This post is a little different than what you are used to. This is a letter written to us by Joe Cucci, CEO of Corrosion Solution Unlimited. He explains his excitement of EonCoat.
His Writing
Polymer coating technologies (alkyd oils, epoxies, urethanes…) have long been the standard choice for providing corrosion protection to steel and concrete structures We would like to change that concept by categorizing EonCoat Corrosion Protection Coating as a Surface Engineered Treatment.
Surface treatments like, thermal spraying, plating, and laser alloying are usually not a viable option for large-scale applications. The size of the articles and transportation costs makes most surface treatments impractical as large objects, like tanks, cannot easily be transported to a new site. And as we know, surface treatments, like thermal spraying cannot be field applied.
Galvanizing (Zinc) has proven toxic in the welding process, has a toxic chemical reaction with organics (highly problematic for the food industry), and the wastewater is strictly monitored at the process site.
This is why EonCoat has been accepted as the new standard and is the more “sustainable choice.”
EonCoat alloys the surface of steel 20 Microns deep, in the range of a gold plated ring.
EonCoat’s regimen of testing has demonstrated this alloyed passivation layer is amorphous (continuous), permanently separating the steel surface from corrosion-promoting elements in the atmosphere. EonCoat will protect the steel beyond that of a polymer coating as alloying the surface is more effective than coating it. With an alloyed surface, there is no greenhouse effect or spot migration. Because the coating cannot peel away from the surface, it’s not possible for water to get trapped under the coating. And repeated tests have shown that with EonCoat, there is no spot migration, meaning that a spot of rust will not grow and spread.
This alloyed layer is protected by a chemically bonded inorganic ceramic. Because EonCoat does not have carbon atoms and is totally inorganic, it lasts longer. It ages much slower than organic materials and does not break down the way carbon atoms do. Because it’s inorganic, there is no off-gassing or noxious fume released as a result of grinding or cutting steel coated with EonCoat making it much safer for workers, especially those working in confined spaces.
Typically self- fired ceramics fall short on impact and aesthetics as compared to polymers, but good wear resistance, fireproofing and zero flames spread ceramics provide needed benefits. As a paint-ready surface, EonCoat®, a one-coat primer/finish, can be top-coated with any color or gloss to satisfy your needs, allowing you to get the look you desire with the durability and fireproofing needed.
EonCoat has put its product to the test in accredited labs and testing facilities and backs its performance with a 30-year warranty.
Eco-Friendly Surface Engineering, EonCoat’s paving the way with Self-Fired Ceramics!
Joe Cucci
Corrosion Solutions Unlimited
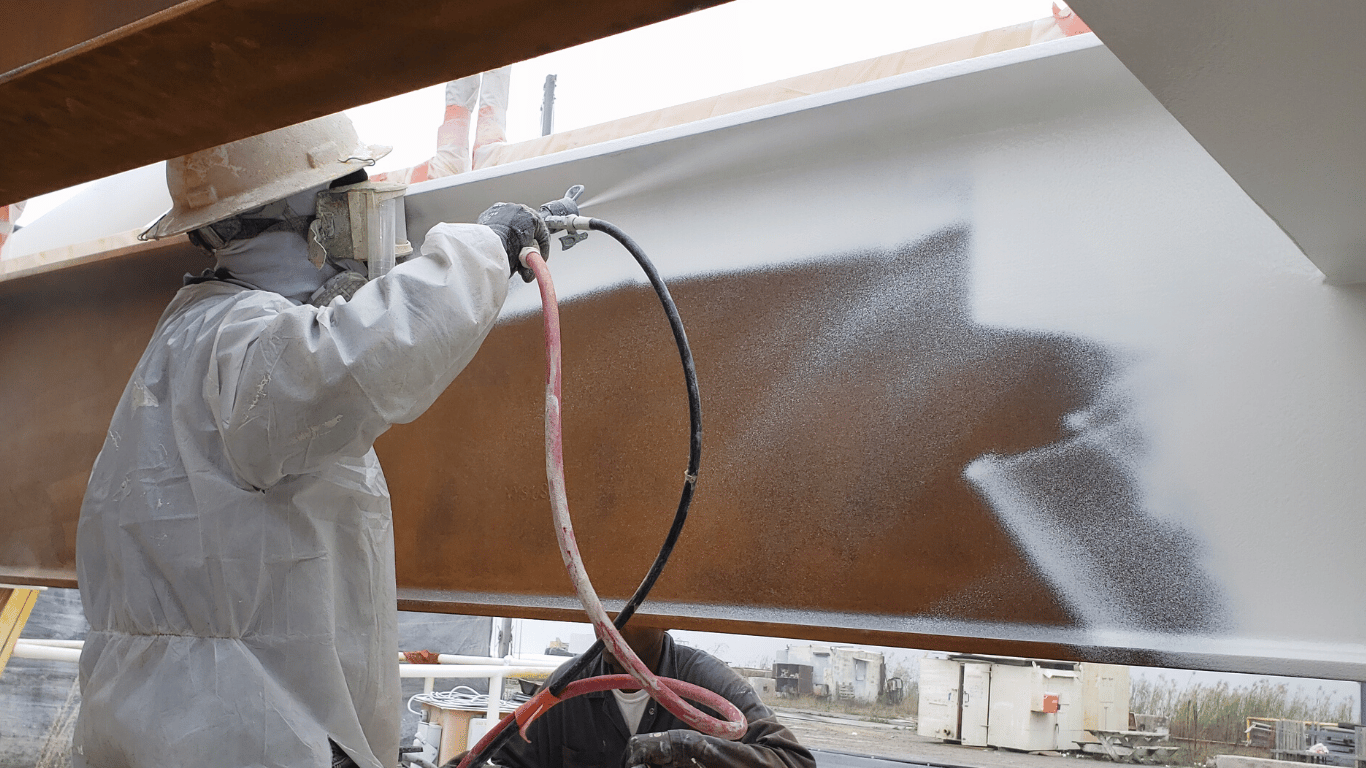
Ready to Learn More About EonCoat?