For folks interested in corrosion resistant coatings, the Corrosion Test Chamber is where all of the action happens. Here at EonCoat, we run a variety of corrosion tests using different substrates and corrosive additives to determine their effects on our coatings.
The scientists at EonCoat recently added a live web cam of EonCoat’s corrosion test chamber. Click on the video to your right or follow the link to view the live feed of the current test which we will cover in a blog next week as it compares 15 industry competitors: EonCoat Corrosion Test Chamber
45 Day Salt Water Test
A 45 day corrosion test was run in late 2010 to determine how EonCoat reacted under extreme saltwater conditions. The test pitted EonCoat against a leading commercial brand of corrosion resistant coating. Each coating was subjected to 12 hours under a seawater spray followed by 12 hours of intense multi-spectrum light for the duration of the test. As you can see from the images below, EonCoat held up for the 45 days while the leading commercial brand corroded at a much higher rate.
The EonCoat Difference The difference between EonCoat and the leading commercial brand is the way in which EonCoat binds with the substrate. EonCoat works by turning the service of the substrate into a complex of stable oxides. EonCoat then builds a ceramic layer on top of the new stable surface. The resulting ceramic layer is extremely tough (170 Wear Index; 400 wear cycles/min) and corrosion resistant (5x more resistant than leading corrosion paints). Since chemical bonding occurs (EonCoat does not sit on top of the substrate like normal polymer paints), corrosion promoters like oxygen cannot get behind the coating.
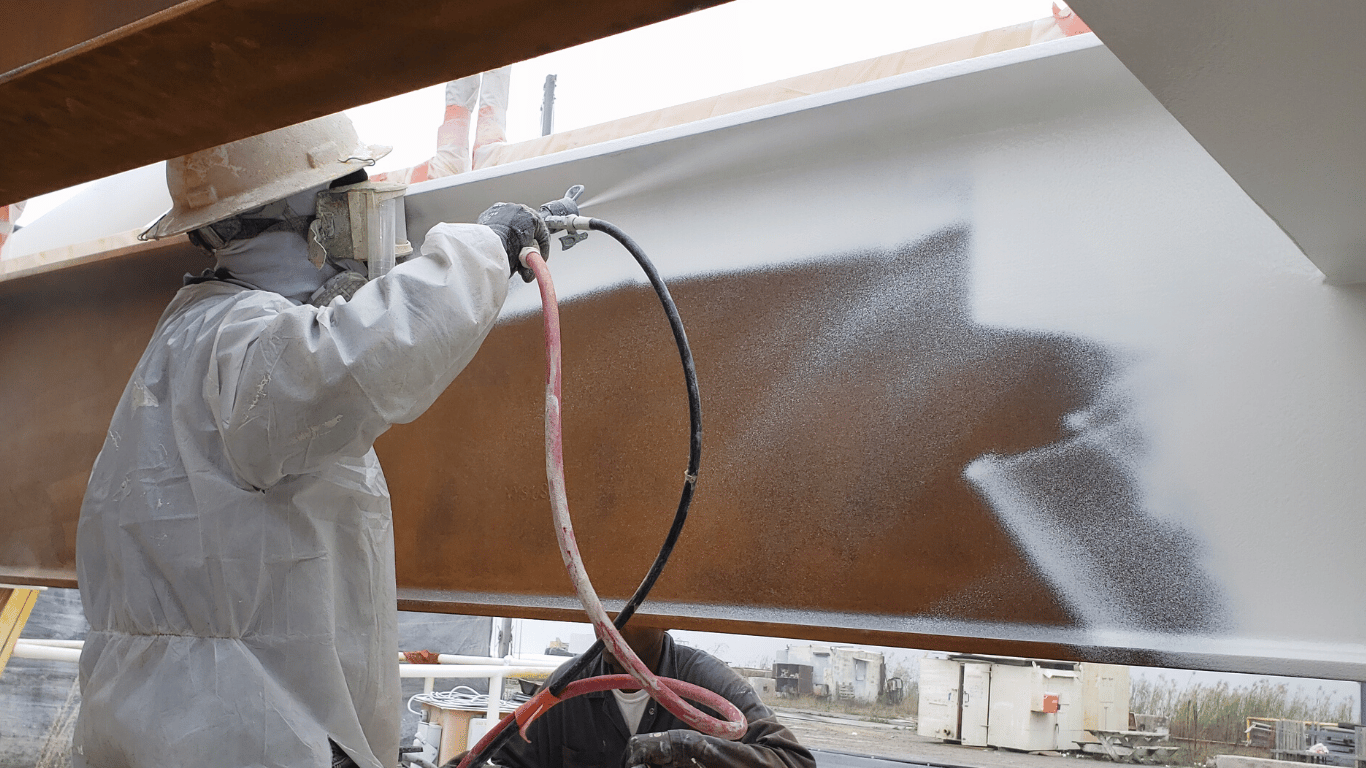
Ready to Learn More About EonCoat?