One of the most common questions we get about EonCoat is the amount of surface preparation required for a specific substrate. We’re happy to answer these questions, especially because EonCoat usually saves contractors time and money during the surface prep process! 🙂
EonCoat saves contractors money on the application side since it only requires one coat and saves contractors time on the surface preparation side. The recommended surface preparations for EonCoat are equal to or in most cases, less time-intensive than leading corrosion/abrasion coating competitors.
Below, we’ve listed some of the most common surfaces used for EonCoat and the amount of preparation required for EonCoat to fully bond with the substrate:
*Note: Visit the SSPC or NACE websites for more information about their standards.
Minimum Surface Prep by Substrate
- Iron & Steel: SSPC-SP14/NACE 8
- Previously painted: SSPC-SP6/NACE 3 (primer recommended)
- Concrete: SSPC-SP13/NACE 6
Surface Prep by Condition:
- White metal blast (new/mill scale): SSPC-SP 5/NACE 1
- Near white metal (new or unused with rust over mill scale): SSPC-SP10/NACE 2
- Commercial blast (in-service or previously coated): SSPC-SP6/NACE 3
- Brush-off blast (even layer of rust/oxide): SSPC-SP7/NACE 4
- High pressure water jet (previously painted, loose rust or debris): SSPC-SP12/NACE 5
- Concrete (all surface conditions): SSPC-SP13/NACE 6
- Industrial blast cleaning (used, in-service, or previously coated): SSPC-SP14/NACE 8
Do you have questions about the above? Let us know in the comments or on Twitter @Eonoat. The information above was drawn from our EonCoat product data sheet. Want to know more about Eoncoat? Download the EonCoat product data sheet.
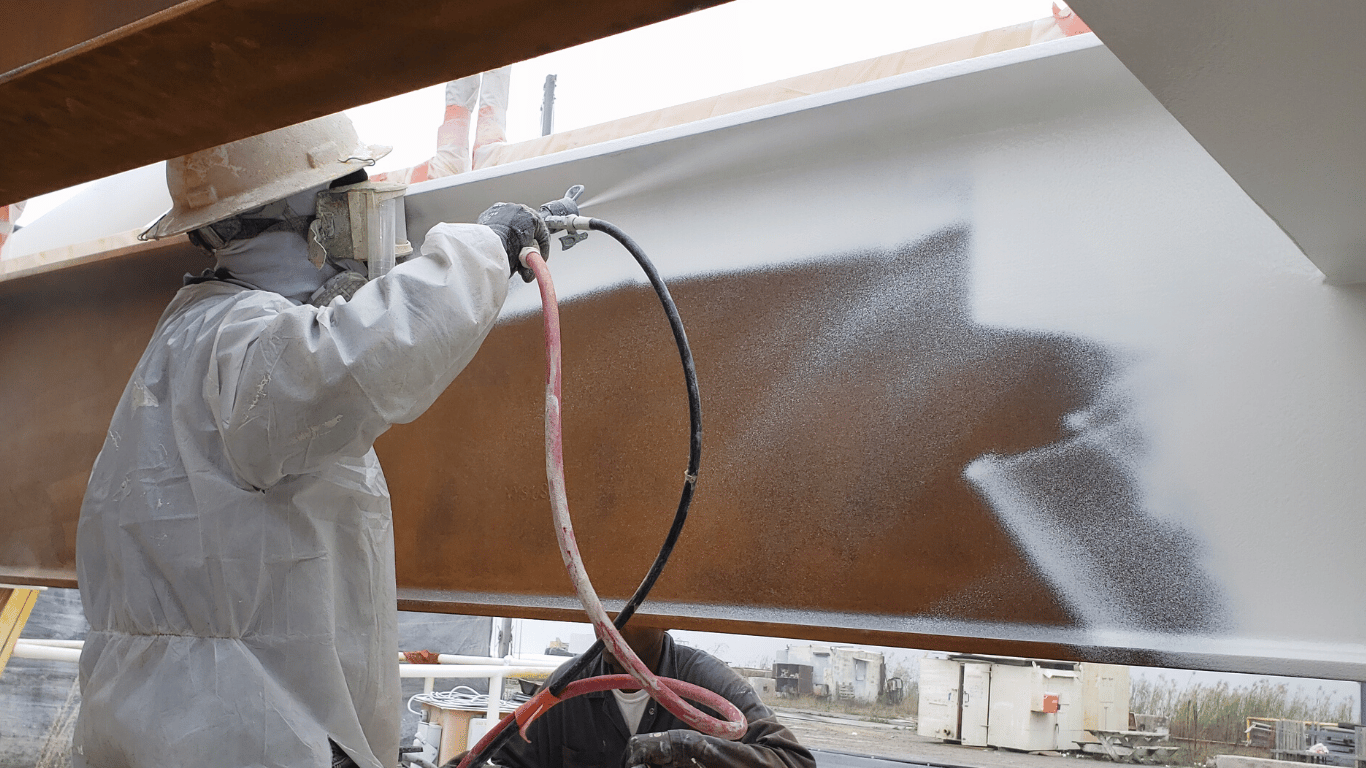
Ready to Learn More About EonCoat?