When it comes to choosing an anti-corrosion method, budget is a crucial consideration. If your business is in oil and gas, petrochemical, industrial or infrastructure, you are likely under immense pressure to preserve a positive cash flow. Protecting your carbon steel assets from corrosion in the most cost-effective way possible.
If you want to get the most value out of your investment, you must consider more than just the price of the protective product itself. With any anti-corrosion solution, there are also costs associated with surface preparation, application, and continuing maintenance. With so many variables to factor in, it can be difficult to compare the return on investment of two different methods.
We’ve created a guide to help companies compare the costs and value of two of the most common anti-corrosion solutions for the oil and gas industry: Thermal Sprayed Aluminum (TSA) and EonCoat®.
Choosing Your Corrosion Prevention Solution
On closer inspection, most companies find that conventional options like Thermal Sprayed Aluminum have higher overall costs than initially anticipated.
The most cost-effective option is one that comes with minimal downtime, minimal labor, and no continuing reapplication costs.
EonCoat® has been carefully formulated to give you an all-in-one solution for corrosion defense with a high return on investment. Where TSA requires extensive surface preparation and has a labor-intensive application process, EonCoat® requires only a NACE-3/SSPC SP-6 and can be applied with little downtime — minimizing your initial costs.
EonCoat® not only allows your company to achieve reduced time, labor, and interruption, it also lowers the costs of ongoing maintenance for your assets. Because EonCoat’s dual-layer formula chemically bonds to steel and is self-healing, there is no need to reapply.
Read our infographic below to compare EonCoat® and TSA side-by-side, and discover how EonCoat’s unique formula can save your company time and money in the long-term.
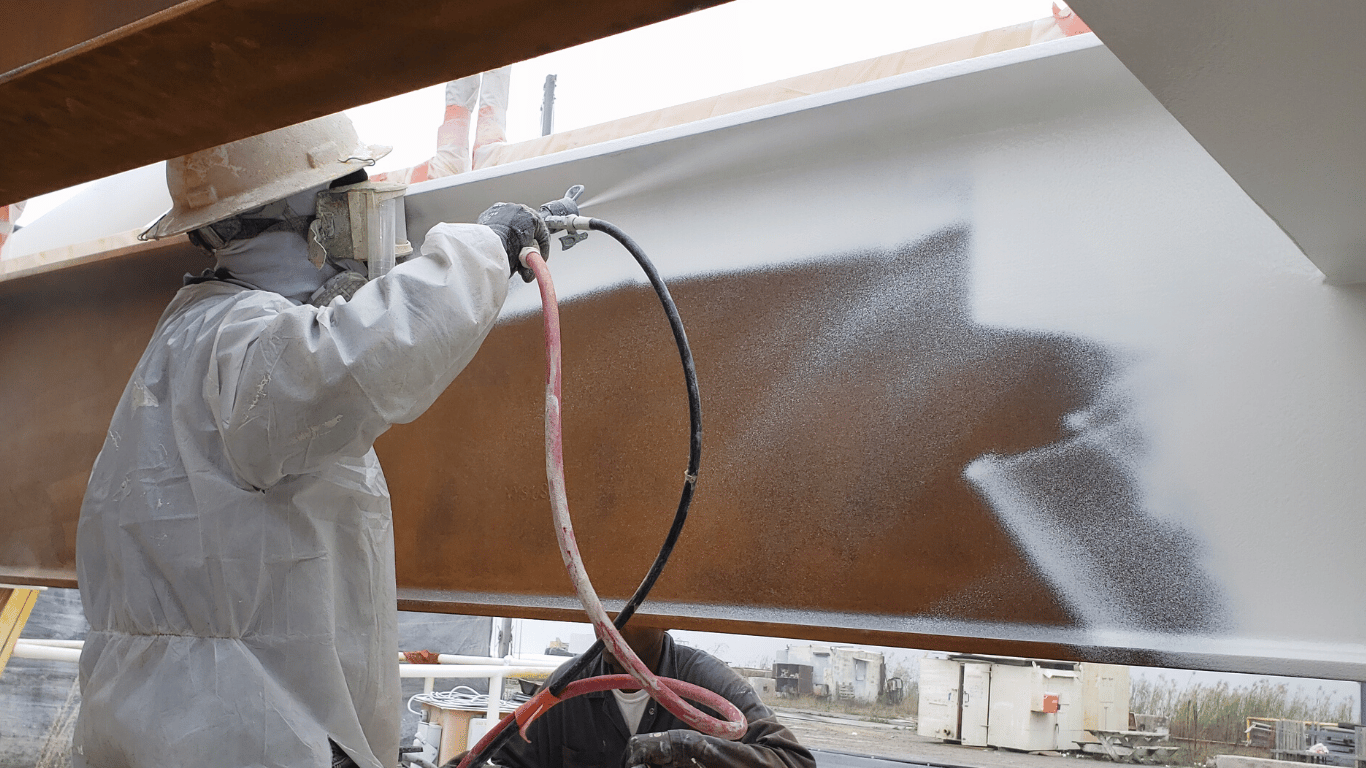
Ready to Learn More About EonCoat?