Can you name the common symptoms of volatile organic compounds (VOC) exposure? [1] Can you explain the long-term health implications of VOC exposure? Does your company track both short- and long-term VOC worker compensation claims? If a company values its front-line employees – the folks in steel-toe boots – the answer to the questions above and so many others need to be a resounding, “Yes!”
According to the National Institute of Health (NIH), handling chemicals, working in inadequately ventilated areas, or entering areas of exposure with improper or no protective equipment is generally recognized as the reasons for occupational inhalation injuries[2]?
I’ll share more about this later, but first, I want to share some reflections and personal examples – because employee injury prevention is just that – personal.
I’ve worked in the manufacturing and energy industries at various senior levels for a long time. In my opinion, educated folks who enter the workforce at the management level are often indifferent, or even disinterested, about the safety of the front-line people. It isn’t that the educated-but-never-worked-the-front-line people don’t practice or enforce good safety policies. That same person may be stricter than someone who has come up through the ranks of hands-on trained managers. But I can tell from talking with them that safety is frequently a numbers game. If the numbers are inside the proper measures, the job must be going well. It has been my experience that the person who hasn’t worked the front line doesn’t take worker safety personally. I state emphatically, worker safety is 100% personal!
Personal Experiences Make Worker Safety Personal
I have noticed that the people who came up through the hands-on-trained ranks view and feel safety differently. I have seen the pain on their faces when they realize they have exposed one of their people (and they do see them as “their people”) to danger. It is very personal. An easy way to make one of the up-through-the ranks folks angry is to look at an exposure event as a number. I recall a great engineering manager at a paper mill, Ken Johnson. Ken nearly threw a guy out of his office after that person offered an expedient but dangerous solution to removing asbestos from a hot environment on a steam line. I never respected Ken more, and I never forgot that lesson. Ken was one of those high-level guys who started at the bottom. He was tough as nails, but he cared about “his people” and was labor’s best friend. I wish there were more people like him.
I’m a hybrid person. I have an Engineering Degree from Georgia Tech, and my first role out of college was in a supervisory role. However, I worked my way through school as a construction boilermaker; and after all this time, I still identify as one. The people on that crew taught me so much, and I am forever grateful. Working with that boilermaker crew shaped my thoughts about safety and is still a foundation for worker safety, whether I am manufacturing products or creating processes.
The behavior that used to anger us all was when management appeared to care about whether we were following the safety rules instead of whether or not we got hurt on the job. I felt like management would let us walk under a 200-ton suspended load if we wore our hard hats and safety glasses. I always imagined being crushed, with the bill of my hard hat and steel toes sticking out from under the load.
I remember Warren, a young plant engineer, looking underneath a turning gear to see why it was sticking. The scary part is that he was underneath the equipment while it was suspended with a come-a-long. Come-a-longs were notorious for slipping a link, and this one did just that while Warren had his head under the load. The entire thing dropped about two inches. I was fortunate enough to catch Warren as he fell. He was knocked unconscious and had a knot on his head the size of an egg. When his boss saw him, the first question asked was, “Were you wearing your hard hat.” I’m confident the first question should have been, “Are you OK?”
The underlying assumption about the question was if the employee followed the rules. Front line employees following rules and regulations can impact the perception of how the boss is doing his job. In some way, an injury could have a negative impact on the perception of management.
Those are just two experiences that shaped the engineer and manager I became. Once in a power plant in Iowa, I found two of “my people” working on a rickety scaffold. I immediately had them come down from the scaffold, and I began to look for the foreman. The foreman’s response was, “We didn’t build that scaffold. The power plant did, and it has their tag on it.” I’m sure that is the angriest I have ever been while standing on a turbine deck. I instructed the foreman to go into my office and not come out until he had written what we would say to the families of those two men at their funerals. I told him to specifically include “the part about how we didn’t build the scaffold. The families will really care about that.” A short time later, I found that foreman crying in my office. Finally, he got the message – we are responsible for the people we lead.
Today’s workplace is so much safer than the one in which I began those many years ago. I’m glad to see safety improvements. I’m grateful to the people who continue to work hard to change the workplace safety environment. I may have made fun of Ralph Nader and his zest for employee safety and wellness when I was young, but I now realize he was right, and I was wrong.
There Is Still So Much Room For Improvement
We need a sense of urgency about exposing painters and applicators to VOCs. Some of the VOCs to which workers are exposed are “mutagenic, genotoxic, neurotoxic, and carcinogenic. Studies have shown that exposure to VOCs increases the risks of developing a respiratory illness, leukemia, birth defects, neurocognitive impairment, and cancer in humans. [3]The alarming physical signs and symptoms of Acute Inhalation Injury (AII) are well documented[4]. The long-term effects are varied and can evolve from respiratory issues to systemic problems, including death. The most concerning problem is that these chronic health issues may not become clinically evident for years. The delayed manifestation of symptoms allows corporate cultures to maintain plausible deniability up to 15 years later. Does popcorn lung ring any bells? It should.
The NIH estimates that between 5% – 6% of workers affected by an inhalation injury will develop various chronic complications. For example, “carbon monoxide (CO) poisoning is associated with an increased risk of mortality even at long-term follow-up (median of 7.6 years)[5].”
What’s the worst part of this? In 2022, we have no excuses. Years ago, we did not know how much damage was caused by inhaled VOCs, HAPS, and toxins. We didn’t have an excellent way to protect both our front-line employees and our carbon steel assets. EonCoat has flipped this paradigm on its head. You can both protect your workers and your assets!
As far back as 2013, NASA told us the single most effective carbon steel protective coating is also safe for employees and environmentally friendly. We have invested time and money to make EonCoat both available and cost-effective. As more companies use EonCoat’s patented permanent corrosion protection, more employees are protected.
This brings me back to my original question – how do we measure compassion toward front line employees? Globally, we must move to a place where those front-line, steel-toe-boot-wearing folks are valued and no longer exposed to an uncertain future that could include cancer, chronic obstructive pulmonary disease, or even death. We must move toward an applicator workplace environment that has a zero tolerance for preventable inhalation injuries. A new, industry-wide standard should be that an applicator work environment must contains NO VOCs, NO TOXINS, AND NO HAPS.
If there are managers who cannot flip the script and focus on employee safety – they need to go!
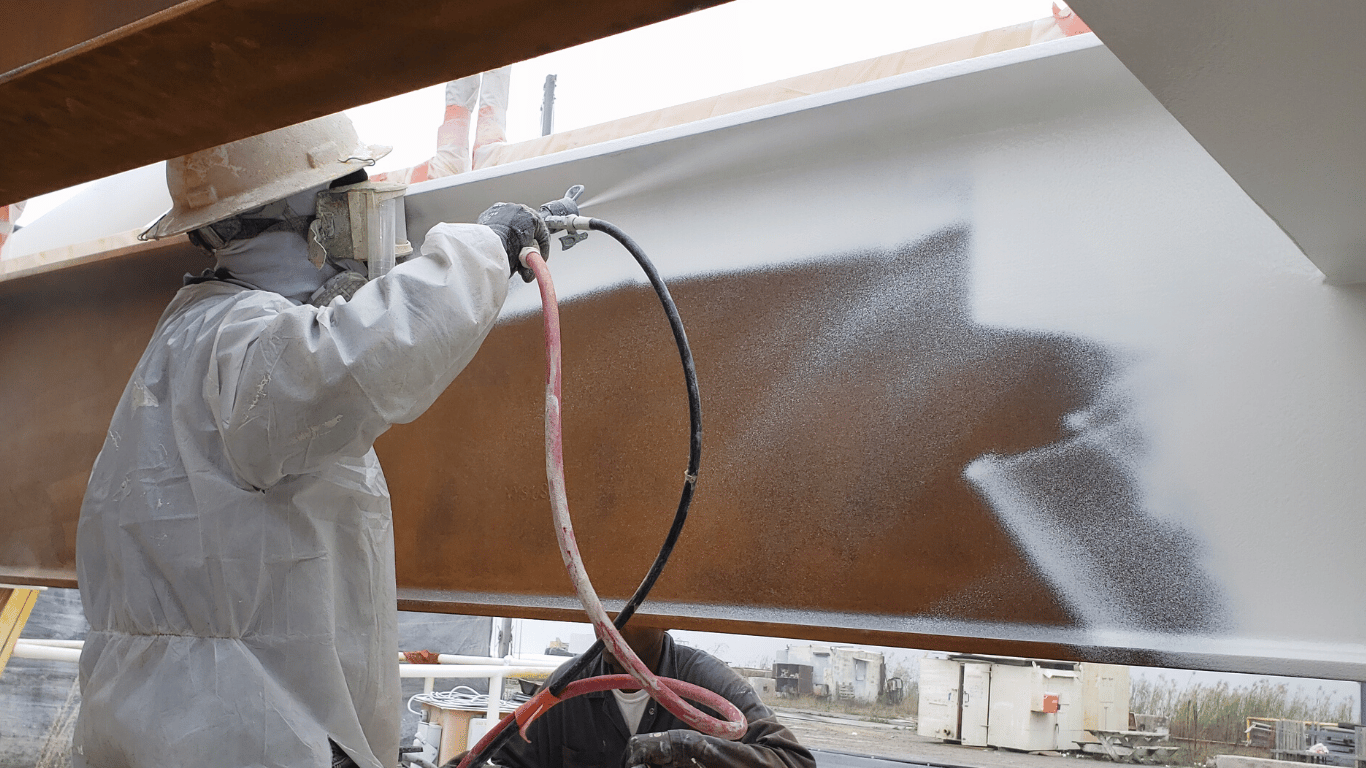
Ready to Learn More About EonCoat?