SOLVING RUST = WE ARE MAKING THIS TOO HARD!
Corrosion plagues the energy industry. Globally, the cost of corrosion is estimated to be $2.5 trillion annually – and this is before you factor in the employee safety and environmental costs into the equation. These high costs stem from maintenance, equipment downtime, asset replacement, and lost production, just to name just a few. For example, just the corrosion under insulation costs accounts for approximately one-half the pipe maintenance budget.
Each company in the industry has experts that are incredibly knowledgeable about the effects of corrosion, the varied unique mechanisms by which it occurs, and the many complex techniques to mitigate it. Unfortunately, as is the case with many things in life, by not understanding and focusing on the root cause, we make the problem of corrosion more complicated than it needs to be.
Listening to folks talk about the intricate details and complications reminds one of an accountant talking about tax strategies – the eyes glaze over. For example:
- corrosion cells
- stress corrosion cracking
- intergranular corrosion
- Galvanic corrosion
- crevice corrosion
- filiform corrosion
- fretting corrosion
- cavitation corrosion
- cathodic protection
- anodic protection
- mill scale
- concentration cells
- yellow, brown, and black rust,
- blast profile
- painting “conditions.”
You get the eyes-glazed-over point!
The most important thing that the Georgia Institute of Technology taught me is that reducing the problem to its simplest form often causes the answer to fall out. When you reduce corrosion prevention to its simplest form, EonCoat falls out of the mix and rises to the top as the permanent corrosion solution for carbon steel assets.
Solving Rust = Preventing Rust
Preventing Rust is about stopping the loss of electrons. In this article is everything you need to understand rust – and how to permanently prevent it. Rust is a simple thing that is only made difficult when we talk about the complexities of things like galvanic corrosion, microbial-induced corrosion, and all the various technical details of applying a coating without understanding why we do it. However, if we forget about the complexity and focus on the basics, the problem becomes easy to solve. Corrosion happens when a carbon steel atom loses an electron and bonds with oxygen to restore the charge imbalance.
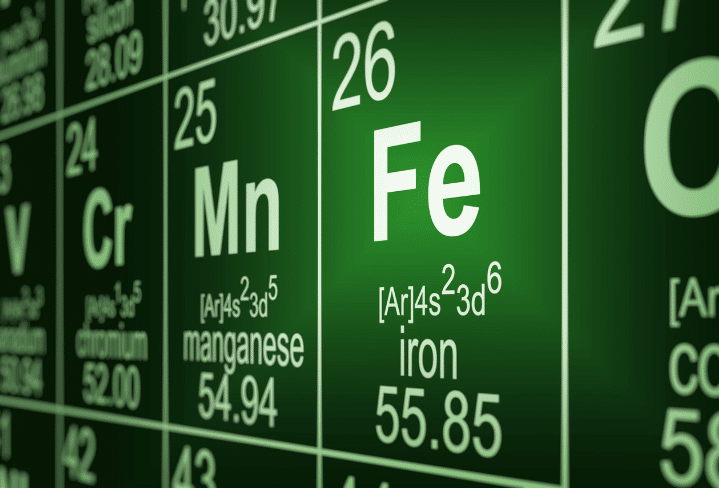
That is the root of ALL corrosion. For carbon steel, this process is called rust. It is as simple as that. Figure out how to stop electron loss, regardless of why it happens, and there will be no rust.
Solving Rust = Understanding the Problem
By definition, metals are good conductors of heat and electricity. They have these properties because they readily share electrons. Electrical current is just electrons moving in a path from high to low voltage.
This sharing of electrons makes extraordinary things possible, like electricity. Each atom gives electrons to the next atom in line and then accepts electrons from the atom behind it in the chain. Everything goes swimmingly until an atom loses an electron. Then there is a net shortage of electrons, and everything goes wrong after that. If the iron atom that has lost electrons bonds with oxygen, you get rust.
Solving Rust = Stopping Electron Loss
If the problem is the loss of electrons, how do we stop it? We do not want metal to stop sharing electrons – it would no longer be metal if it did that.
Could we electrically insulate it somehow so the electrons travel down the middle of the metal but cannot leave the surface? EXACTLY!
Could we feed the metal a constant stream of electrons so no atom ever runs short on electrons? THAT WORKS TOO!
Supplying a constant stream of electrons to a metal is called Cathodic Protection. There are several ways to do that. One method is to hook up a DC voltage to the metal with a wire and pump electrons down the wire to keep a slight negative charge on the metal. Cathodic protection works well, but you have to replenish the supply of electrons at an ongoing cost.
Another method is to electrically connect the metal to a different metal that likes to give up electrons even more than the metal you want to protect. The downside is that the quality of the protective metal becomes sacrificed even faster. Examples include adding zinc anodes to boats or pipelines or adding a layer of zinc directly to metal in the form of a coating – known as galvanizing.
Insulating the metal can be a better solution, and like Cathodic Protection, there are several ways to go about it. A pretty common way to insulate is to cover the metal with a plastic sheet called paint. The plastic layer is an insulator. This method significantly reduces the loss of electrons until water seeps through the paint either through permeability (all paints are permeable to some extent) or through a scratch or flaw in the paint film.
Solving Rust = The Science
A more permanent method of insulating steel is to form an alloy over its entire surface. We must create an alloy that does not share its electrons for this to work. In other words, the alloy must be non-conductive. Fortunately, there are several effective ways to do this. Take, for example, the poor atom that became short of electrons. The atom cannot be happy until it finds a replacement electron. The atom will bond with WHATEVER satisfies the need and takes the LEAST AMOUNT OF ENERGY!
In the case of the atom, this means bonding with another atom (or molecule) that has extra electrons it is willing to share. This new partner can be one of two types. One type will form a stable partnership that is welcome in the community of other similar atoms forming the metal, and this is an alloy. The second type is a partnership that is not as stable and will not become part of base metal. That unstable base metal is called corrosion – or rust.
Examples of stable alloys include positively charged iron (Fe) bonding with negatively charged phosphate (PO4) – resulting in iron phosphate (FePO4) or one of its derivatives. Of course, there are other choices besides phosphate, but phosphate is a particularly good one. For simplicity, we will use the option of phosphate for this article.
There are also stable oxide bonds. For example, the chromium in stainless steel forms an amorphous layer of chromium oxide. The amorphous oxides stay bonded to the base metal and protect it. This is also possible with iron, but a catalyst is required to convert the iron oxide crystals to amorphous. Examples of unstable bonds include iron combining with oxygen – resulting in a crystalline iron oxide (FeO, Fe2O3, or Fe3O4), and these are the various forms of rust.
As described, the Fe ion chooses which of these to bond with, based on what reaction takes the least energy. Engineers quantify the energy of formation using something called Gibbs Free Energy. We do not need to explain Gibbs Energy here but accept my word that the more negative the Gibbs Energy of a Reaction, the more likely it will happen. For example, the Gibbs Energy of the reaction of oxygen with iron is not as negative as the reaction with phosphate. Therefore, if sufficient phosphate is present – the Fe ion will choose to bond with phosphate instead of oxygen. In the process, we get an insulation layer of iron phosphate that is not conductive in nature and does not give up its electrons.
Solving Rust = The Permanent Solution
All we must do is put soluble phosphate next to steel in an aqueous environment, and it will create its own alloyed layer. The higher the phosphate concentration, the better this works, and the more corrosive environment the metal can endure and stay protected.
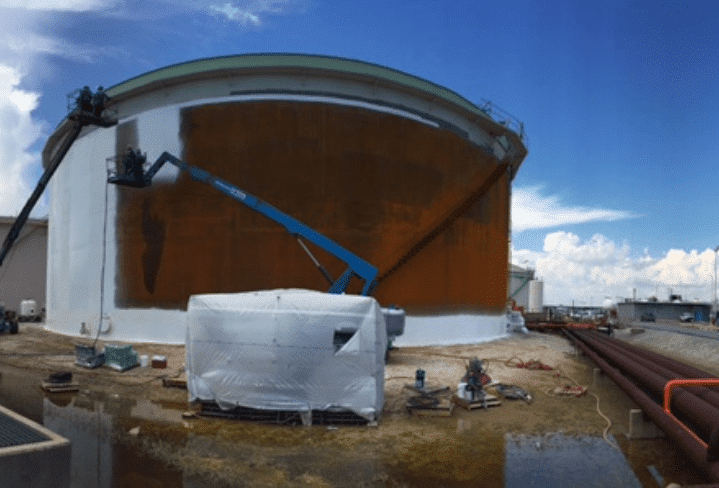
Many years ago, paint companies, recognizing the limitations of the plastic barrier, began employing both insulating methods mentioned above. They encapsulated phosphates in the plastic barrier. While the idea was a step in the right direction (polymers containing inhibitive pigments do work better than those without), the encapsulation of the pigment in the gooey resin of phosphates in a plastic barrier is counterproductive. The phosphate must fight its way out of the resin to reach the carbon steel to form the alloy. Additionally, adding a large enough volume of pigment to be effective in a highly corrosive environment is impossible. From a practical standpoint, polymers can hold only about 20 percent inhibitors.
It would be more effective to bond the phosphate directly to the carbon steel without all the gooey resin. Some years ago, the scientist at EonCoat figured out how to do precisely this! EonCoat enables 100% inhibitive pigment right next to the metal.
EonCoat works! You can still add a plastic barrier (known as the paint color of your choice) outside the pigment if you like. However, if there is a thick enough phosphate layer, the plastic barrier is only needed for appearance.
Solving Rust = Evidence of Efficacy
Here is some proof that this is all correct and that the solution we propose works when applied in laboratory and real-world conditions:
- NASA did an experiment whose results shocked the coating industry. The study was conducted in 2013 – 2014 with the goal of finding a coating that had excellent corrosion protection properties, the lowest impact on the environment, and no zinc, heavy metal, or isocyanate. The results showed that the newest competitor on the block, EonCoat, was the clear winner. In 60 years of testing at the Cape, the highest score ever on a scale of 1-10 had been a 9.2. In this test, EonCoat received the first-ever 10.
- Chevron presented a paper to the Society of Petroleum Engineers in 2018 detailing their successful study- and use of EonCoat. Chevron conducted the study over three years, both in the laboratory and in-field testing and at two drastically different geographic and environmentally distinct locations. The takeaway from that study is simple, as demonstrated by the statement, “EonCoat provides an attractive solution that facility operators are seeking.”
- The US Department of Transportation has oversight of the Federal Railroad Administration, which funded research and testing performed by EWI (previously known as Edison Welding Institute), headquartered in Columbus, Ohio. Their findings state clearly that “A commercially available inorganic conversion coating (EonCoat®) was effective in preventing corrosion in saltwater environments. It enabled extended fatigue life, even on damaged rail subjected to aggressive corrosive environments, and gave performance similar to that for undamaged, uncorroded rail.”
EonCoat has taken the high cost of rust and the need for carbon steel to have permanent corrosion protection to its most basic level – an electron. In getting to this point, the Research and Development Team engineered all three products with the environment, applicators, and your budget in mind. As a result, EonCoat has no VOCs, no HAPs, and no TOXINS. In addition, because EonCoat is an inorganic, water-based product, it does not endanger the environment and does not have costly cleanup. Finally, one coating of EonCoat applies everything your carbon steel asset needs and has a 30-year warranty. Would you like to know how much you’d save by applying EonCoat? Feel free to use our free calculator and start saving!
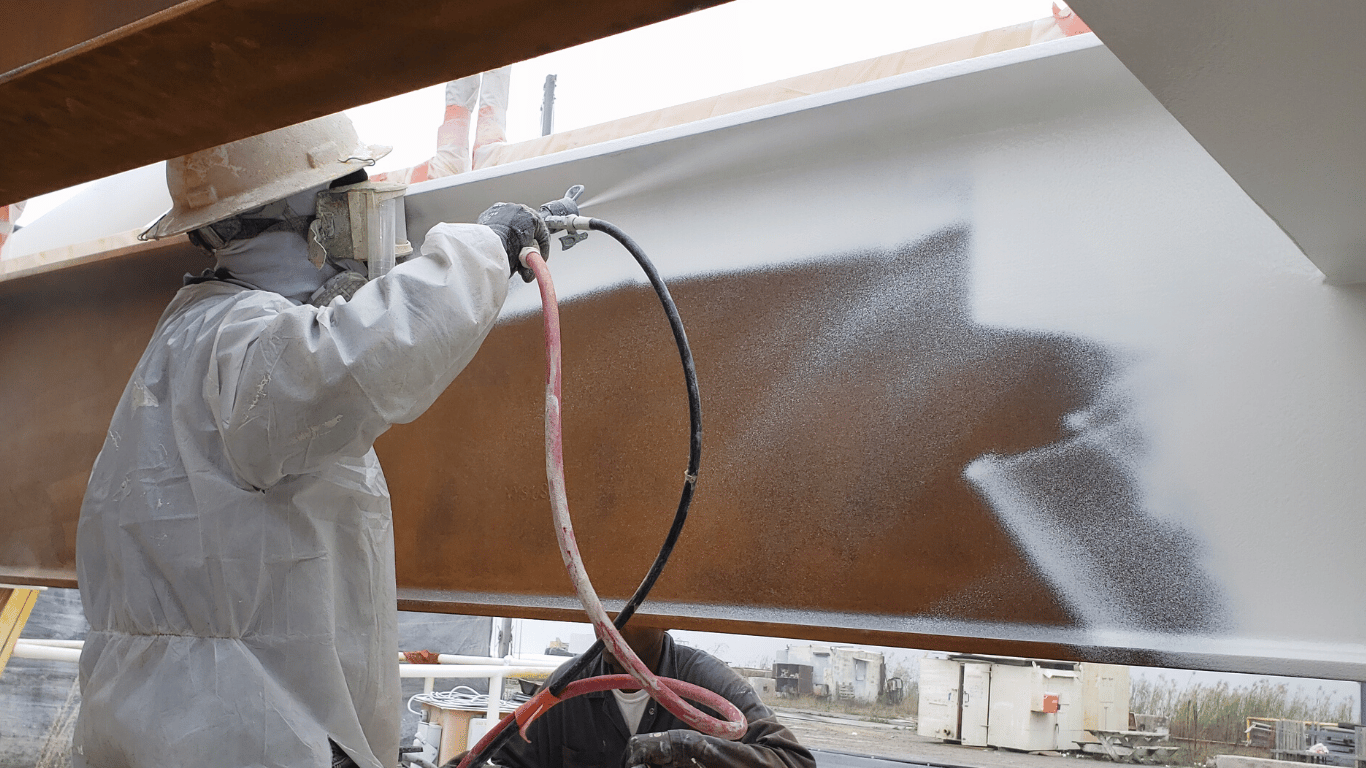
Ready to Learn More About EonCoat?