Is Carbon Capture New?
While Carbon Capture Utilization and Storage (CCS / CCUS) seemingly came onto the energy scene recently, the history of this technology goes as far back as 50 years. That was the last time the United States faced a significant energy crisis. The sense of urgency for affordable energy in the 1970s led engineers to discover that mature oil fields experience increased production due to being injected with carbon dioxide.
The goal is to manage environmental conditions through carbon capture, utilization of some carbon dioxide to advanced materials for re-engineering, and sequestration.
What is the Current Status of CCUS?
With the growing focus on the global reduction of greenhouse gases, CCUS has returned to the forefront of dialogue in the environmental, oil and gas, and petrochemical industries.
Between December 2020 and September 2021, CCS experienced a 48% growth. The Global CCS Institute cites,
“Despite unprecedented growth in the CCS project pipeline for the last 12 months, there remains a massive gap between today’s CCS fleet and what is required to reduce global anthropogenic emissions to net zero. Limiting global warming to 2°C requires installed CCS capacity to increase from around 40 Mtpa today to over 5,600 Mtpa by 2050. Between USD$655 billion and USD$1,280 billion in capital investment is needed to 2050.”
See the two maps below for a visual representation of where the CCUS industry is growing.
Image Extracted From (Globalccsinstitute.com)
Image Extracted From (Catf.us)
Carbon Capture Science
Let’s boil down the science of CCS/CCUS to its three basic steps.
First, we must capture the carbon dioxide that has been produced. Some techniques position the capture to occur near the point of carbon production. Still, others are positioned further from the initial production site and are referred to as Direct Air Capture (DAC). It is anticipated that DAC will be capable of capturing harder-to-target carbon production from “industries such as aerospace, maritime, rail and trucking.”
The second step is transporting the captured carbon gas. Transportation can be done via pipeline, truck, railway, or boat.
The final step, storage, will result in a portion of the CO2 injected into strategic underground sequestration points. Not only will this step remove the CO2 from the atmosphere, but it will help bring old oil fields more productivity. When the CO2 is pumped underground, the oil beneath the surface rises to the point of being more easily removed. Increasing the reservoir pressure and miscibility by injecting carbon dioxide is called enhanced oil recovery (EOR). EOR accounts for 88% of the current C02 raw material market.
Since Aramco began using CCS in the Uthmaniyah oil reservoir in 2015, oil production has doubled for all four wells. Considering the feasibility of utilizing oil wells already being worked, the production increase alone is an amazing return on investment.
What Advanced Materials Can CCUS Aid?
CCUS has multiple options, as seen in the graph below. In the geological option, C02 is the feedstock, and crude oil is the product. In contrast, CO2 can also be feedstock and converted for other chemical, biological, and mineralization options.
Image Extracted from (Clearpath.org)
Corrosion in the Carbon Capture Utilization Sequestration Process
Because of the pH balance, the temperature of pressurized C02, and the presence of water and other impurities, corrosive attacks will happen in the CCS / CCUS process. We must build corrosion protection of carbon steel into the entire process. While cathodic protection can be used in some instances, corrosion-resistant coatings must be applied wherever possible.
Simply replacing incorrectly or unprotected corroded carbon steel with more carbon steel is inconsistent with the environmental protections we are collectively trying to achieve.
According to Gary Coates, the Technical Manager at the Nickel Institute, “If C02 is dry, it is non-corrosive, and it is a matter of economically transporting it to a storage site … Dry C02, then, can be channeled, stored, and transported using traditional carbon steel”. That carbon steel needs an anti-corrosion coating.
How Does EonCoat Help in Carbon Capture Utilization and Storage?
Let’s start with the obvious reasons that CCS/CCUS is becoming such a common topic of conversation:
- removing excess carbon dioxide from the environment,
- while also increasing production of already existing oil fields,
- and supplying C02 as feedstock for advanced materials,
is a win-win-win. We need to take it one step further and make it a win-win-win-win. That is where you can utilize EonCoat with confidence.
If you want to be environmentally friendly, then you need to use a carbon steel protection coating that is also environmentally friendly. EonCoat has:
- NO VOCs
- NO HAPs
- NO Toxins
- NO Odor
Additionally, EonCoat is:
- NON-Flammable
- Water-based
- Inorganic
Our Scientists and Engineers specifically engineered EonCoat with a safety focus. The applicator is safe using EonCoat, and the only PPE requirement is an N95 mask and safety goggles. The environment is safe because no solvents are required to clean up after an EonCoat application – only water is required. Any remaining EonCoat can easily be disposed of in the same manner as any cementitious product.
All these benefits add up to one coating application for two layers of protective coatings. Part A (acid) and Part B (base) mix and then atomize just prior to making contact with the carbon steel substrate. The process forms a chemically bonded phosphate ceramic that prevents corrosion on carbon steel.
What’s The Next Step For CCS/CCUS Professionals?
Whether your CCS/CCUS is onshore or offshore, EonCoat has the protective coating and experience you need to succeed. If you’re curious about how EonCoat performed in one of the most corrosive atmospheric environments, look at the results from NASA. EonCoat scored the first perfect 10!
If you’re ready to engage with an EonCoat specialist about your unique coating needs, feel free to click the Contact Us button below. If you want to continue to learn more about the EonCoat family of products and the science behind them, download our Free E-Book. You’ll receive one email daily for five days and be on your journey as an EonCoat expert.
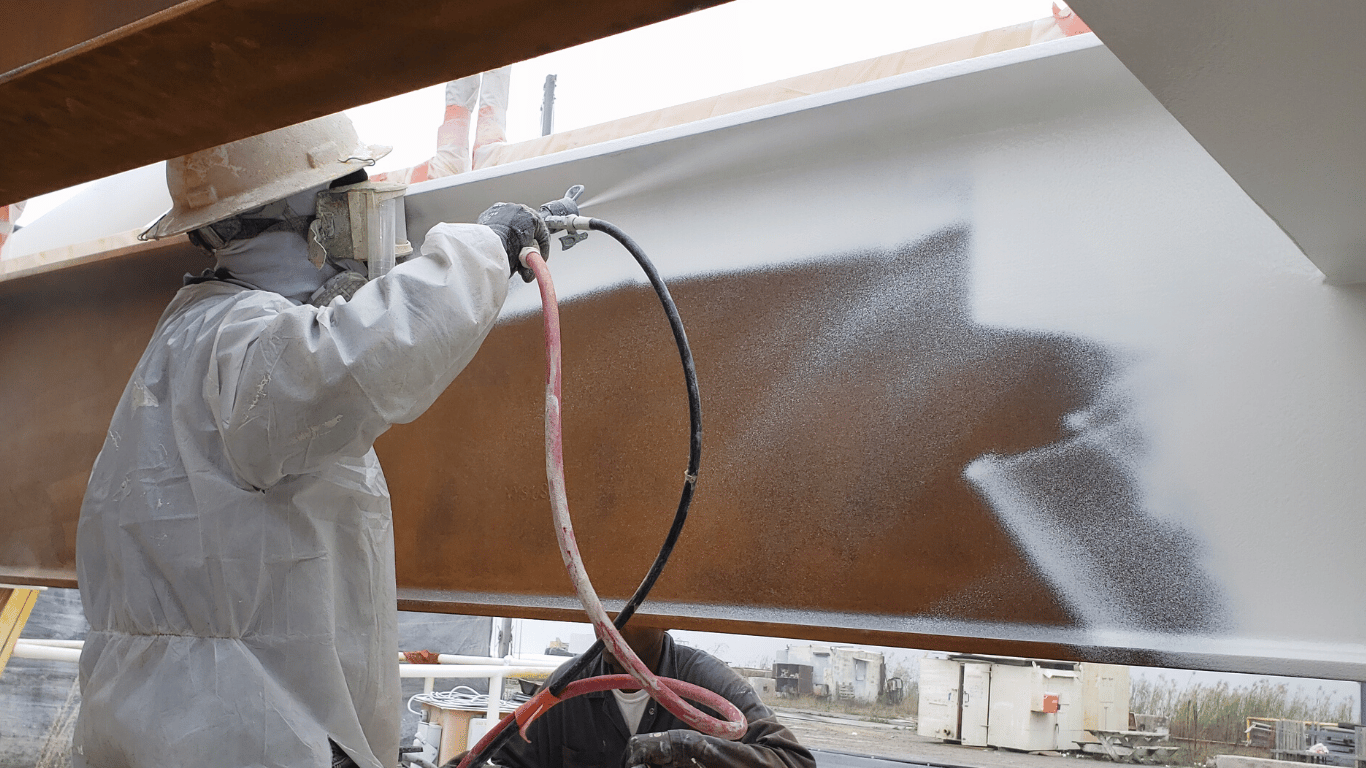
Ready to Learn More About EonCoat?