The soil-facing side of a tank bottom is highly susceptible to corrosion while also being the hardest to protect from corrosion. So, let’s take a closer look at why both parts of that prior sentence are true, the current options, and what the future holds for this distinct industry.
Let’s start by reviewing some of the language specific to tanks and tank bottoms, also known as the tank floor. The soil-facing side of tank bottoms is unique to aboveground storage tanks (AST). ASTs are defined as a container that holds 55 gallons or more.
The large tanks we are talking about are divided into two groups. One group is larger, field-constructed, or field-erected tanks. The second grouping is smaller, shop-built, bulk storage containers. These containers can be on, partially in, or completely off the ground.
For this blog, we will focus on the large tanks with a soil-facing side of the tank bottom, flat bottom reservoir tanks, and API 620 low-pressure liquid storage tanks. Those specific ASTs, also referred to as bulk liquid storage tanks, are some of the largest diameter tanks in the industry. In addition, many of these ASTs frequently house petroleum or other petrochemicals.
For a perspective of the market size, in 2020, the global market for aboveground storage tanks (AST) was $3.15 billion. North America has the lion’s share of this market, approximately 35%. Europe and Australia share approximately 24% of the AST market. The AST market is predicted to have significant growth in the future.
Now that we’re together on the basics, let’s take a look at the immediate challenges. First, why is the soil-facing side of the tank bottom susceptible to corrosion? Then, let’s explore the inherent issues with protecting the tank bottoms.
Why Is The Soil Facing Side Of The Tank Bottom Susceptible to Corrosion?
The soil-facing side of a tank bottom is susceptible to soil side corrosion simply because of how the storage tank bottoms are engineered. Because of the complexities of tank engineering design, the issues with tank bottoms cannot be eliminated. The susceptibility to corrosion comes directly from the following:
- It sits directly on the ground or the mandated spill containment apparatus.
- Tank owners typically leave the carbon steel untreated, allowing oxygen, moisture, and salt from the atmosphere and underside soil to be in contact with the substrate.
- The soil has moisture that creates ongoing corrosion opportunities.
- Microbial Induced Corrosion (MIC) speeds up the corrosion process any time carbon steel is present in soils, seawater, fresh water, and many other environments.
What Is the Current Plan For The Soil Facing Side of the Tank Bottom?
A typical AST has a life expectancy of 25 to 40 years. However, currently, most tank owners do not apply any corrosion protection to the soil-facing side of a steel storage tank bottom. Because of this, and with no protective coating on the tank bottoms’ soil-facing side, the tank bottom’s life expectancy is reduced to 15 years.
Instead, the current trend is to simply double the thickness of the soil-facing side and replace the tank bottoms when the steel becomes too thin. Unfortunately, doubling the thickness also doubles the price. While this tactic may slow down the corrosion, it doesn’t prevent corrosion and may not even increase the total years the asset is in service.
A three-coat paint system will not work on the soil-facing side of the tank bottom plate. Mechanically, the paint lays on the carbon steel and is not resistant to the heat of the welding process, causing any paint to burn off. The paint burn-off is one of the reasons the welds are typically the first place an inspector will notice the corrosion. After that, the corrosion keeps creeping from there.
Monitoring the status of the soil-facing side of the tank bottom via a cathodic protection system is federally mandated in certain instances. However, as a corrosion protection mechanism, the shortcoming with the large tanks is apparent. The bigger tanks have such a large diameter that the current flow cannot be consistently maintained.
The other option of draining, cleaning, degassing, inspecting, repairing, and returning to service costs the tank owner. Those costs are not only for the expenditures of such practices but are also tied to vast amounts of lost production opportunities. While there is a time and place for a complete drain-to-inspect process, reducing that frequency by having intact, permanent corrosion protection on the soil facing side of the tank bottom pays off financially and with peace of mind.
While we are talking about the high cost of monitoring, please hear us clearly – not monitoring is not an option – because the risk of a product spill is the most unacceptable cost.
So, if the “do nothing and wait for the corrosion” isn’t working, what is the next best step? Keep reading for the highlight reel of EonCoat Weldable Corrosion Protection.
What’s So Different About EonCoat’s Weldable Corrosion Protection?
All of the inherent challenges we just outlined and an outpouring of demand for better corrosion protection on the soil-facing side of the tank bottom led Sameer Patel, EonCoat’s Lead Chemist, to develop EonCoat’s Weldable Corrosion Protection. Honeywell International’s plant in Louisiana utilized EonCoat’s Weldable Corrosion Protection on two of their bulk storage tanks. Honeywell is not alone in wanting to tackle this financially- and environmentally-costly corrosion.
Like the EonCoat Corrosion Protection and the EonCoat Corrosion Under Insulation (CUI), the EonCoat Weldable Corrosion Protection forms an intimate bond with the carbon steel substrate and alloys to the carbon steel. Therefore, the EonCoat Weldable Corrosion Protection has the same dual layers of protection – one layer of iron phosphate and one layer of ceramic coating that creates the reservoir of inhibitor.
EonCoat Weldable Corrosion Protection can be applied at the fabrication shop. The asset can then be transported to the tank site. In the alternative, because EonCoat has a wide range of weather application standards, you can also apply the EonCoat Weldable Coating onsite as the tank is field erected.
Unlike anything else in the protective coating industry, EonCoat Weldable Corrosion Protection is heat-rated up to 600°C (1112°F) and will not burn because it is non-flammable. Essentially, EonCoat Weldable allows carbon steel to be protected:
- before the weld,
- during the weld, and
- after the weld.
The protection begins before the weld. Once the surface preparation requirements are met, and the EonCoat Weldable is applied, the carbon steel asset – in this case, a panel of the soil facing side of the tank bottom – the corrosion protection is in place with full efficacy and protection integrity.
The carbon steel is protected during the weld because the protective coating does not burn off. Unlike paint which burns off and leaves a void allowing corrosion to begin immediately, EonCoat Weldable does not burn off. The non-flammable nature of EonCoat allows the full efficacy and protection integrity of the corrosion protection to remain in effect.
Protection after the weld is unlike anything else on the market! EonCoat Weldable Corrosion Protection allows your typical lap and butt welds to be easily applied without damaging the carbon steel or protective coating. Additionally, the welder and fitter can fabricate both plug and seam welds.
EonCoat’s 30-year warranty is effective on the Weldable Corrosion Protection product when applied by an EonCoat Certified Applicator. The 15-year life expectancy for a soil-facing side of the tank bottom that we referenced earlier just grew to a 30-year (minimum) life expectancy. That’s a 100% increase in the amount of time one tank bottom can be utilized. The use of EonCoat Weldable Corrosion Protection also eliminates the need to double the thickness of the tank bottom.
So, while decreasing the initial cost of carbon steel for the soil-facing side of the tank bottom, EonCoat Weldable also increases the life cycle by 100%. That’s a return on investment any tank owner is happy to have. If you’re interested in learning more about EonCoat Weldable Corrosion Protection, feel free to download our FREE E-Book.
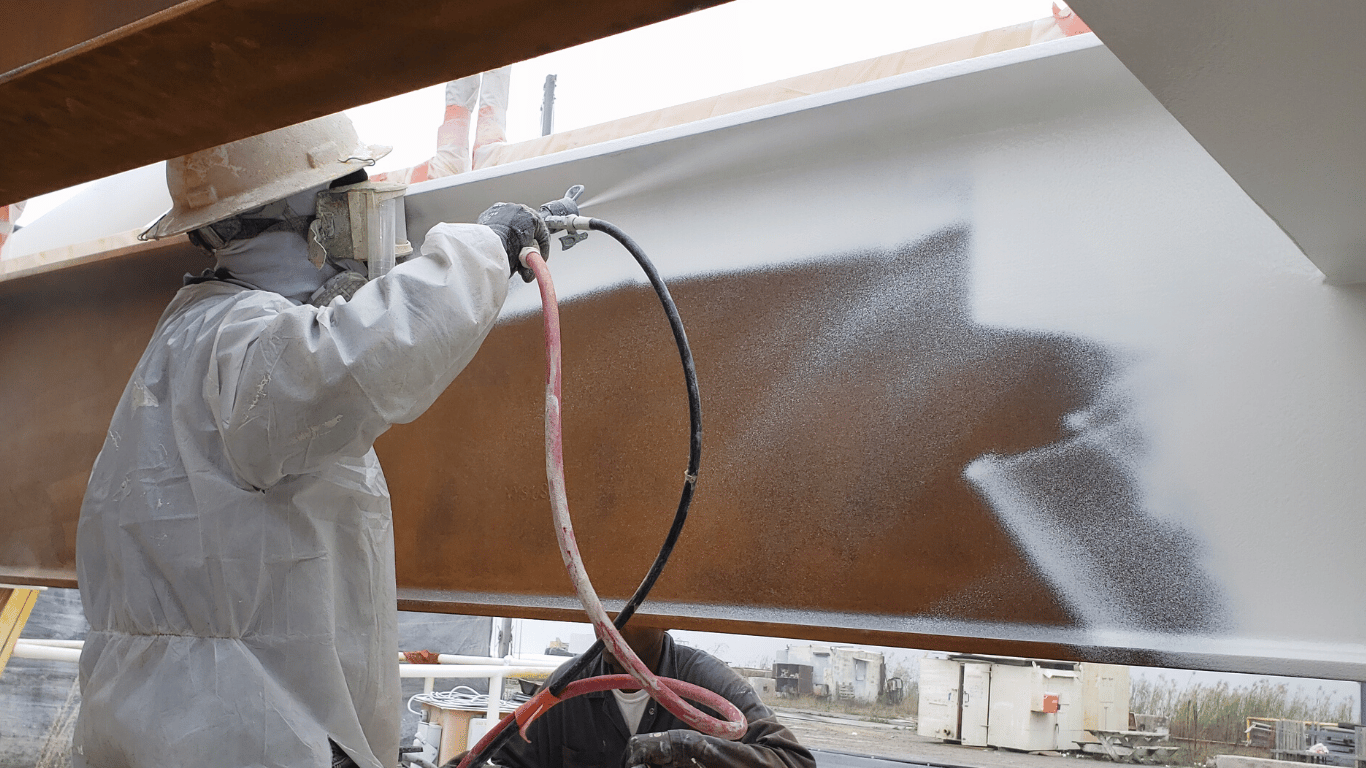
Ready to Learn More About EonCoat?