June is National Safety Month
In 1996, the National Safety Council established June as National Safety Month. They have as their goal to “eliminate workplace fatalities with emerging technologies .” That’s a great goal, but why are we still talking about it 25 years later? We have immense respect for the education, outreach, and advocacy work the NSC is accomplishing. But, while we applaud the statement at face value, we have deeper questions.
- Why wait until 2050?
- What can we as a company – and a leader in the protective coatings industry – do to close that time gap for our employees, EonCoat applicators around the globe, and others in the protective coatings industry?
- Why are other paint and coating companies not working to eliminate VOCs, HAPs, and TOXINs?
Situational Risks or Systemic Risks?
Wisely, the NSC identifies work safety into categories of Hazardous Situations. They go a step further by defining contributory factors as either Situational Risks or System Risks. For situational risks, we had to hunt for anything resembling applicator or painter safety. There are no obvious online links for inhalation injury or long-term effects, such as painter’s dementia. The closest categories for anyone in the coatings and paint industry are Repair and Maintenance, Construction and Installation, Confined Space Entry, and Hot Work. Roughly tabulated, the painting and protective coatings industry could contribute to 4 out of the top 18 hazardous situations. We can be better than that. We have got to be better than that.
If you stop and examine NSC’s Systemic Risks, that’s when and where you see so much of what plagues our industry. Clearly, the most significant contributory factors to fatalities in our industry are:
- lack of training or supervision,
- leadership failure,
- lack of workplace awareness, and
- improper PPE.
Our Industry Already Has The Technology To Prevent Certain Deaths
As the NSC has clearly stated, we need to use emerging technology to eliminate these deaths. In our industry, we already have the technology to eliminate many of the deaths and long-term debilitating illnesses our employees suffer by eliminating VOCs, HAPs, and toxins. Simply stated, many of our fatalities are largely due to our lack of leadership – because the solutions already exist.
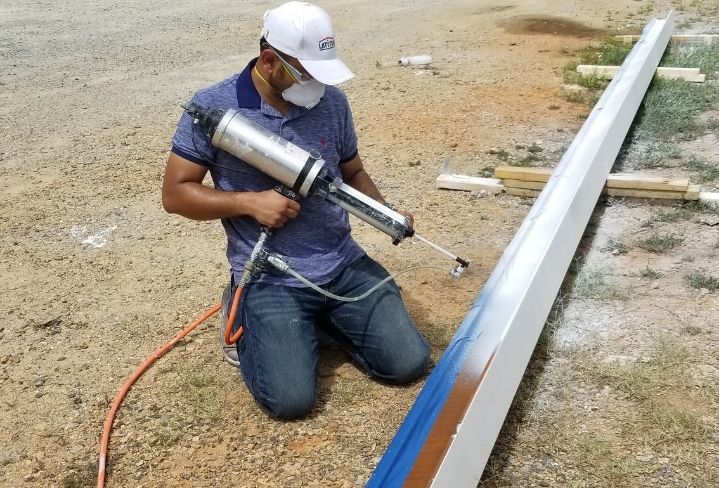
Our Call To Action
EonCoat is calling for each Company President, CEO, CFO, and CSO in the paint and protective coatings industry, as well as their large users, to move at a rapid pace and with the intent to eliminate VOCs, HAPs, and toxins. Treat worker safety as a right, not a privilege.
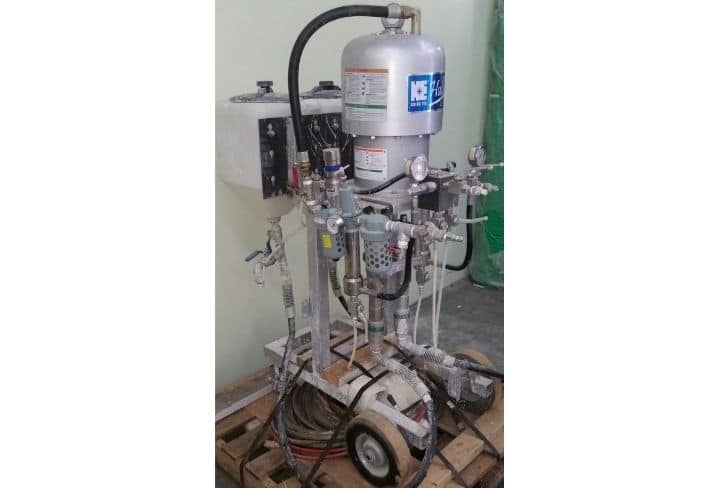
What Rights Do Workers Have?
Let’s review workers ‘ rights to ensure we’re all on the same page. According to Safety Stage, employees have the right to:
- Receive health and safety training at work in a language they understand
- Work on safe machines
- Receive all required safety equipment and PPE (personal protective equipment)
- Be protected against toxic chemicals
- Request an OSHA inspection
- Report workplace injuries or illnesses
- Review records of work-related injuries and illnesses
- View the results of workplace hazard tests
Are The Paint and Coating Industries Still Dangerous?
If you’re asking how prevalent it is in the 21st Century to have dangerous paints and protective coatings, let’s look at a few key examples. Sherwin Williams Company was ordered to pay out $101,666,667 in 2019 because they manufactured paint products that contained lead – a known VOC -when lead in paint was already a known and clear public health crisis.
According to the Oakland City Attorney, Barbara J. Parker,
“Lead paint is prevalent in Oakland homes and disproportionately impacts African American, Hispanic, Asian, and other communities of color and low-income communities. In this case, the defendants knew they were selling a product that poisoned children, yet they continue to market it as safe and sell it on a massive scale – in fact most homes built before 1978 contain lead paint hazards. These funds will make it possible to clean up the homes of our most vulnerable residents, and the settlement reaffirms that these companies are accountable for the harm their products continue to cause to California’s children.”
Sherwin Williams knew, “In 1904, a French expert was quoted in Sherwin-Williams’s monthly publication as finding the paint to be ‘poisonous to a large degree, both for the workmen and the inhabitants of a house painted with lead colors.'” The US didn’t ban lead-based paints in new construction until 1971. It wasn’t until 1977 that the US Consumer Product Safety Commission banned the use of lead paint in residential and public properties and its use on toys and furniture. That means Sherwin Williams knew the lead paint was dangerous for 73 years but continued to manufacture and market lead-based, dangerous paint. Sherwin Williams was penalized for doing something while it was legal – but already knew it was dangerous.
Don’t think for a moment that Sherwin Williams stands alone. You don’t have to search hard to locate other examples:
- Chevron was ordered to pay $21.4 million in damages to the families of two brothers, Gary and Randy Eaves, after they were exposed to benzene – a VOC and known carcinogen – while working at Cooper Tire and Rubber. Gary died from non-Hodgkin’s lymphoma, and Randy died from acute myelogenous leukemia. Both brothers were only 59 when they were diagnosed with their respective illnesses. That’s too many and too young. Reportedly, none of the people at the plant handling or near the benzene wore protective respirators or clothing. Even scarier is the claim that they “were never advised to handle benzene inside a ventilation booth.”
- Samsung reportedly paid close to $15.3 million after 320 workers at a semiconductor plant developed illnesses after exposure to VOCs. “Benzene, trichlorethylene (TCE) and methylene chloride are VOCs used widely in semiconductor and electronics manufacturing and are associated with cancer, nervous system damage and are also known to affect developing embryos.” That’s too many.
- Benjamin Moore, YOLO Colorhouse, and Imperial Paints were taken to task by the FTC. These companies deliberately misled consumers by labeling their products incorrectly and making false or unsubstantiated claims in their visual and print advertisements. Apparently, you aren’t supposed to make false claims about being emission-free or containing zero VOCs – when in fact, you contain VOCs! One Benjamin Moore ad even showed a nursery being painted while the baby slept in a crib during the process. That’s too young and too many gallons of intentionally mislabeled paints.
- Home Depot was ordered to pay $8 million to settle a lawsuit for violating California’s limit on VOCs per liter for tens of thousands of liters of paint, sealer, primer, and other coatings. Our readers from California can appreciate the limit on VOCs because they directly contribute to smog. That’s too many liters and VOCs.
Is The Painting And Protective Coating Industry The “Next Big Tobacco”?
These cases should be a clarion call to all of us in the coatings business and to the industrial customers who hire us. We know that VOCs are harmful now and can have long-term adverse side effects in those exposed regularly. So why are companies not making the transition away from VOCs, HAPs, and toxins?
Knowing that something is dangerous but continuing to manufacture and market it clearly falls under the National Safety Council’s definition of lack of leadership that contributes to work-related injuries, long-term health problems, and eventual death. Knowing something is dangerous and continuing to manufacture, market, and sell is how things progressed with big tobacco and asbestos in our nation’s past. If the paint and protective coatings industry doesn’t change how it engineers and applies products, we will be the next “big tobacco.”
As Leaders In The Paint And Coatings Industry, What Can We Do To Eliminate VOC, HAP, And Toxin Exposure?
As leaders, we can start at the beginning – and in doing so, we can change the outcome. Utilizing plural pump application enabled EonCoat to be engineered to eliminate VOCs and HAPs. We don’t own the patent to plural pump engineering and application. Anyone can use this readily available technology for applying their paint or coating and, by the nature of the design, eliminate VOCs and HAPs. Imagine being the person who is applying a protective coating in a confined space and hoping that what you’re applying is safe. Now imagine being in the same confined space and applying EonCoat. You know it is safer because the manufacturer has eliminated VOCs and HAPs.
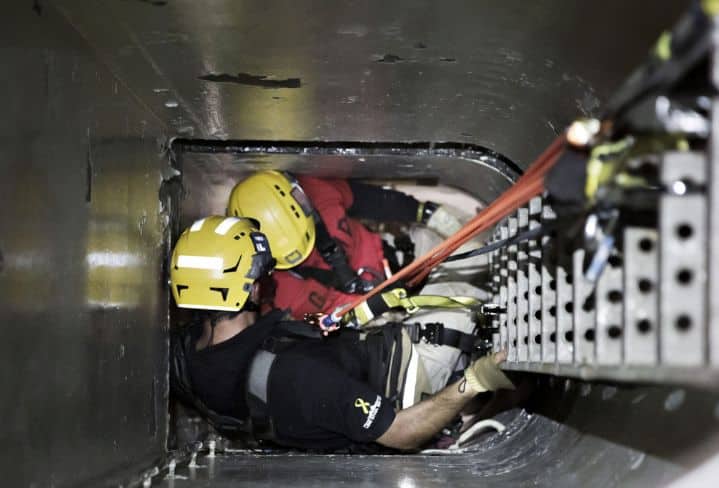
As leaders, we can ensure that we have corporate policies and practices that result in everyone applying Eoncoat wears a dust mask capable of filtering solid particles. A simple N95 mask is sufficient. EonCoat is a solid suspended in a liquid. As it is applied, it almost resembles dental cement in its texture, density, and feel. The goal is to keep out any solid particles (not micron-sized particles such as viruses and bacteria).
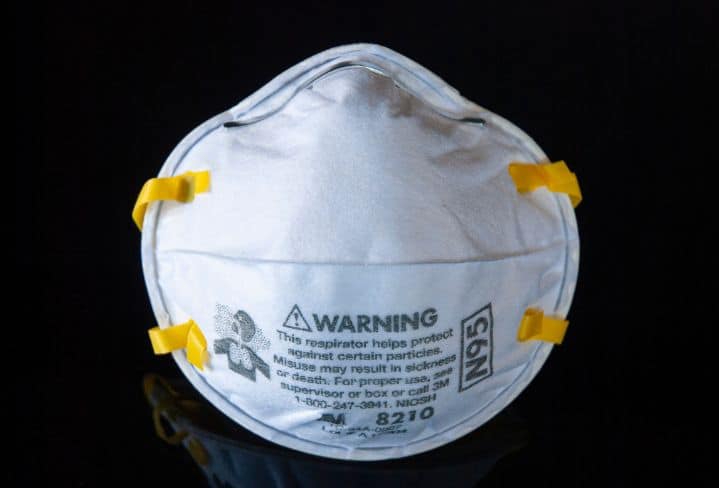
As leaders, we can alter our protective coating to eliminate the use of harsh solvents or chemicals in the clean-up process after an application job is complete. After applying EonCoat, water is the only item needed to clean the tools and equipment. You can dispose of any leftover, wasted, or dry fall EonCoat the same way you dispose of any cementitious product.
As leaders in the coating industry, we have specifically engineered EonCoat to be applied at ambient temperatures. Compare that to TSA’s requirement to be thermal applied up to 3,100°. So that one is simple – where would you rather spend the day? Would you want your child to get a job at a site that manufactures thermal-sprayed aluminum?
As A Leader, What Is Your Next Best Step?
If you have a question about how EonCoat can permanently protect your carbon steel asset and make it safe for your employees who work in applications, feel free to reach out to us or call us at 754-222-4919.
If EonCoat is not the right option for protecting your carbon steel, please demand better from your vendors! Source and engage with a vendor who uses plural pumps to eliminate VOCs, HAPs, and Toxins. Source a vendor who has eliminated harsh chemicals and solvents in the clean-up process. Source a vendor that can have reduced PPE needs because their products and processes are safer. Source a vendor that doesn’t expose applicators to high temperatures. Start at the beginning, so you have a different outcome – source a vendor that leads.
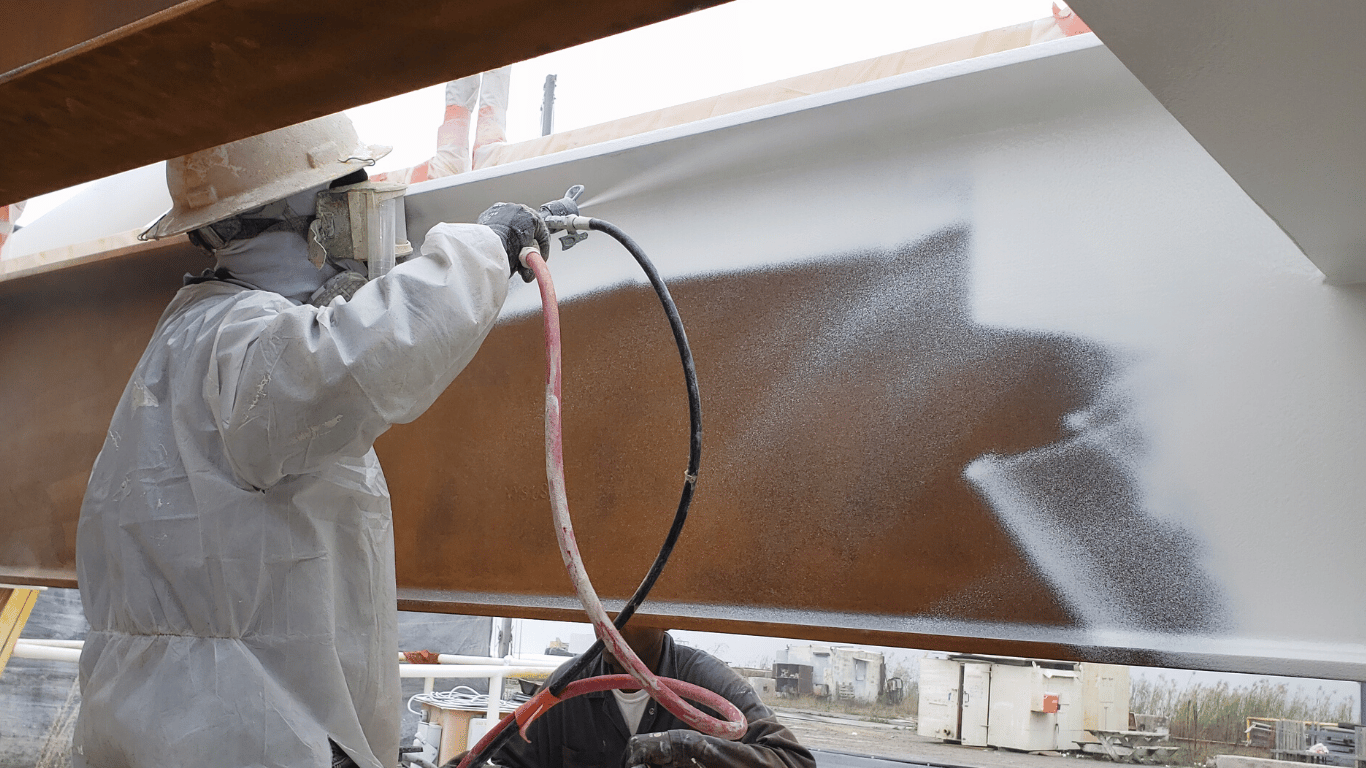
Ready to Learn More About EonCoat?