technology, is a permanent corrosion prevention solution. Because of its unique formulation and application, we offer a 30-year warranty – even in harsh environments. We have outperformed all of our competitors in the most corrosive environments, including salty and wet areas.
INITIAL COST
According to the American Galvanizing Association, the initial cost of applying hot-dip Galvanizing, according to the American Galvanizing Association, ranges from $1.10 for light structural steel to $4.40 per square foot for heavy structural steel. In addition, the process galvanizing process must be done in a galvanizing-specific shop environment. That is a restrictive and costly barrier. The customer must now add travel costs to the galvanizing shop from the worksite. An asset owner must consider this additional expense when estimating the overall corrosion prevention and asset maintenance cost.
When a customer applies EonCoat in a shop environment and has accomplished surface prep with automated equipment, the estimated cost of EonCoat is around $2.00 per square foot regardless of the weight of the steel. Field application of EonCoat depends on the cost of surface prep and, more specifically, the cost of grit blasting media and local labor. Typical prices for field application can vary significantly with the geometry of the substrate and local conditions, including labor rates.
This information concludes that EonCoat is the lower initial cost solution for mid-to-heavy steel, and Galvanizing is initially less expensive for light steel.
LONG TERM COST
The life cycle cost of galvanizing is low for dry, inland areas because it can last for the life of the asset with no need to re-coat. Essentially the initial cost is the life cycle cost for dry, inland areas. The initial cost of EonCoat is also the life cycle cost. For EonCoat, this is true for even highly corrosive areas – specifically wet and salty environments. This ability to perform well in such diverse environments allows us to offer a 30-year warranty!
The long-term cost for galvanizing is exceptionally high for wet, salty areas. Either the initial application of molten zinc must be increased significantly to accommodate 8 microns-per-year of corrosion; or the galvanizing will have to be repaired at a relatively short interval. The cost of replacing galvanizing on an existing structure is prohibitive. In addition, it would be necessary to disassemble the structure and take it back to the galvanizer. This limitation leaves two uncomfortable options. Either let the structure rust or completely remove the zinc and re-coat with a conventional system.
Removal of the galvanizing is a costly proposition. Partly because it is not easy to blast off the zinc, but also because of the environmental hazards associated with removing galvanizing and the expensive precautions necessary to protect the workers who must do it.
EonCoat is clearly a much less expensive alternative to galvanizing for long-term exposure in wet or salty environments.
DAMAGE TO THE ENVIRONMENT
The US EPA lists zinc as a priority pollutant. Zinc impacts the environment by several routes. First, water is polluted with zinc due to the presence of large quantities of zinc in the wastewater of industrial plants and leaching from large, galvanized structures. The zinc gets into the water supply at levels that are toxic to fish because fish can accumulate zinc in their bodies when they live in zinc-contaminated waterways. When zinc enters the bodies of these fish, it can bio-magnify up the food chain. The zinc in our waterways, and therefore fish supply, can potentially become toxic to humans! Additionally, rivers are depositing zinc-polluted sludge on their banks because of the zinc runoff. Finally, water-soluble zinc that is in soils can contaminate groundwater.
You can also find large quantities of zinc in soils. When the soils of farmland are polluted with zinc, animals will absorb concentrations that damage their health. Zinc cannot only be a threat to cattle but also to plant species. Plants often have a zinc uptake that their systems cannot handle due to the accumulation of zinc in soils. On zinc-rich grounds, only a limited number of plants have a chance of survival. That is why there is not much plant diversity near zinc-disposing facilities. Zinc effects upon plants are a serious threat to the production of farmlands and, therefore, our food chain.
Review this data about the environmental impact of galvanized steel from the folks at Arcelor Mittal- Environmental impact of galvanized steel vs. bare steel per metric ton.
EonCoat, having a low carbon footprint and no toxins, does not cause any of these environmental issues.
HEALTH IMPACTS ON THE WORKFORCE
Zinc is toxic at high exposure levels. As an occupational inhalation injury, zinc can cause metal fume fever. Read more directly from the source:
… the inhalation of zinc oxide can lead to an entity known as “metal fume fever,” which usually occurs secondary to occupational exposure. In these cases, workers who suffer exposure to fumes through welding, alloy production, and soldering of metal can present with flu-like symptoms in addition to cough and dyspnea, presumably due to zinc’s direct effects on the pulmonary epithelium
The process of welding galvanized steel is commonly found in the metal fabricating industry. Many welders usually weld galvanized steel at some point in their career, and in doing so, they may experience galvanize poisoning or metal fume fever. Galvanize poisoning is a condition that results from overexposure to zinc oxide. Symptoms typically begin shortly after exposure to zinc oxide and may include a headache and nausea. A moderate case of exposure will result in symptoms including chills, shaking, a slight fever, vomiting, and cold sweats.
EonCoat contains no toxins, no VOCs, and no HAPs. We engineered all of our products to be water-soluble and inorganic. As a result, EonCoat is nonflammable and has no flashpoint. As a result, it is the safest corrosion coating solution for the workforce and the environment.
Additionally, EonCoat has developed a weldable product with the same safety standards. You can weld over the EonCoat Weldable with no loss of corrosion protection and no risk to the employee. Welding over zinc can create a list of issues – not to mention that some hot-dipped galvanization might contain trace amounts of lead or chromium.
REPAIR TO THE COATING IN CASE OF DAMAGE
Repair of EonCoat is a simple matter. Generally, no surface prep is required – spray more EonCoat on the substrate if any impact has damaged the ceramic. The same is true if an application error occurs and a local spot on the coating and a customer needs to perform a touch-up.
These types of repairs are not possible with galvanizing. Galvanizing must be done in a controlled environment in a specialized facility. No onsite repair is possible. If galvanizing fails or is damaged, the repair procedure must be some other type of coating solution.
ANALYSIS AND CONCLUSION
Considering the extensive protection in severe corrosion environments, easy repair, and the zero environmental and safety impacts of EonCoat appears to be the correct choice for most industrial applications.
Do you have questions about any corrosion prevention challenges unique to you or your customer? Sign Up for our Free E-Book. In 5 short lessons, you’ll learn all about EonCoat.
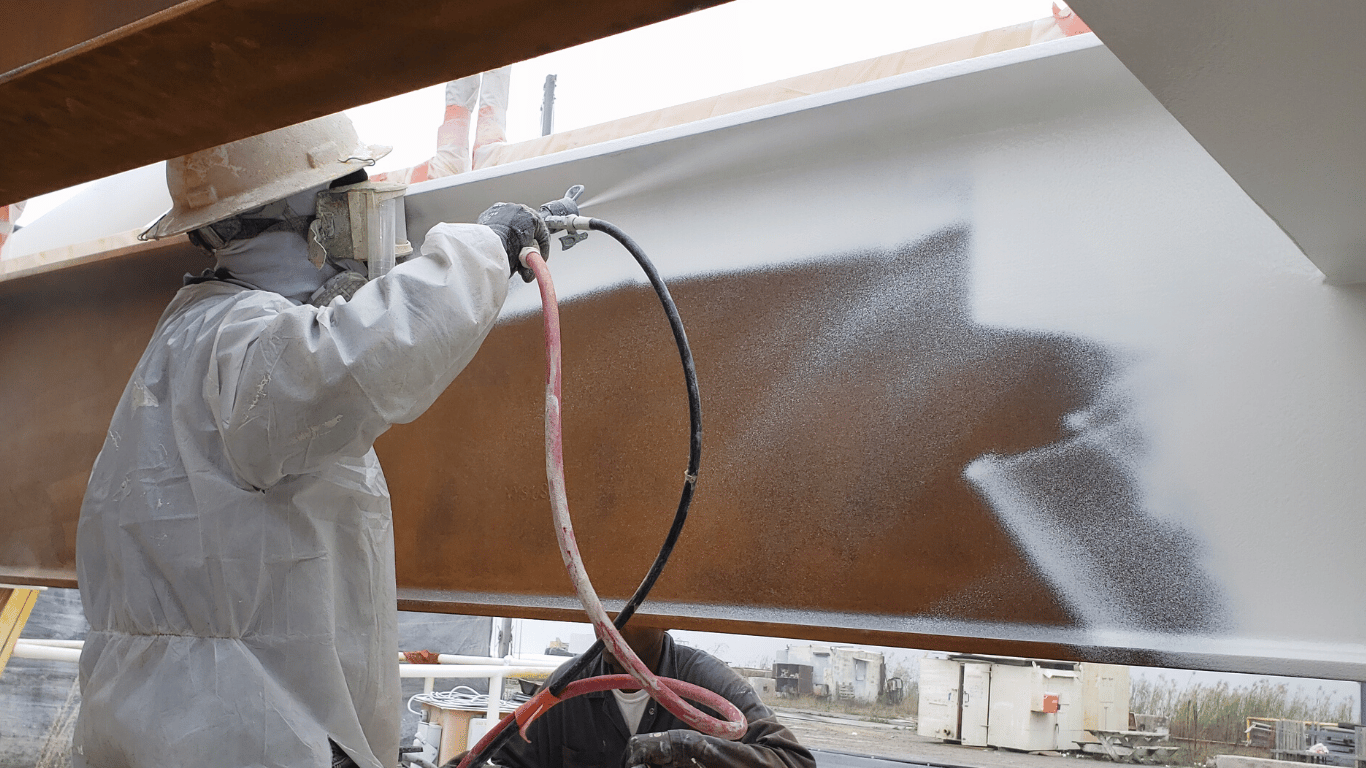
Ready to Learn More About EonCoat?