THE QUESTION WE MUST ASK AND ANSWER EVERY TIME
Everyone in the protective coatings industry spends a great deal of time evaluating coatings with formal test protocols and field testing. We do this to ensure application, lifespan, and performance integrity. What tests we should run, how to run them, and how to correctly interpret the data are constant topics of conversation and debate. Those of us in NACE (now AMPP) and the other associations work to get better results for our customers. That should always be the goal.
It is appropriate that we design test protocols specifically intended to evaluate the type of coating we are considering or applying. It is common for different coatings to perform better or worse in different kinds of tests.
Here is the hard part and what should be our constant focus – will the coating meet the customers’ needs for the specific application under consideration? Too often, we forget this vital question. We try to apply what has become our favorite test to ALL coating systems without carefully considering if the test protocol leads us to the situation-specific correct conclusion. If we lose focus on the customer- and application-specific question, we fail to analyze carefully and truly understand the results of how this product will perform for a specific customer in a specific application.
AT EONCOAT WE ARE ALWAYS ASKING, TESTING, AND LEARNING
Early in the development of EonCoat, I saw an example of how to test coatings and analyze results the right way. When Chevron was considering EonCoat, they tested 100’s of EonCoat protected panels at different thicknesses, applied on different substrates, and with various levels of surface prep. When Charter Labs finished the testing Dr. Benjamin Chaloner-Gill brought the results to our lab to review. Page after page showed EonCoat cracking due to UV exposure in the weathering chamber. We later found that one of the fillers we were using at the time absorbed UV. As an unforeseen consequence, this created extreme heat, which caused the cement to generate shrinkage cracks due to the loss of bound water at high temperatures.
At the time, our team of scientists and I were sick that we had failed so badly in front of a potentially lucrative customer. Who wouldn’t be? However, Dr. Chaloner-Gill showed us – literally and figuratively – that we were missing the relevant point. With hundreds of tested and now cracked panels, there was not a spot of red rust, despite all the cracking. One of the nice things about working with very smart people is that they look beyond the obvious to understand the bigger picture. We needed to change the UV absorbing filler, and we would have a winner with EonCoat.
A prime example of test results leading to poor conclusions is galvanizing. If we evaluate galvanizing by its results in salt fog, it would never be approved for service. Yet the galvanizing market is five times the size of the total protective coatings market. People found its value before we developed ASTM B117. We should learn humility and patience when designing test protocols and evaluating the results.
Because of the huge volume of polymer coatings available, many have become comfortable thinking only about polymers for corrosion protection. This comfortability leads to standardized test protocols intended to evaluate the behavior of polymers. Unfortunately, this narrow focus has multiple shortcomings. The worst outcome is that we award good marks to a good polymer product but may not provide the outcome that is important to the end user – like permanent corrosion protection for carbon steel.
Examples of things that we evaluate that may not be relevant include gloss. We like glossy polymers because they are aesthetically attractive. How valuable is measuring gloss in considering corrosion protection?
WHAT QUESTION DOES TESTING DUCTILITY ANSWER?
Another example of testing that is sometimes irrelevant and often misleading is ductility. Polymers are inherently good at stretching, and manufacturers like to highlight that. But is 200% ductility important when coating steel, with a maximum ductility of 36% and a practical maximum of 1% before permanent deformation? It is fair to say that ductility is significant when bridging gaps, so there may be instances when the measurement is important.
The manufacturers always fail to mention that they measure the ductility of a new polymer coating. Exposure to UV significantly degrades the ductility of a polymer. When we look at a five-year-old paint chip, it is brittle – it has almost no ductility. So, isn’t it a bit misleading to brag about having high ductility when that will only last a short time for a protective coating? Isn’t the goal of a coating to last more than a short time?
Inorganic materials, like EonCoat, have lower ductility, but the ductility remains the same for the life of the product. With EonCoat, permanent ductility is 19%. This measurement is well beyond what is needed for steel since engineers don’t design steel assets to bend beyond the point of permanent deformation – 1%.
WHAT QUESTION DOES PULL-OFF STRENGTH ANSWER?
Perhaps the most misunderstood measurement that almost every customer asks about, and every lab performs, is adhesion. Less than 1% of the people who ask about Pull-off strength can answer the question, “does coating pull-off strength matter”?
If you are reading this and know why it is important, you are a knowledgeable coatings person. If you don’t know, adhesion is important because it measures the resistance to osmotic pressure. If salts are under a coating, they will pull water through the polymer. This water builds pressure underneath the coating and tries to push it off the substrate and create blisters. The osmotic pressure can exceed 2000 PSI. So we want a polymer to have that much adhesion so it cannot form blisters.
Cementitious coatings, like EonCoat, are porous. Water pressure cannot build underneath the cement because the water flows through it easily. Therefore, any adhesive strength greater than the few PSI required to hold the weight of the cement is of no practical value. Yet some standards will fail a coating system if the adhesive strength is below a certain number. This standard violates the objective we stated earlier – will the coating meet the customers’ needs for the specific application under consideration? How do we test for that? There are multiple cases of passing a coating that will not meet the customers’ needs, all while failing coatings that will meet the customers’ needs. These seemingly different outcomes are because of a subjective standard that does not answer the original question – what are the customers’ needs and will this product meet those needs.
WHAT QUESTION DOES HOLIDAY TESTING ANSWER?
One of the most popular post-coating tests is Holiday testing. Holiday testing is a non-destructive test method applied on protective coatings to detect unacceptable discontinuities such as pinholes and voids. The test involves checking an electric circuit to see if current flows to complete the circuit. What is disturbing is that this is a primary method of determining the quality of a coating system. Yet all it really tells us is that we don’t have a hole in the polymer. We test at relatively high voltage as if that means anything. The voltage necessary to create corrosion is quite small – less than a volt. But we sell Holiday testers that measure up to 40,000 volts. The high number of volts makes us feel that we have an excellent coating but ignores the fact that the corrosion takes place underneath the polymer. Having a good insulator that has moisture and salt underneath does not provide great corrosion protection. Yet somehow, we feel good after a successful “jeep test.” This test is another example of not measuring what is relevant.
We see these testing flaws in many industries, and cement is not exempt. The code requirements for many building materials are prescriptive vs. performance-based. It takes volunteer organizations like the American Concrete Institute (ACI) about 14 years, on average, to approve new products and write them into the often prescriptive- vs. performance-based code. As a result, there has been little development of new technology in the concrete industry. From a corporate perspective, why spend the money on R&D if it may take a decade before you can sell your product.
WHAT TAKES SO LONG?
These long-persevering rules serve the entrenched vendors at the expense of the public, all while appearing to provide a public service. The result is that our primary building material, Portland Cement, was created in 1824. While there have been additives, the basic material is much the same. Compare that to the improvements in electronics, microprocessors, and programming that are not code regulated. We have had slight improvement in our most basic building material in 200 years because of the code – not because there are no intelligent people in the building industry. This lag in approval timeframes is a reason to be suspicious of any testing protocol designed around a specific material rather than a specific objective.
WHAT QUESTION DOES EONCOAT ANSWER?
To be fair, it is a challenge to measure what matters to successful corrosion protection in a field environment. What matters most is providing a sufficient volume of inhibitive pigment to enable the metal to protect itself and bond those inhibitors directly to the metal. Eliminating the access of water to the substrate would also be a good alternative – but as of today, there are no completely impermeable coatings. Therefore, complete elimination of moisture at the metal interface is not currently possible.
We can offer EonCoat, which does provide a sufficient volume of corrosion inhibitors to permanently protect your carbon steel in even the most corrosive environments. That’s what Chevron, NASA, and countless others have found. So, what problem are you trying to solve? Feel free to reach out to our Customer Success folks and ask if EonCoat is the right product for your carbon steel asset.
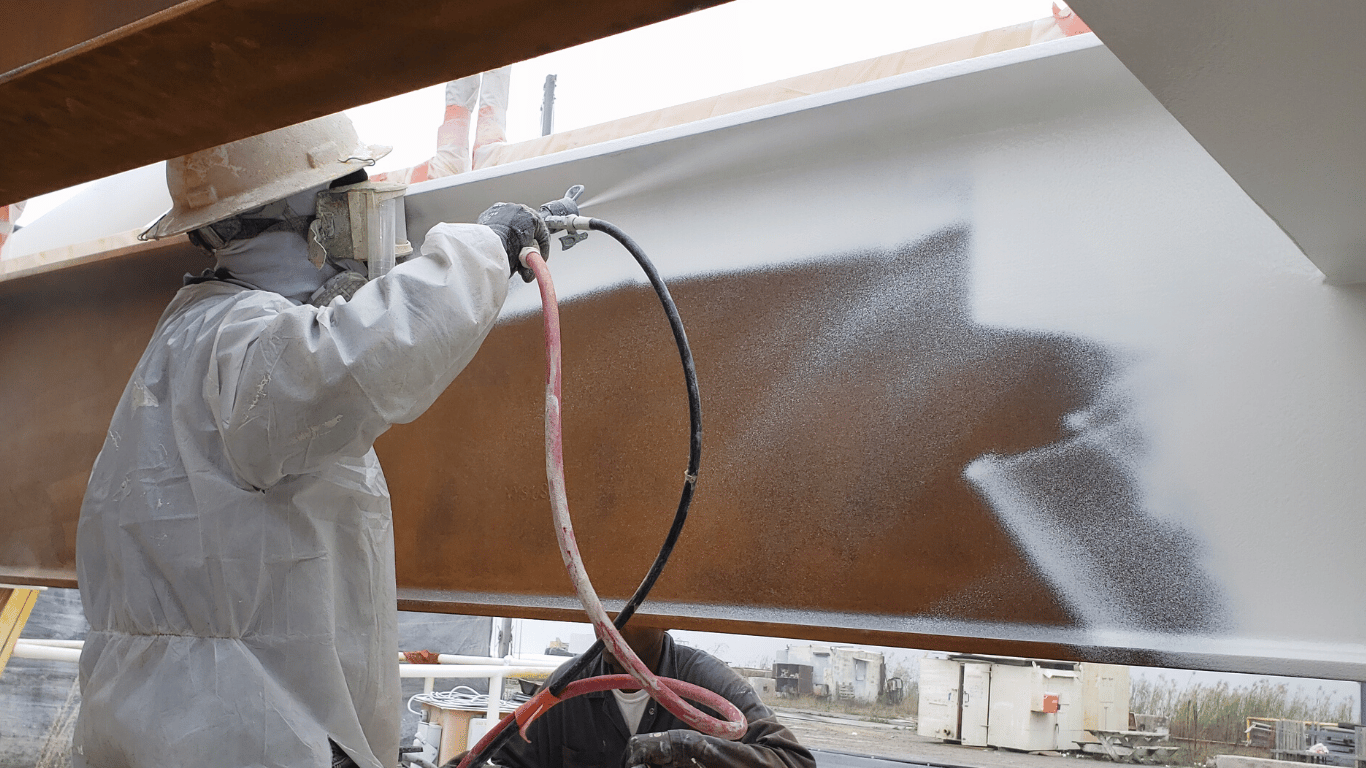
Ready to Learn More About EonCoat?