Carbon steel is widely used across industries such as energy, industrial, infrastructure, heavy equipment, and marine. Unfortunately, carbon steel is highly susceptible to corrosion, which can put major holds on workflow and production, costing organizations significant amounts of time and money. The first step to battling corrosion is understanding it. There are many different types of corrosion that are visible to the naked eye: uniform corrosion, pitting, crevice corrosion, filiform corrosion, galvanic corrosion, environmental cracking, and fretting corrosion, to name a few. Let’s review how these types of corrosion occur, and how they can damage carbon steel.
Uniform Corrosion
Uniform corrosion is the most common variant of corrosion. This corrosion occurs naturally when carbon steel deteriorates through a chemical or electrochemical reaction with the surrounding environment that deteriorates the entire surface, corroding it ‘uniformly.’ This type of corrosion is the most widespread, but is predictable and can be managed by using the appropriate preventative measures.
Localized Corrosion
Localized corrosion comes in many variations, such as pitting, crevice corrosion, and filiform corrosion.
- Pitting corrosion: This type of corrosion happens when a small break in the metal forms. The subsequent hole or cavity becomes anodic, while the surrounding metal becomes cathodic. This produces a localized galvanic reaction, leading to the structural failure of the metal. Pitting is difficult to locate and manage, as it is often masked by other materials produced during the formation of corrosion.
- Crevice corrosion: This localized corrosion can often be found under gaskets, clamps, and other unmoving areas where low oxygen and acidic conditions can lead to corrosion within crevices.
- Filiform corrosion: This corrosion occurs under surfaces that have been painted or coated. Defects in the paint or coating allow water to intrude, thereby causing corrosion below the protective layer, resulting in a weakened structure.
Galvanic Corrosion
Galvanic corrosion is the result of a very specific set of conditions. It is only found in environments where there are electrochemically dissimilar metals in electrical contact that are also exposed to an electrolyte. This corrosion happens when galvanic coupling occurs between the anodic and cathodic metals. The anode corrodes faster by being coupled, while the cathode deteriorates more slowly.
Environmental Cracking
This corrosion process occurs when environmental conditions arise that negatively affect carbon steel. Chemicals, stress, and temperatures can create conditions that produce stress corrosion cracking (SCC), corrosion fatigue, liquid metal embrittlement, and hydrogen-induced cracking.
Flow-Assisted and Intergranular Corrosion
Flow-assisted corrosion occurs when the protective oxide layer is dissolved over time by the flow of wind or water. This corrosion exposes the oxide on the surface of the metal, exposing subsequent layers to further corrosion.
Intergranular corrosion attacks the grain boundaries of metal, often as a result of metal impurities. Impurities are frequently present in higher concentrations near these grain boundaries, making them more susceptible to this type of corrosion.
Fretting Corrosion
This type of corrosion occurs as repeated weight, vibration, or wearing causes pits and grooves on the surface of the metal. This occurs most often in machinery parts in motion, or surfaces that suffer vibration as they are transported from place to place.
High-Temperature Corrosion
High-temperature corrosion can occur from oxidization, sulfidation, or carbonization, or from fuels that contain vanadium. Sulfates can also form corrosive compounds that will attack carbon steel which is normally resistant to high temperatures and corrosion.
Soil Corrosion
Soil corrosion is seen when carbon steel is exposed to moisture and oxygen in the surrounding soil. Soils with high moisture content, high electrical conductivity, high acidity, and high dissolved salts are the most corrosive.
Because carbon steel accounts for approximately 85% of total steel production worldwide, it becomes necessary to be knowledgeable about the things that cause it harm. Efforts to understand and manage carbon steel corrosion can help mitigate and assuage the high costs associated with this common concern.
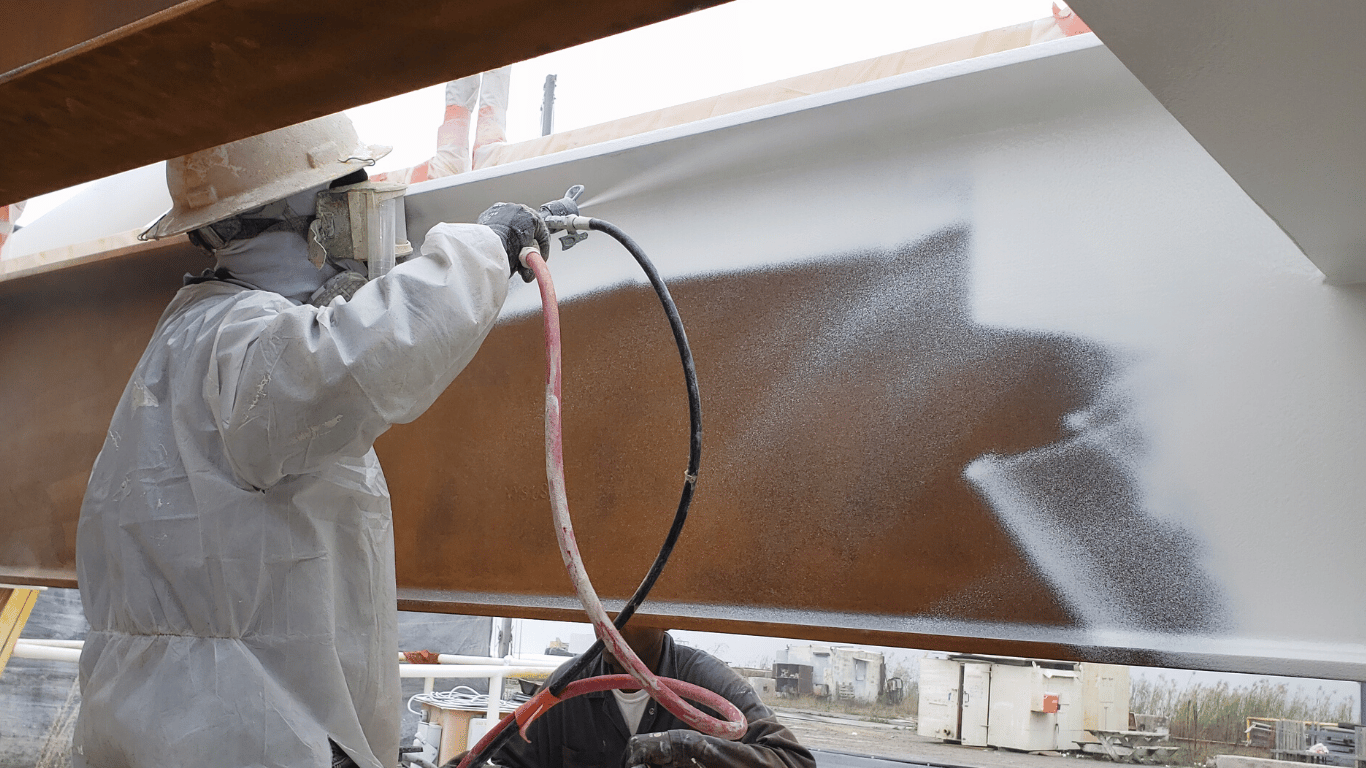
Ready to Learn More About EonCoat?